Established in 1899, today a Fayat Group Company, Marini is a world leader in the manufacturing of stationary and mobile batch asphalt plants with manufacturing sites in Italy, Turkey, China, India, and offices in Russia and UAE and a global partner network. With a capacity of up to 480 t/h, relying on the most modern technologies and over 120 years of experience made in Italy, Marini’s equipment distinctive features allow customers around the world to produce low energy consumption asphalt using up to 100% of recycled asphalt pavement (RAP). Unique project management capabilities combined with outstanding technical support, service availability, a global footprint and a dedicated training Academy make of Marini the customer’s choice when it comes to reliability, innovative technology and comprehensive effective support.
For more information about Marini, please visit https://marini.fayat.com.
Easy Engineering: Which are the most futuristic products / solutions from your portfolio?
MARINI: The use of reclaimed asphalt pavement (RAP) is the most important market trend that is developing steadily, though there are large differences between different markets and working practices between each contractors.
MARINI offers all the options available:
- Recycling ring on the dryer drum, with the possibility to use up to 40% RAP;
- RAP placed directly into the mixer, possible up to 40%;
- Smart combination of both solutions, up to 60% RAP;
- MASTER TOWER technology for any % up to 100% RAP.
The mature countries with a big network of high roads are the best candidates for greater adoption of RAP. The most important factor is to preserve the quality of the residual bitumen contained into the RAP used, choosing the right and proper technology.
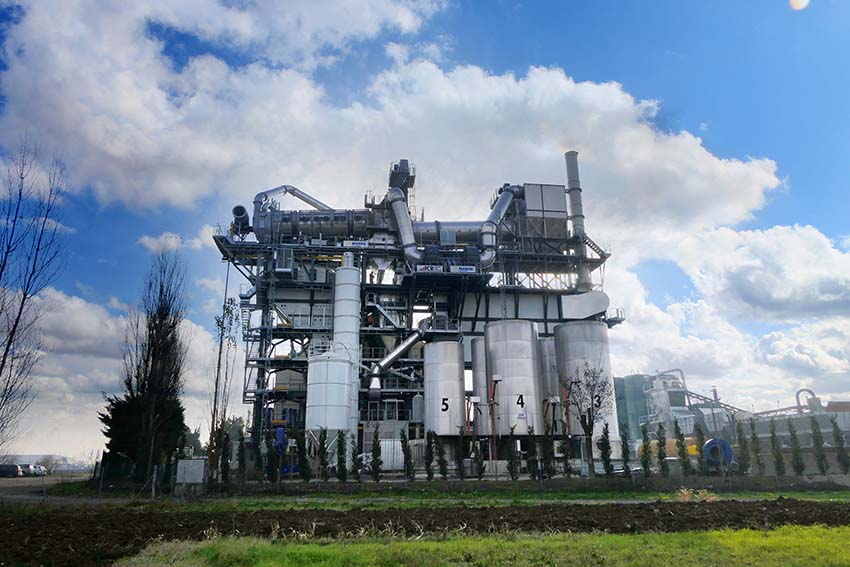
E.E: What are the characteristics of these products / solutions?
MARINI: Let’s focus on the MARINI MASTER TOWER technology which today is the most performing available on the market.
As a result of its peculiar feature of vertical integration into a single plant solution, including mixing tower, 2 dryers, filter on ground right under the tower, recovered fines deposit and much more, all problems of plant limitation and site layout can be solved, while easy grafting can be made onto any given site, even one already existing.
The new MARINI MASTER TOWER is a milestone in asphalt production with a high RAP content, in addition to the guarantee of low emissions and low energy consumption.
As we said during product lunch and presentation at BAUMA 2019, all the technologies available on the market up to now are based on a system having two dryer drums, each with its own burner. It is needless to say that such a system is “energivorous”, because of its “double” use of fuel for the two burners, and the consequent elevated power consumption.
These systems exceed the present international limits set for atmospheric emissions.
MARINI completely innovative solution consists of the simplification of the mechanical components of the drying and heating systems of the materials. While maintaining the two dryer drums, our system uses a SINGLE burner which is able to supply energy both to the first drum, dedicated to virgin materials, and the second drum, in the right amount depending on the percentage of RAP to be heated.
