sensXPERT enables future-readiness for the plastics manufacturing industry.
Interview with Cornelia Beyer, Managing Director at sensXPERT.
Easy Engineering: How do you see sustainability and what are your efforts in this direction?
Cornelia Beyer: Across the globe, industries are facing increasing pressure to address their process contributions to the rapid advance of climate change, pollution, and global warming. To envision a greener future for the planet, it is vitally important for businesses to acknowledge the carbon footprint of their operations and waste production, as well as work with sustainable practices. Plastic manufacture is one such industry that has been particularly scrutinized for its impact on the world’s pollution problems. Producing a large carbon footprint through plastic waste incineration and endangering ecosystems with non-biodegradable material, plastics industries face a challenging battle to become environmentally sustainable and convince society of the ongoing efforts being taken. The steps to sustainability start within the plastics industry, minimizing potentially harmful processes and working towards a circular economy.
However, these challenges do not come without opportunity. Processors who invest in technology to make their manufacturing operations more sustainable will find it much easier to meet the taxonomy reporting requirements and ensure they keep their customers. In addition, they will also reduce their costs of goods and services (COGS) via decreased energy consumption, lowered material usage and scrap, improved quality, optimized human resources, shorter cycle times, and improved uptime. Overall equipment effectiveness (OEE) can also see an improvement, with lower wear on presses and molds, and improved production capacity (potentially delaying the need to make capital expenditures on new equipment). In the end, this can benefit everyone across the value chain.
The sensXPERT process control solution from NETZSCH Process Intelligence GmbH is a highly useful tool for plastics processors to improve their sustainable practices. It works alongside molding rigid plastics or elastomers, neat, unreinforced polymers or composites, and with thermoplastic, thermoset, or vitrimer matrices. The sensXPERT solution provides moment-by-moment in-mold materials characterization and process data to predict how evolving conditions inside and outside the mold are likely to affect the ultimate performance of parts.

sensXPERT Digital Mold achieves sustainable manufacturing through shorter cycle times, lower energy usage, and reduced scrap, while also providing the highest level of transparency necessary for meeting E.U. taxonomy reporting requirements. This is possible with the fully digital system presenting a complete digital thread (traceability) for every product produced using the system.
E.E: Tell us about the sustainable solutions that you offer.
C.B: sensXPERT is the game changer for the sustainable, resource-saving and data-driven plastics production of the future – and is aiming to pave the way for a sustainable and transparent circular plastic production.
While pressure and temperature sensors are widely used in the manufacturing landscape, they do not provide comprehensive information as they are not able to capture material behavior at molecular level. With sensXPERT Digital Mold dielectric sensors determine these crucial parameters, e.g. the degree of cure and glass transition temperature, which are decisive for the quality and thus resistance of the end product. Thus, quality control as part of the ongoing process is the new standard the industry is aiming for. The in-mold sensor data is processed using artificial intelligence based on 50 years of experience in basic materials science, reaction kinetic simulations and real manufacturing data.
Besides the immense measurement hardware know-how incorporated in the sensors and the edge device, the sensXPERT technology excels in its mathematical and physical/chemical models of material behavior and machine learning algorithms that constantly scan incoming data for patterns and deviations in the background. The algorithms translate the raw sensor data into predictive quality criteria, feeding them back to technicians, monitoring a given machine and process via a web app.
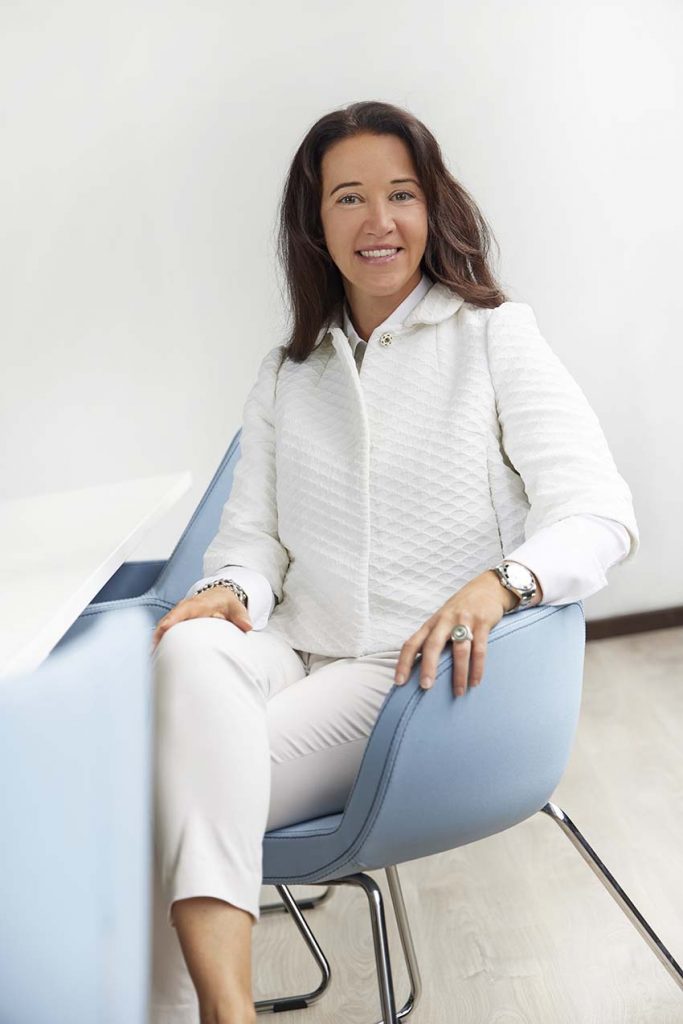
An additional layer of machine learning algorithms supports the system parsing the process parameters and sensor data flowing in from customer molds in manufacturing facilities worldwide, displaying the process outputs and operating conditions using data science. Over time, the amount of data created enables predictive analytics to kick in, thus promising unseen process stability. In more depth, algorithms note data set deviations; correspondence starts with the local edge device, which alerts the workers that monitor the process. The machine learning models running in the background experience consistent retraining when patterns change, ensuring the process’s performance.
