The division of PEKA BAU 2000 Construction Ltd, which includes Pallethouse Kft. of Hungary, specialises, among other things, in the production of EUR pallets of wood. It has turnkey technology supplied by Störi Mantel, s.r.o. As a result, it launched a new Europalet technology in May this year. The technology consists mainly of a high-capacity jackhammer line from Störi Mantel, located in new production premises with patented technology to collect pallets using an electromechanical system.
The reason for the purchase of the pallet line was the objective to produce and meet the demand of pallets primarily for own use and also to offer possible overproduction in an ever-growing market that demands new pallets. ‘Thanks to the new production line from Störi Mantel, productivity and production capacity are at a level to fully meet the in-house pallet needs.’ The experience of the annual operation is viewed positively by the manager of György Petö and adds that the Störi Mantel brand has an important role in terms of automation, which has a high reputation in the world in terms of quality and is perceived as such by our customers. „The argument that we produce pallets on Störi Mantel machines carries a lot of weight with our customers “.
The priority of the production line is first and foremost operator safety, low energy requirements and production accuracy, both nail shapes and the final palette.
Pallethouse Kft. has implemented its capacity expansion project in Szikszó. The newly created pallet factory was implemented with support from the Hungarian state and the European Union for approximately HUF 490 million under the Operational Programme Economic Development and Innovation. The purpose of Pallethouse Kft.‘s development was to invest in greenfields and create a new industrial unit that meets the following requirements: high automation, flexibility for product innovation, being a market leader in quality.
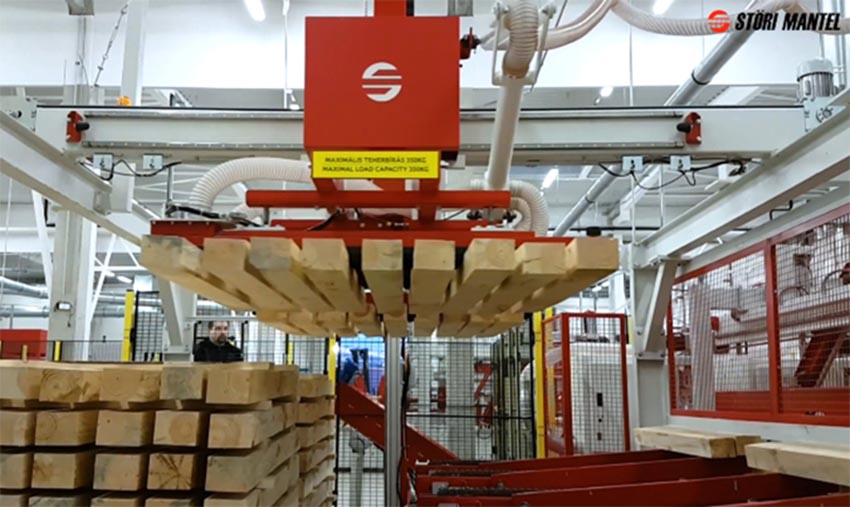
The purchased pallet production line is fully automatic, with output reaching 2000 pallets per shift, which also enables more cost-effective production. With the revival of domestic industrial production, Pallethouse allows Kft. to meet the increased demand in the market through a realized investment.
Preparing material
Pallethouse Kft. processes its own sawn wood as part of the pallet program, which is already prepared for the required input dimensions from the primary production line for the processing of logs. The material is delivered to the pallet line using forklifts to facilitate handling. The whole layer, depending on the product range, has to be inserted into the shortening centre, this is done with a vacuum manipulator.
From the toy, stored next to the production line, the vacuum manipulator loads onto the input chain conveyor. The human factor is not needed here. The operator just transports a pot of sawn wood to the designated place, the dosage is taken care of automatically by the line. The entry point for the material is divided into two sides for side and center cubes according to dimensions. The material is placed on the transverse chain conveyor intact into the shortening center for the production of cubes.
It takes away the hard work of cutting dice and handling the material. The forklift operator conveniently ties the prisms to the cut from one part and the other of the vacuum loader, which both increases productivity and also reduces operating costs. The capacity of the line is thus supplied with enough material, so-called cubes.
