From small to large-scale approach: fermentation on an industrial scale requires technical experience – and a lot of communication. This is how it works at German Biotech company BRAIN.
In contrast to spontaneous fermentations during home bread baking with sourdough, targeted fermentation processes in industry must be planned and developed in detail. As a basic process of biotechnological production, a targeted fermentation starts in a small laboratory set and is then scaled up to production scale.
At biotech company BRAIN in Zwingenberg targeted fermentation is carried out on a small scale in the laboratory, occasionally also on a somewhat larger pilot scale of up to 200 liters. Special technical equipment is required and, of course, a great deal of experience. For a further up-scale to a larger production-scale fermentation BRAIN Group member Biocatalysts Ltd, a British enzyme specialist, handles larger production-scale fermentations for BRAIN Group customers.
Fermentation process in bioeconomy
Specific Microorganisms that are used for fermentation, need nutrients and mostly air. Both is provided in the fermenter or bioreactor. From a technical view a fermenter is a clear thing: a closed vessel in which stirring takes place. The microorganisms (bacteria or funghi e.g.) use the supply of organic substances, nutrients and trace elements present in the liquid medium to produce the energy they need. Enzymes inside the cells convert the substrate, producing the energy molecule ATP. The organisms use this energy to reproduce and to produce metabolic molecules. Under certain conditions, which vary from organism to organism, the microorganisms also produce “valuable substances” from the substrates. These metabolic products (target molecules) either remain in the cell or are released into the medium and can be “harvested” by the bioprocess engineers at BRAIN.
The target molecules that industry is interested in are e.g. enzymes, proteins or small molecules. Customers use them in industrial processes and, in the case of enzymes, replace chemical reactions with biochemical reactions. They often do that in order to have their processes and/or products more environment-friendly and thus improve the company’s sustainability. So, fermentation can be seen as a key technology on the industry´s way to bioeconomy.

Microbioal production facilities
How to get a microorganism to produce a targeted valuable substance? The production is artificially induced in the fermenter, for example, by introducing genes into the microorganisms. The genes can be “switched on” e.g. by induction with a specific substance or by the lack of a nutrient.
Targeted fermentations require precise planning. Ideally, the best possible conditions for the organisms are provided in the fermenter: e.g. with regard to the type and concentration of the nutrients offered, the temperature, the pH value or the oxygen level. Basically, therefore, the first thing to do is to obtain as much information as possible regarding the growth behavior and requirements of the strain.
Then a decision about the kind of fermentation (batch or fed-batch) has to be made, followed by defining a “feeding strategy”. Other process conditions must also be defined, i.e. temperature, stirrer speed (and control), gassing rate and duration of the fermentation process.
Even though much of this information is described in scientific publications, especially for special cases or poorly described organisms, much of it must be determined in preliminary experiments. Thus, it may well take some time before the BRAIN experts go into the fermenter with a new strain for the first time. At BRAIN the bioengineers work with a wide variety of bacteria, such as Bacillus subtilis/licheniformis, Pseudomonas putida and Escherichia coli, but also with yeasts and fungi, such as Picha pastoris, Kluyveromyces lactis and Aspergillus niger. They also cultivate more exotic organisms, including Streptomyces, Aceotbacterium woodii and Rhizomucor mihei.
Challenging fermentation in an industrial scale
The most meaningful differences between lab-scale fermenters and large scale fermenters are the operations of mixing and oxygen supply. Small-scale fermenters offer much better mixing because it is possible to turn the stirrer very quickly, e.g. at 2,000 rotations per minute (rpm). On a large scale, the maximum of about 200 rpm is quickly reached. As a result, not only the mixing but also the introduction of oxygen into the medium decreases significantly. In addition, the size on an industrial scale means that cooling the bioreactor becomes more demanding and also more expensive.
