Microinnova Engineering is a specialist in innovative process technology, offering clients continuous manufacturing with an end-to-end solution.
Interview with Dr. Dirk Kirschneck, Strategic Director at Microinnova Engineering.
Easy Engineering: How do you see sustainability and what are your efforts in this direction?
Dirk Kirschneck: Microinnova focuses on resource efficiency for chemical reactions and chemical processes. It is our daily business to develop and realize efficient processes, mainly in the chemical and pharmaceutical industries.
E.E: Tell us about the sustainable solutions that you offer (if any).
D.K: Our chemical processing and manufacturing plants have a much smaller footprint than conventional plants and benefit from the optimization of mass and heat transfer. Our modular plant systems provide increased flexibility, capacity, and accelerated time to market through reconfigurable multi-purpose setups.
E.E: Do you offer solutions for reinvigorating old equipment with new solutions?
D.K: We follow a debottlenecking approach for optimizing conventional batch technology toward sustainability and efficient processing. A capacity increase of existing batch vessels can be reached by implementing continuous manufacturing units in existing batch environments. On-demand reagent generators can provide chemical reagents in an efficient way.
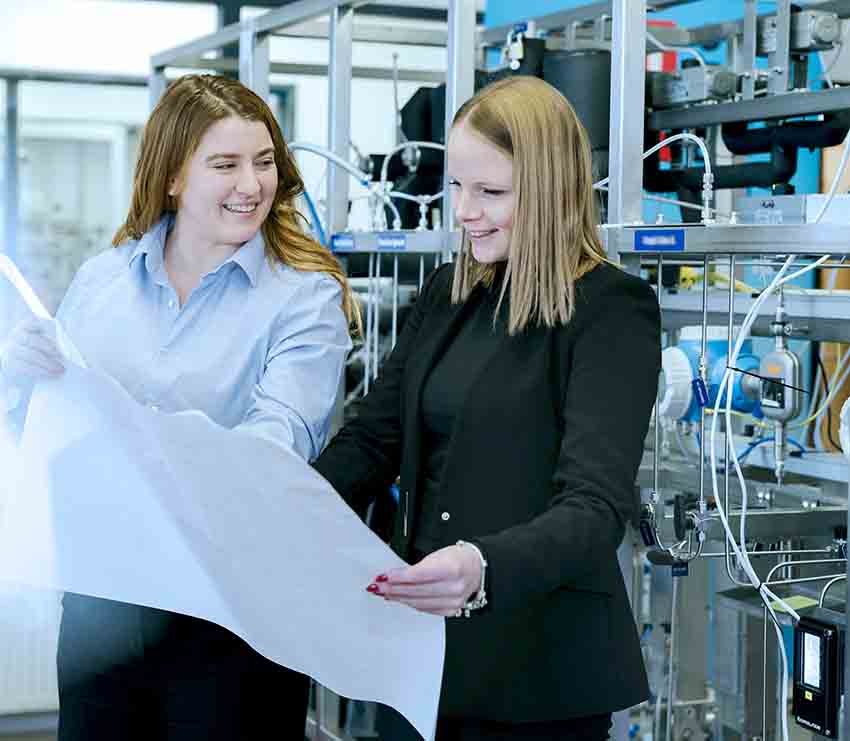
E.E: Tell us about sustainability in production & distribution.
D.K: Our continuous manufacturing approach follows the idea of process intensification. Yield improvement and the avoidance of unwanted side product formation, reducing the workup effort for the chemical synthesis, are core ideals we achieve, as well as a reduction in the number of unit operations.
E.E: Tell us about R&D and innovation.
D.K: We utilize continuous lab setups for development, which are tools for our chemists, as well as for our chemical engineers. The classic batch approach typically works serially. First, the chemist develops the process in flasks in the lab, followed by the scale-up of the process engineer. Our interactive approach between our chemists and chemical engineers, coupled with our continuous lab setups, leads to superior processes. Therefore, the continuous plant in the lab is the tool for the chemist, as well as for the chemical engineer.
E.E: What is the company strategy to reduce environmental impact?
D.K: During our process development, we are looking for processes with a high atom efficiency and opt for environmentally friendly solvents, or wherever possible even solvent-free processes.
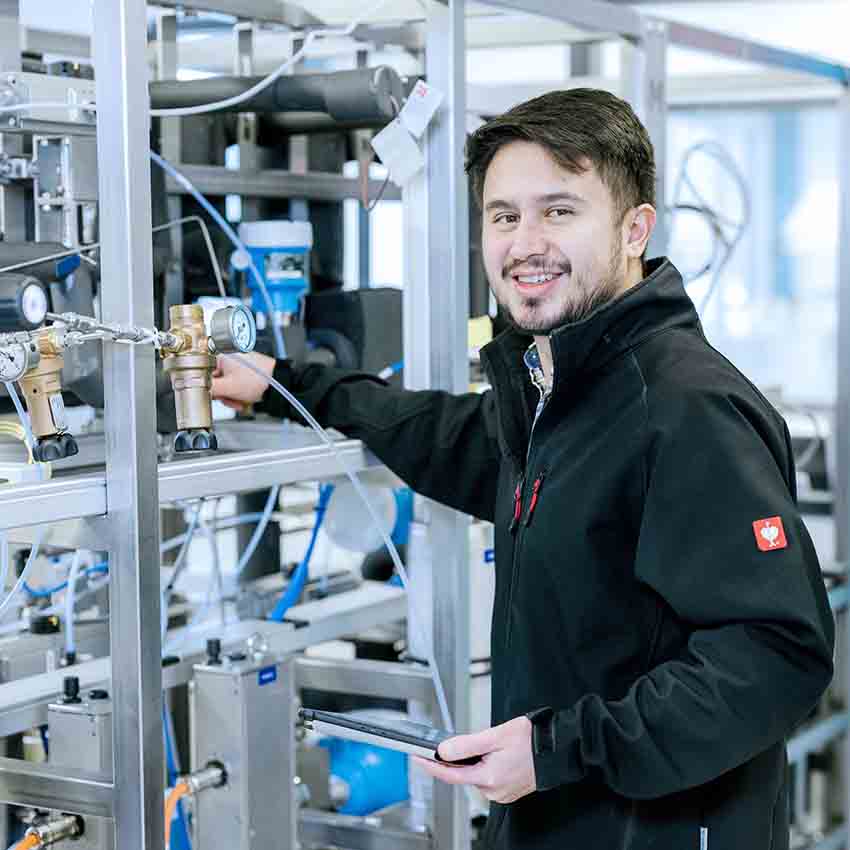
E.E: How do you drive focus on sustainability of operations?
D.K: Our skilled team uses a specific approach to identify critical process parameters for chemical processes. This is the basis to make sure that all molecules have the same processing conditions, which is not always the case in chemical batch processing.
E.E: Tell us about sustainable energy solutions used.
D.K: Continuous processes benefit from precise processing conditions, avoiding hot spots. Therefore, cryogenic processes, which usually entail high energy usage, can be executed at much higher temperature levels, lessening the need for extreme cooling. Exothermic chemical processes can be intensified by a more efficient heat transfer.
E.E: How do you see sustainability in the future?
D.K: It is expected that a significant number of chemical processes will switch to continuous manufacturing since higher qualities can be reached by cheaper and more efficient processes.