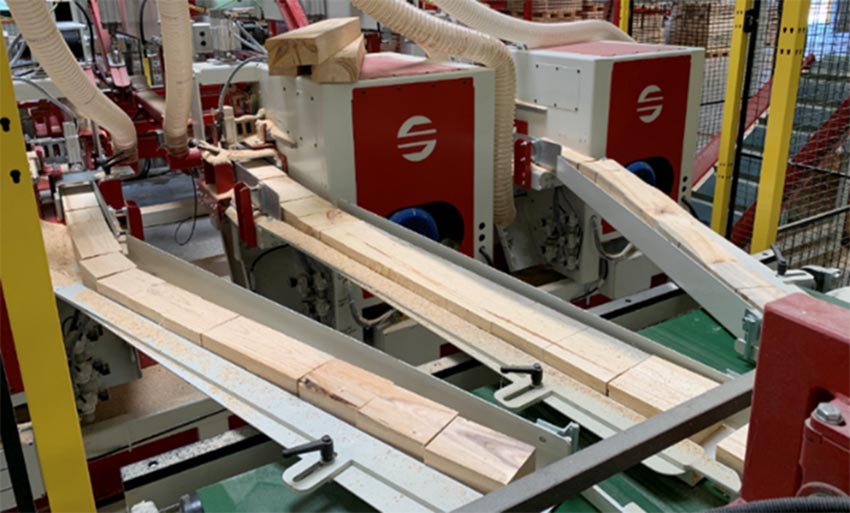
The high-capacity SMHC- Line consists of the following modules:
- Vacuum manipulator
- Cube cutting centre
- Cap jacking machine
- Pallet [top] jacking machine
- Pallet [bottom] jacking machine
- Working line: corner trimming, character
- burning, edge milling
- Pallet stacker
- Output chain conveyor
Pallet production
Most current pallet manufacturers do not only produce one type of pallet, but their range is far wider. Moreover, market demand is constantly changing, forcing manufacturers to respond flexibly. The delivered line meets the requirement for universality and allows to produce pallets of different types and dimensions and this puts this technology on an economically interesting plane. The full line in full kit is made up of three modules allowing efficient production of pallets with minimal human factor for operation. The universality of the line is enhanced by the assembly of the line from three jacking machines producing individual parts of the pallet.

Production line
In the case of the Deck Machine (SMPA-3), the input machine is equipped with transverse plate stacks that can be of two different widths as standard (e.g. EUR pallets). The principle of charging is provided by an electromechanical system, which is the standard for all manufactured machines of the Störi Mantel brand and the system is valued for its reliability and low energy requirements. At the output of the machine, the machine is accompanied by a stacker lid with an exit conveyor to balance the stacks for further operation.
The SMPA-1 loading machine with a handler is fitted with a conveyor with a cube stacker and a lid loading handler. The role of the machine in the large-capacity line is to nail the lid to the cubes, which are distributed from the shortening centre using the continuous conveyor of the jackhammer.
The next step is to distribute the pallet semi to the next operation to the SMPA-2 jacking machine, where the bottom plates of the pallet are automatically placed on the bottom of the palette. After finishing the operation to nail the bottom plates, the pallet goes to the last part of the line, the so-called working line, where the pallet has corners trimmed, longitudinal edges milled and characters burned and stacked.
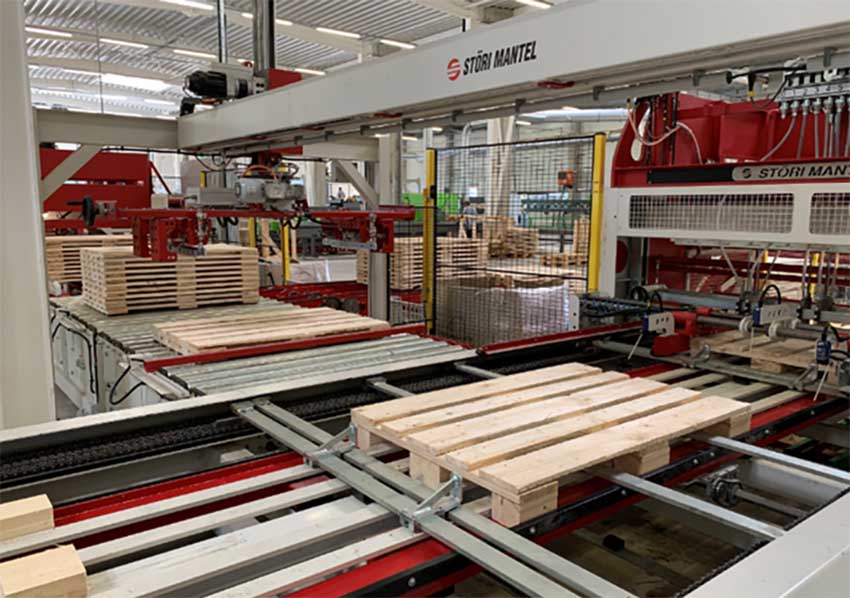
Description of the large capacity production line:
1) VAKU MANIPULATOR is used to load prisms onto the cross-input chain conveyors of short saws. The loading process operates in automatic mode and the loader operates three cutting saws. As specified, it transfers a layer of prisms from individual handrails to saw conveyors and automatically summarizes the stabilizing interlaces.
