Founded in 1975 in Tomi-shi, Nagano, Japan, Mimaki is a leading manufacturer of wide-format inkjet printers and cutting plotters. The company supplies industrial printers, cutting plotters and their consumables to different segments, including the sign graphics, textile, industrial and 3D markets. Mimaki Europe itself was founded in 2004 to manage the EMEA region.
Since 1975, Mimaki has steadily grown by reputation and influence into a global company with large operational bases in Asia and the Pacific, United States and Europe. In addition, they work with a vast network of long-established resellers and partners worldwide.
Easy Engineering: Which are the fields of activity where you are operating?
MIMAKI: We serve various market segments and usually group them into four business units: Sign Graphics (SG), Industrial Products (IP), Textile and Apparel (TA) and 3D.
Our printers and cutting plotters for the sign graphics market are used for the creation of indoor and outdoor signs, retail displays, stickers and labels, among others.
Our portfolio for the industrial segment mainly consists of our UV flatbed printers that can print on almost any substrate, including plastic, wood, metal, glass, and more. These machines are used for printing a wide range of products, such as custom promotional merchandise, name badges, furniture, glass decorations, kitchen splashbacks, doors and more.
We also have a long heritage in textile printing. In this market, our textile print solutions are used to produce textile banners, interior fabrics, fashion apparel, sportswear, face masks, etc.

Our 3D printing technology was added to the Mimaki product portfolio more recently but feature the same level of advanced innovation that Mimaki is known for. We were the first to create a full-colour 3D printer that can offer 10 million colour possibilities, opening the door to new opportunities for highly creative and accurate 3D applications. Our 3D printers are used for producing scale models, figurines, product prototypes, and art.
It’s quite amazing how many things around us, in our everyday life, are actually printed and how often these high-quality prints are produced using Mimaki technology.
E.E: Which are the most significant projects from 2021?
MIMAKI: Università di Firenze (University of Florence) (mentioned below) and Biologic Models, who are using Mimaki’s 3D printing technology to produce intricate molecular visualization models, are great examples of how this technology can be used to create detailed high-quality 3D printed models for the medical sector.
In addition, Grand Style’s comprehensive industrial UV printing services see the company regularly embark on complex projects with the use of the creative design and a large number of production stages: cutting of materials, 3D milling, vacuum moulding, laser engraving, furniture production, printing, various light, and dynamic effects, all which give additional value to the end-product. The company is equipped with a Mimaki JFX200-2513 and a Mimaki JFX200-2513 EX.
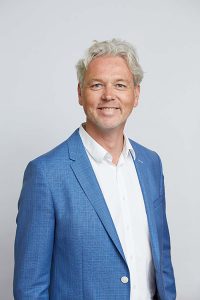
Mark Sollman, Product Manager EMEA at Mimaki Europe
E.E: What projects were the most challenging?
MIMAKI: There are 3D applications where colour is crucial to ensuring a true representation of what is being printed. Mimaki’s 3D technology, with 10 million colours achievable, provides the range of colour needed to accurately reproduce the most complex of models. Medical professionals, researchers or educational organisations using 3D printing to deliver anatomical models or even prosthetics that truly match skin tones, require exceptional colour fidelity. Such is true for Mimaki customer, Università di Firenze (University of Florence), who chose Mimaki’s technology to print models of the human heart and help students recognise its structure during a surgical or anatomical dissection.
E.E: What are the usual challenges you encounter?
MIMAKI: Other challenges business face when producing intricate, detailed scale models, figurines, collectables or product prototypes, is the time it takes to first produce the model and then to finish the model with hand painted colour and detail, which is also extremely time-consuming and expensive.
E.E: How did you overcome the challenges?
MIMAKI: Adding high-quality, full-colour 3D printing technology from Mimaki streamlines the model-making process and delivers a high-value model.

E.E: What products / solutions were used in the projects?
MIMAKI: Università di Firenze (University of Florence) used the Mimaki 3DUJ-553 3D Printer to produce its models of the human heart but Mimaki’s new, more compact 3D Printer, the 3DUJ-2207, has the same colour capabilities and could also be chosen for such a project.
E.E: Why did the clients choose your products / solutions?
MIMAKI: The main reason Università di Firenze (University of Florence) chose Mimaki was the quality and colour achievable with our technology. In fact, many of our customers, across all the sectors we operate in, would say that our solutions are chosen for the quality they are able to deliver when using them. The heart models featured good detail definition and dimensions, and excellent colour fidelity. Often customers like Università di Firenze (University of Florence) also choose Mimaki because of our far-reaching network of partners too, ensuring they can rely on expert, local support whenever they need it.
E.E: How were these products/solutions used to optimize the client’s business?
MIMAKI: According to the team at the University of Florence, 3D printing can effectively contribute to transforming the world of teaching and medical-scientific research. The colour quality, replicability, and durability of 3D printed objects could enable the team to cross further frontiers too. In pathological anatomy, for example, they are now able to create a 3D organ that shows the anomalies caused by a specific disease – thus providing a very useful tool for preparing any surgical intervention and for communicating with the patient.

E.E: What innovative features do the products / solutions have?
MIMAKI: With Mimaki’s complete and affordable full-colour 3D printing solution – comprising the Mimaki 3DUJ-2207, 3D Print prep Pro software and the 3DCS-322 post-processing unit – the end-to-end 3D printing process is now easier to implement and operate than ever before, making the dream of adding full colour 3D printing now a reality. The larger print area and higher speed of the Mimaki 3DUJ-553 also offers the same extensive colour range for high-quality model-making on a production scale.
Full-colour professional 3D printing can enable a wealth of new ground-breaking revenue opportunities or simply add significant value to an existing business that currently 3D prints in one colour.
When we look at our UV printing portfolio, the quality, speed and versatility of these solutions is market-leading. The JFX600-2513 LED-UV large-format flatbed inkjet printer, for example, is designed to address the high-volume UV market. Engineered for high speeds and high productivity, this new model offers print service providers a broader variety of applications thanks to a wider range of ink types and increased media flexibility.
The UJF-7151 plusII and the UJF-MkII e Series was developed for seamless and reliable high-speed production. The UJF-7151 plusII allows for faster print speeds of up to 190% compared to the previous UJF-7151 plus model. The printer is capable of handling high-quality print jigs and ideal for accurate industrial printing of heavy media, such as wood, metal, and glass.

E.E: What are your forecasts for 2022?
MIMAKI: While the economic and logistical situation surrounding the pandemic continues to be unpredictable, we have high hopes for the coming year. Mimaki will continue to support all of the core markets in 2022 and beyond, and we expect to see particular growth in the UV market. We also expect to see further adoption of our 3D printing technology, due to our new end-to-end solution, the 3DUJ-2207 full-colour 3D printer combined with 3D Print prep Pro software and 3DCS-322 post-processing unit, being both cost-effective and high-quality, opening the market up to more model-making businesses.
Another trend we anticipate through 2022 is a higher demand for automation, an exciting prospect as it allows for Mimaki printers to work alongside other technologies in automated production workflows. As events begin to migrate from virtual to in person, this year we attended FESPA and Formnext and we look forward to even more tradeshows returning to our calendar in 2022. We have enjoyed developing our digital showroom and will continue to do similar virtual initiatives in the new year, but we can’t wait to demonstrate our newest, innovative technologies at more in person events.