The maximization of the burner calories is realized through the recirculation of hot combustion gases, right down to the last calorie. In particular, the RAP is heated by the hot gases coming from the virgin aggregate drum. The use of the hot gases only avoids contact of the RAP with the direct flame and its radiation, thus eliminating peaks of high temperature during the RAP heating process.
On discharge from its individual drum, the hot RAP can be heated up to a temperature of 160°C, allowing recipes containing up to 100% RAP to be produced, ready to be laid as pavement; in addition the advantage that the virgin materials have not had to be overheated.

E.E: What are the benefits for the users?
MARINI: The main measurable benefits are:
- Low emissions, as a result of indirect of RAP with hot air;
- Reburning;
- Gas;
- Smell emissions treatment.
New standard for RAP (Reclaimed Asphalt Pavement), as a result of new smart software control system, high flexibility to variate recipes and recycled percentage in the HMA up to 100%, long lasting manufacturing infrastructure
High energy saving as a result of one burner instead of two in counterflow, high efficiency in the heat exchange and up to +20% saving on thermal and electric energy consumption ( the lowest CO2 emission level for asphalt plants )
E.E: How do you think the future will look like in your field in the following years?
MARINI: In every state of the European Union and around the world, new road infrastructure design criteria are becoming increasingly popular. The systematic and homogeneous application of the same road design criteria makes it possible to spread the same technologies for the protection of the environment on a large scale as well as products that meet these criteria.
All this is triggering a virtuous circle, inducing those who are less virtuous to adapt to the new demands of public administration in the countries as well as public and private companies.
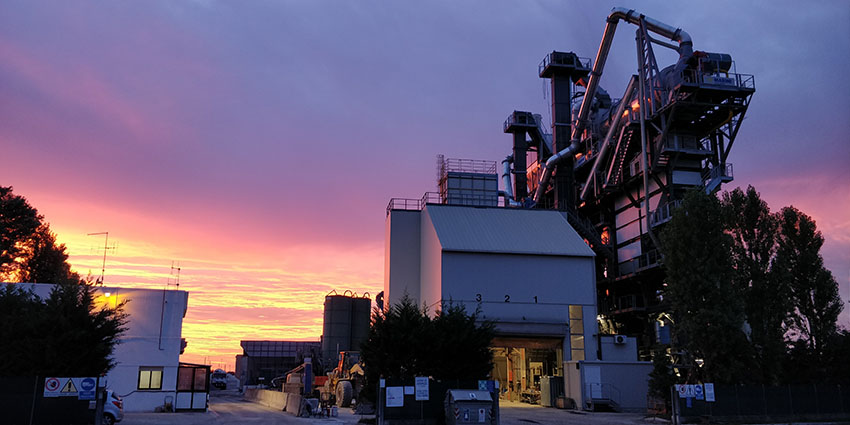
E.E: What technologies do you think will grow this year / in the following years?
MARINI: Sustainable road design is essential and goes hand in hand with constant technological innovation.
The successful technologies will comply to the following requirements:
- Reduction in the consumption of raw materials during production phase because existing materials can be recovered on site;
- Reduction of energy consumption because better and more efficient machines are used;
- Containment and reduction of emissions because compliance with the rules is imposed and it is clearly defined how compliance with the standard must be measured and who’s in charge of controlling;
- Reuse, recycling and regeneration of materials during production processes;
- Extension of the useful life of products by encouraging an effective and far-sighted policy of conservation and maintenance of civil and industrial infrastructures.
Asphalt plants play force become part of this virtuous circle, in fact those available on the market can be equipped with special technologies to allow the use of RAP (Reclaimed Asphalt Pavement) at variable percentages based on specific customer requirements.
The solutions available today boast many positive aspects.

Here are the advantages of a correct choice:
- Reduction of energy consumption for the mix production;
- Possibility of using up to 100% recycled material, therefore containing bitumen;
- Lowering of polluting emissions and containment of odorous.
If all this is instrumental in favouring the eco-sustainability of all our actions in the area of road paving, it is nevertheless very important, according to specific needs, to evaluate the most suitable technical solution, otherwise certain operational limits will inevitably arise.