Since 1923 TRAMAG has been developing and manufacturing customized low-voltage (LV) transformers and chokes for a wide range of industrial applications. Over the last years TRAMAG has developed into a widely recognized, well established and leading solution-specialist for LV transformers and chokes to markets worldwide, providing more value to the customers applications.
The TRAMAG group consists of two companies: The TRAMAG Trans-formatorenfabrik in Fürth, Germany, where engineering, the order center and the sales department are located as well as the production plant for the project business of high performance and technologically complex products. All other products, especially the serial business, is being manufactured at BOHEMIA-Trafo, a TRAMAG company in the Czech Republic.
Interview with Jan Reinecke, Business Director at TRAMAG.
Easy Engineering: What are the main areas of activity of the TRAMAG-company?
Jan Reinecke: Drives & Automation Technology, e.g. sinewave filters eliminating voltage peaks and providing a sinusoidal curve to protect the motor;
Machinery and Plant Construction, e.g. high power, low voltage transformers for the heating process in copper wire production;
Medical Technology, e.g. special transformers in medical devices with a multiple secondary system for numerous output voltages;
Renewable Energy Generation, e.g. noise-reduced LCL filter-chokes to convert solar-generated energy into grid-compatible current;
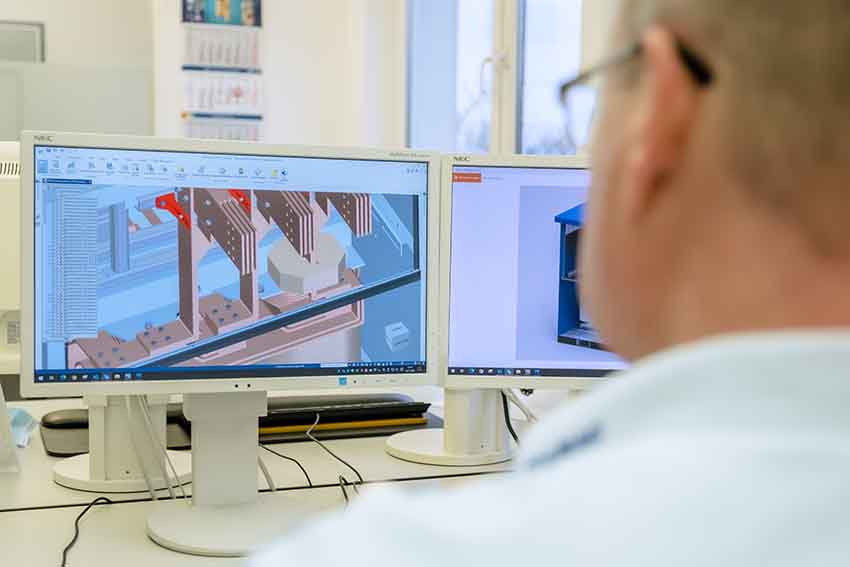
Test Facilities and Test Systems, e.g. load chokes in inverter test benches for the e-Automotive industry;
Energy Supply Systems, e.g. regulating transformers in an active filter-system providing a consistent voltage quality;
Shipbuilding, e.g. premagnetizing transformers charging MV transformers for the onboard power supply.
E.E: What’s the news about new TRAMAG-products?
J.R: Focus on e-Automotive industry: A large number of electrotechnical components are installed in an electric car. The prototype development in the laboratory, but also the series installation along the production line, places new and extended demands on test technology and test systems. These e-car components, like an inverter, are elementary components of the power supply but also of the drive train and must therefore be subjected to extensive quality tests with regard to functionality, load capacity and lifetime.
The core task in the functional test of the inverter is to simulate the system components of the energy supply, i.e. primarily the rechargeable battery, and the consumer, i.e. the electric motor, as a load and to make this load available for the functional test of the inverter. In these automatically operated inverter test benches, load reactors from TRAMAG take on the task of a substitute motor load and thus help to ensure that the tested electric cars, and thus electro-mobility, gets rolling reliably.
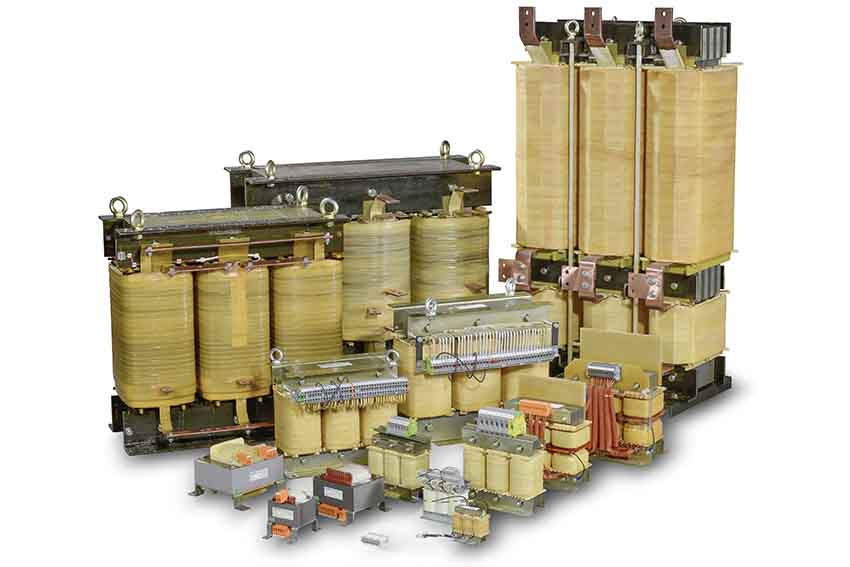
E.E: What are the ranges of TRAMAG-products?
