Speed counts: from configuration to service
Every functioning gearbox/motor combination is the result of a complex process – from configuration to operation. At the same time, speed and efficiency are required during implementation. Because both of these are decisive competitive factors in an environment that is becoming increasingly demanding from an economic point of view. As a manufacturer of planetary gearboxes, Neugart is reacting to this specific market requirement with a comprehensive overall package consisting of hardware, tools, supply chain and services.
Gearbox/motor combinations are used in many industries and applications, from automation to machining. And this usually takes place without problems and with the required result. However, a great deal has to have been successfully determined beforehand for the systems to operate problem-free. Because each individual phase of the process chain has specific requirements – and needs appropriate solutions: from planning and configuration to manufacturing, delivery and service during live operation.
Success factors during planning and configuration
At the beginning of every gearbox/motor configuration there is a specific drive task. The bigger the selection of gearboxes and suitable motors, the easier it is to actually find the optimum solution. The prerequisite for this is created if the gearbox manufacturer has an extensive portfolio – as does the compatibility of the gearboxes with as many motors as possible. Neugart fulfils these requirements with a sophisticated gearbox construction kit, which theoretically contains more than 2,500,000 possible combinations.
In view of this abundance, it quickly becomes clear that an expedient selection and configuration process can no longer be carried out manually. On the contrary, intelligent algorithms and smart tools now pave the way to the optimum gearbox. In this way, an experienced sales technician can create a new gearbox variant within a few minutes, generate the documentation that is required and also forward the work order to production immediately.
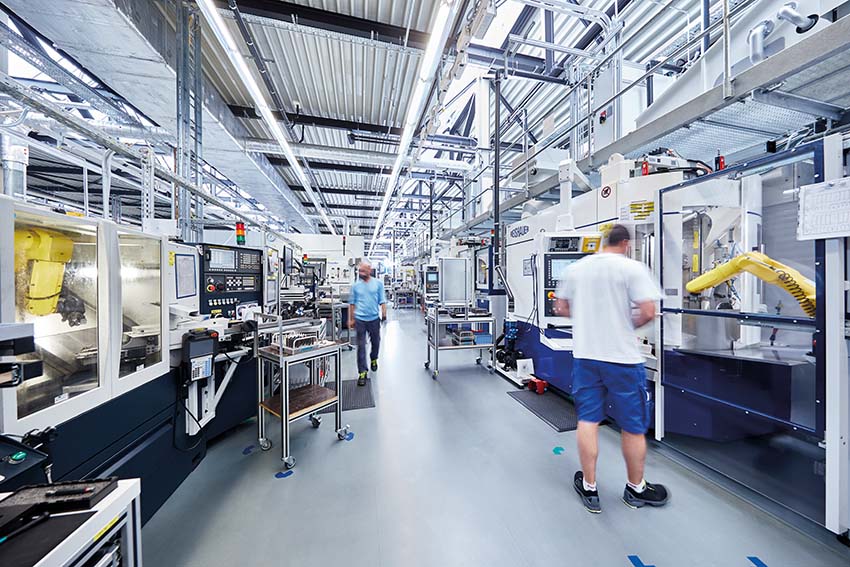
Faster configuration with tools
Things go even quicker if the customer has his own configuration tool. Against this background, Neugart has added two new powerful and intuitively operated software solutions to its range of free selection and configuration tools at Motek 2018: the Neugart Calculation Program calculation software in the current version 4.1 (NCP 4.1) for dimensioning and checking the application-related parameters; and the Tec Data Finder (TDF) for checking the geometric compatibility of the gearbox and the motor and the provision of CAD models and data sheets.
To put it briefly, the TDF quickly and easily leads to the right gearbox/motor combination, even on mobile devices, by only displaying the relevant matches. The selection process can start with the motor or the gearbox. Data for more than 17,000 motors from all of the most popular manufacturers are stored in the software. Up to five different gearboxes can be compared with other with differences within the technical data being marked, so that they are visible at a glance. This makes it possible to quickly detect which gearbox covers the technical requirements in an optimum way. After completing the configuration, the user at Neugart promptly receives CAD models and technical data sheets upon request. Applicable quotes are also produced if required. However, the NCP design software, which is also simple to operate, makes it possible to calculate the specific application case and determine the right drivetrain within a very short time. The basis for this is not only the intricate motor database, but also a wide range of specific applications and load cases such as rack/pinion, spindle, belt, conveyor belt, rotary table, thrust crank and various winders. The user receives suggestions for the optimum gearbox/drive combination for his application as a result. After designing the entire drivetrain, a comparison of the different designs leads to the most cost-effective and energy-efficient option. Furthermore, the software provides comprehensive technical documentation for every step of the calculation, and ensures that direct access is provided to the dimension sheets and CAD files of the selected products. For the user, this means a considerable amount of added value and a clear reduction in the amount of time that is required.
Success factors in manufacturing
When configuration is complete and the order has been submitted to the manufacturer, the manufacturer is required to build the required gearbox as quickly as possible and deliver it to the customer. Direct data transmission between the configuration tool and production accelerates the first step and avoids mistakes. The challenges then lie in the actual manufacturing. Here, digitization and new methods for increased efficiency now provide opportunities and possibilities that were unimaginable several years ago.