Besides the large fermenters are usually stainless steel vessels, whereas glassware is often used in the laboratory. This results in different starting conditions for sterilization and cleaning. Large fermenters have to be sterilized with hot steam or chemically. Special programs can be used for cleaning, also to clean all pipes leading to and from the fermenter. Both kinds of fermenters are equipped with the same sensors, so that the same data can be collected.
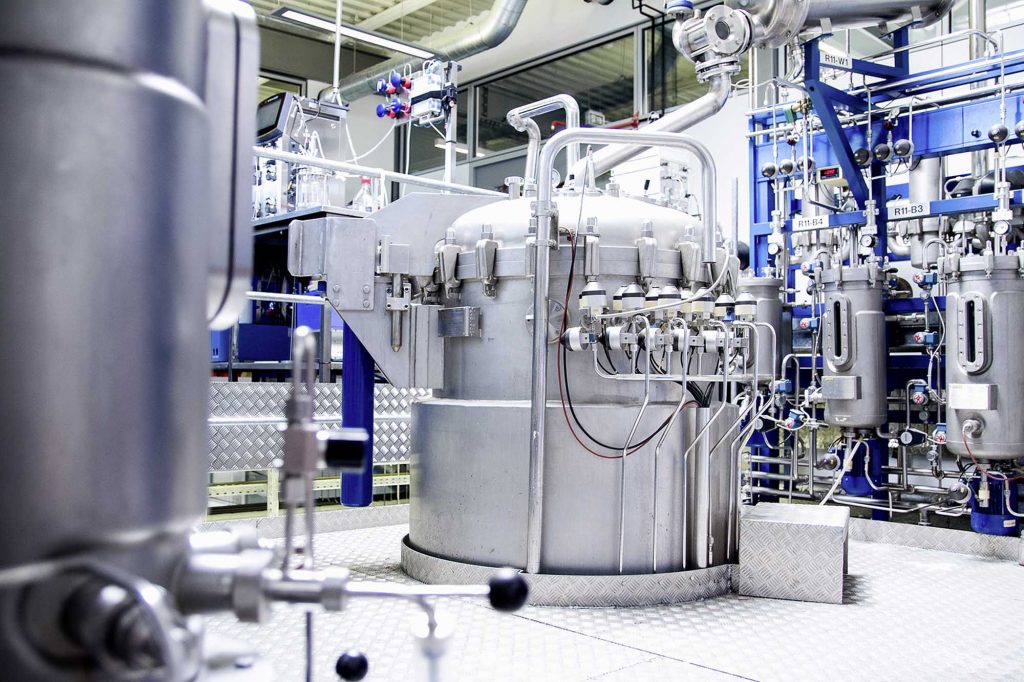
Tech transfer in the scale-up process
Starting with the developing and the establishing on a laboratory scale, i.e. with one to ten liters, the process is then transferred to the next size. At BRAIN´s technical center in Zwingenberg, a 200-liter reactor is then used. After that, the optimized process is well documented and transferred, for example, to BRAIN Group member Biocatalysts, where cultivation can be carried out on an even larger scale (500 – 8000 liters).
During such a tech transfer, the specialists from both companies are in constant exchange with each other. The task then is to apply the foreign conditions to Biocatalyst´s own process in the best possible way. Challenges arise when there are differences in the laboratory equipment – so for example both companies have to use the same filter membranes that they take for cell separation. Otherwise there may be different results in terms of yield. Further critical aspects are the methodology for preparing liquid media, or if Biocatalsysts (or another partner manufacturer) wants to dispense with a certain medium component, as it is known to have an influence on their own reactors.
Thus, during the tech transfer or scale-up, the process is defined more and more specifically to the manufacturer’s specifications until the first processes are run there on a large scale. A lot of fine-tuning has to be done within the transfer and the most important factor in all of this is communication. The whole thing can only work if people speak correctly and at the same level.
Authors:
Sebastian Hohlreiter, M.Sc.
Research Engineer
Dr. Christian Naumer
Vice President, Unit Head Bioprocess Development
BRAIN AG, Zwingenberg, Germany
business@brain-biotech.com