E.E: What is the company strategy to reduce environmental impact?
C.B: With the start of the EU taxonomy in January 2023, companies’ access to finance is linked to sustainability criteria. This – and the overall public view on the use of plastics – puts increased pressure on plastics manufacturers to adapt their products and processes. The sensXPERT Digital Mold solution enables plastic manufacturers to design their processes optimized for sustainability.
Monitoring key quality markers in real-time allows scrap reduction of up to 50%. In order to ensure the production of the highest quality products, cycle times are often longer than needed as processors include a safety time. This additional machine runtime can be abolished, once sensXPERT Digital Mold is implemented. This in turn leads to energy savings of up to 23%. We are committed to providing the change for sustainable plastics production that is so desperately needed.
A significant issue is recycling and the clean separation of the materials. The challenge of the plastics industry is dealing with the enormous number of plastics in the market. Plastics can be reused by turning waste into recycled raw material. However, processing recycled materials has barriers. Often different plastic types are mixed together, making it challenging to reach high part quality without losing process efficiency as each batch of material is different. For this, adaptive manufacturing processes are required, which senXPERT Digital Mold enables.
Our R&D team is currently adapting our solution to allow process optimization for thermoplastics and thus, recycled materials. The first tests showed that our technology can also detect the key parameters in injection molding. This transforms the sensXPERT Digital Mold solution into a promising candidate to solve processing challenges in the production of recycled plastics.
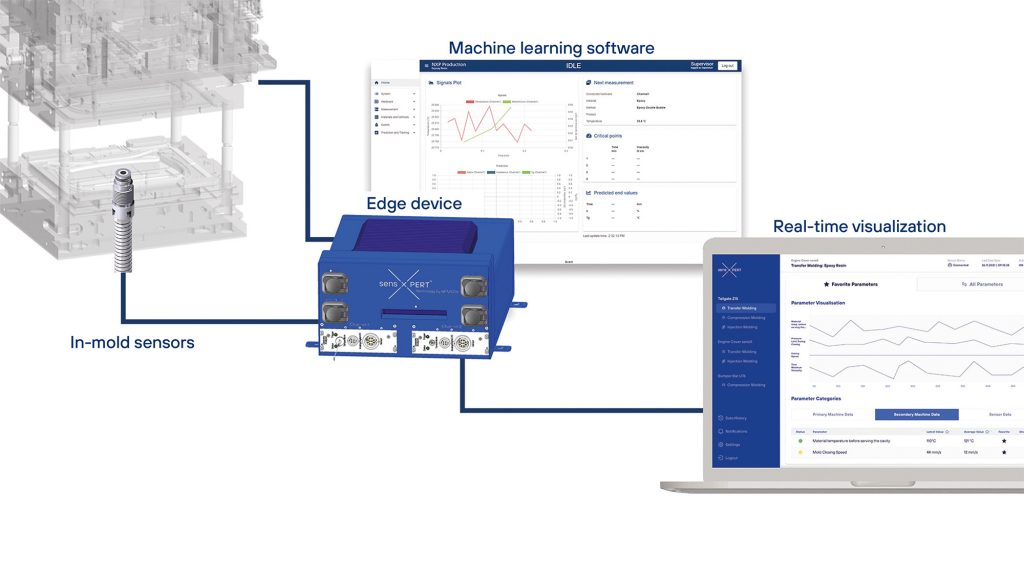
E.E: How do you see sustainability in the future?
C.B: It is no easy feat for the plastics industry to become a sustainable partner for the E.U. Green Deal, and its ambitious climate goals for 2050. It is, however, very possible for companies in the market of plastic manufacture, fabrication, and supply to begin to make a change. Implementation of systems such as the sensXPERT process control solution can better document the plastic industry’s use of CO2 in relation to a company’s carbon footprint, giving detailed analysis into the production cycle and where sustainable solutions can improve operations.
Investing in such technology will help towards E.U. goals of increasing the share of renewable energy to at least 32% by 2030 and becoming climate-neutral by 2050. The technology helps to identify problems in production before products reach the market, therefore helping businesses keep a detailed record of their processes and aligning the data with the Sustainable Finance report that’s needed for the plastics industry to meet E.U. taxonomy requirements.