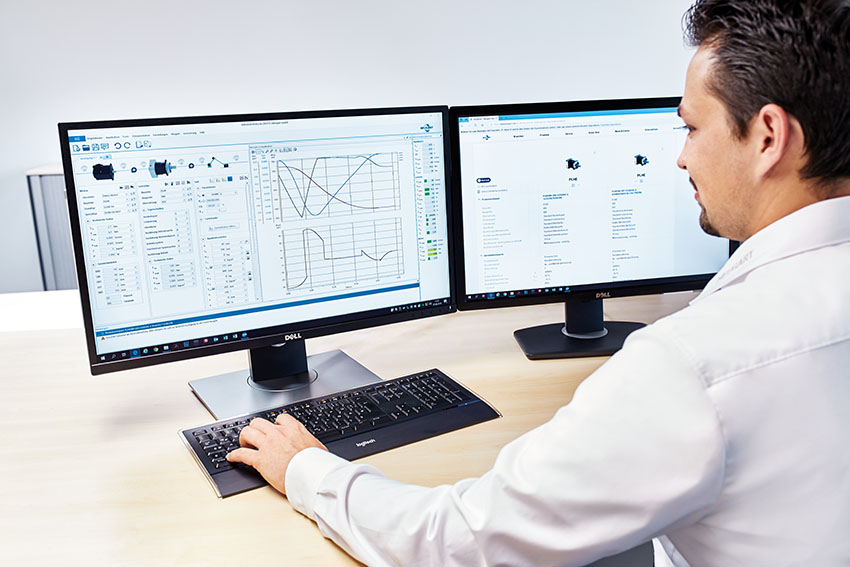
Neugart has therefore succeeded in considerably increasing transparency and reducing frictional losses by boosting the degree of machinery automation and digitizing processes. In a networked environment such as this, it is always clear what is being manufactured and when. Therefore, efficient resource usage can be maximized.
As another trend in the industry, quality has now become the standard to a large extent, and is subsequently expected. It is therefore a case of offering a wide range of products with short delivery times – and in the case of Neugart, this is for manufacturing batch sizes of 2,000 down to 1. The basis for the required flexibility and efficiency in production creates an internal supply chain, which consistently exploits the optimization potential with methods such as U shapes, route trains, SMED and Kanban.
Having sufficient manufacturing capacity is another success factor. Neugart is represented in important strategic locations in the world with three production sites, which reduces transport distances. The company has also increased its production capacity by 30 percent in the last twelve months. Planning is also currently in progress for an additional assembly plant over an area of 107,640 square feet at the German headquarters in Kippenheim. And essentially, particularly in a highly technical manufacturing company, it is the committed and competent employees, with their individual strengths, who ensure that customers are satisfied. During the course of systematic shop floor management, they are so networked with each other that even urgent customer queries can be coordinated between the different departments in a closely interlinked manner.
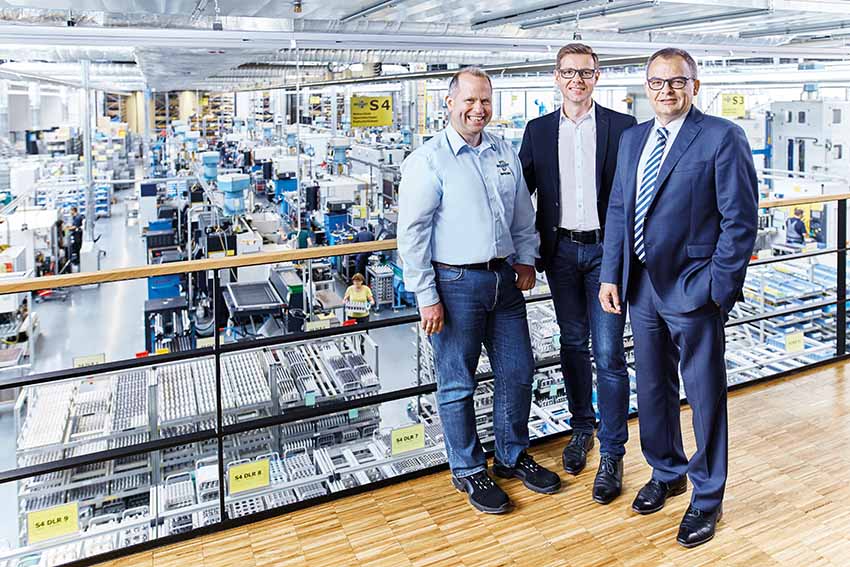
Success factors in the supply chain and live operation
Even the best, punctually manufactured product is only useful if it is in the right place at the right time. For this reason, carefully maintained master data for customers, products, suppliers and machinery required for production is necessary. This makes it possible to have optimally coordinated supply chain processes, which mesh with each other like the gearwheels in a planetary gearbox. This ensures that Neugart has not only a high degree of delivery precision but also the shortest delivery times – as quickly as 24 hours.
However, a really comprehensive gearbox/motor combination overall package does not stop when all components are finally operating with reliability of greater than 99.9 %: worse comes to worst, even with these highly available systems, every minute counts if disruptions are to be minimized. For this reason, the service department has also undergone further expansion during the course of the current optimizations. It is available around the clock via an online form, telephone or e-mail. Service employees, who remain the fixed contact for the customer until an inquiry is complete, perform function analyses and repairs or provide support during conversions. They also provide rapid assistance in the event of complaints, in addition to an in-depth cause analysis. And if it really has to be quick, spare parts can be delivered within 24 and 48 hours.
In view of the thousands of motor models on the one hand and an equally large selection of gearboxes on the other, the complex requirements of gearbox/motor combinations quickly become clear. Different success factors provide speed and efficiency in planning, implementation and operation at each point of the process chain. Long delays between the initial concept to the use of the optimum solution are therefore a thing of the past.