2) CARRIER PILS are used to cut the cubes. In the case of different widths of cubes on the manufactured pallet, each of the saws cuts one dimension of the cubes. The process of loading prisms from the cross-chain carriers into the saws operates in automatic mode and the operator only sets the necessary length of the cube. On the output of the short saws, the front and rear clippings and the remains of the cubes are separated with less than the required degree. The cutting saws operate within a length tolerance of ± 1 mm. min./max. length of input prisms 2 500-4 200 mm. min./max. width of prisms 60-145 mm. Min./max. height of prisms 60-100 mm.
3) THE UNITING EXEMPTIONAL TRANSPORT is designed to distribute cubes from individual cutting saws to the shift conveyor. The shortening saw that supplies the middle channel of the shift conveyor is equipped with a fixed conveyor channel. Extreme cutting saws supply the outer channels of the gear conveyor…
A full description can be found at: www.stoerimantel.com

Patented
The patented technology is clearly visible on the jacking machine. With two linear actuators, it highlights a modern and attractive design. Thanks to a specially developed solution, the pallet jacking machine is more efficient with the lowest power to the jacking machine in its class and only (1.2 kW/h).
The advantages of this patented solution are clear. You don‘t have to worry about leaked oil like on machines that use hydraulic system nails and subsequent ecological disposal. For hydraulics, frequent checks of the oil pressures, tightness and temperature are required, with hydraulic oil replacement usually required every year.
The hydraulic system is noisy, non-organic and energyintensive because when switched on, the hydraulic aggregate engines are still running at up to 9kW per jacking machine. This eliminates the demanding maintenance and frequent replacement of the oil filling.
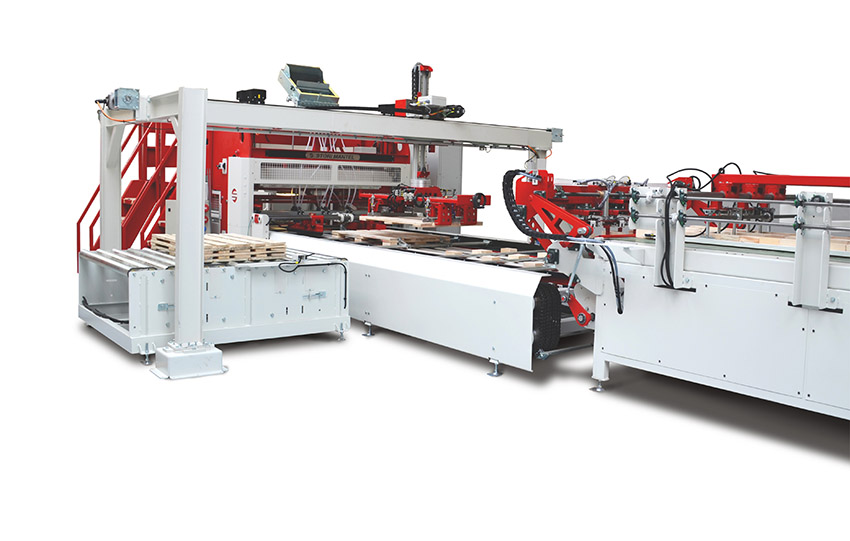
STÖRI MANTEL s.r.o.
U Trati 2620 (Průmyslový areál Tesla)
756 61 Rožnov pod Radhoštěm
Česká republika
Tel.: +420 607 104 014
E-mail: j.zacal@stoerimantel.com