J.R: Transformers: Low Voltage, dry type, from 100VA up to 1,5 MVA core power;
Chokes and Filters: Current up to 10.000A, operating secondary voltage up to 7,2 kV.
All products are compliant with the electrical standard EN 61558 and with the safety standards IEC/VDE and optional UL/CSA.
Products for use in medical applications are compliant with the specific electrical standard EN 60601 for medically used devices and equip-ment or according to EN 61558-2-15 for medically used rooms.
All products are generally designed for air-cooling (AN, AF), however, on request also be possible to be designed for a water-cooling (WF) concept.
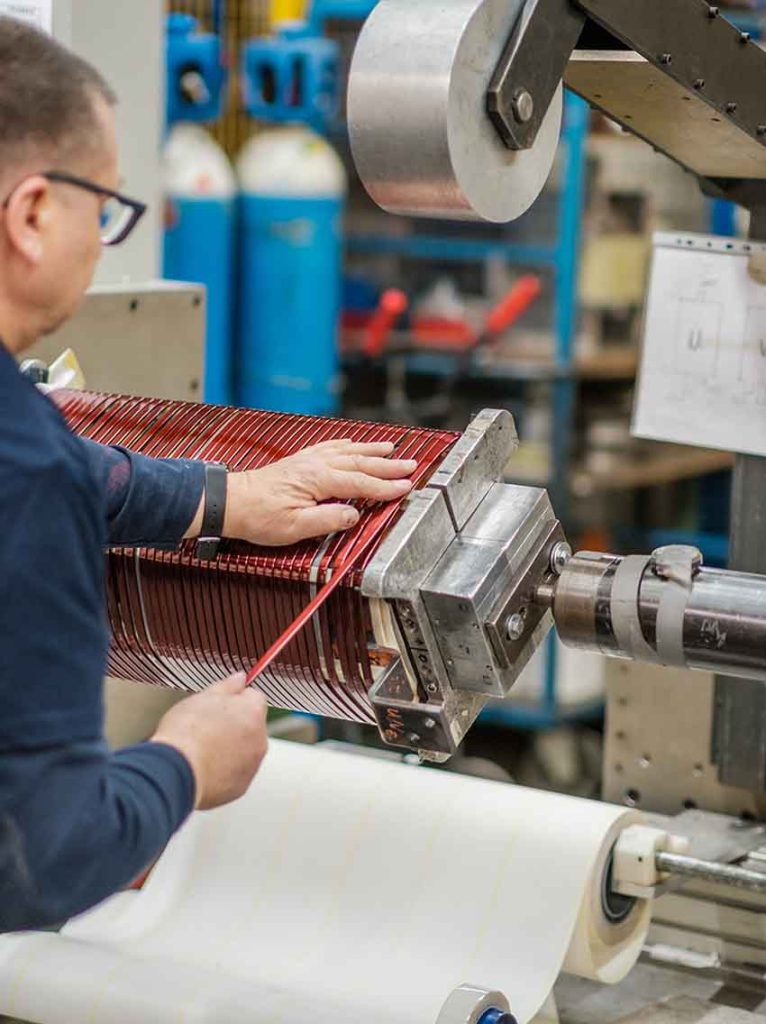
E.E: At what stage is the market where TRAMAG is currently active?
J.R: The markets of LV transformers and chokes are very diverse depending on the type of industry and application. For example, the market for smaller control transformers has been constantly shrinking over the last ten to fifteen years due to electronic substitutes. On the other hand, the market for line and power chokes has been growing due to the rising number of frequency-converter controlled drives systems accompanied by increasing demands on power quality. Another example for fast growing market is the e-Automotive sector, where TRAMAG benefits with it’s new product load choke as explained above under #3.
E.E: What can you tell us about TRAMAG relevant market trends?
J.R: The constant technological development of our customers’ products and systems regularly results in new and higher requirements for our trans-formers, chokes and filters. There is a particular demand for weight-reduced and more compact products, as well as specially developed and designed transformers and chokes for highly specialized innovative applications. Also, noise-reduced transformers and chokes are gaining more and more importance. In addition, we see an increasing demand for higher frequencies, low-loss-products and “plug-and-play” transformers with attached switching elements that protect the circuit as well as trans-formers and chokes with built-in sensors for thermal monitoring. Last not least more and more customers are asking for transformers and chokes that are supplied already assembled in a control cabinet, which is then fitted with switches and control components by the customer.
Thanks to the decades of experience and expertise of our engineers, as well as with our modern testing and inspection facilities, TRAMAG is always able to optimally combine the optimum winding material with the optimum core material for the technically and economically optimized, reliable use in the application.
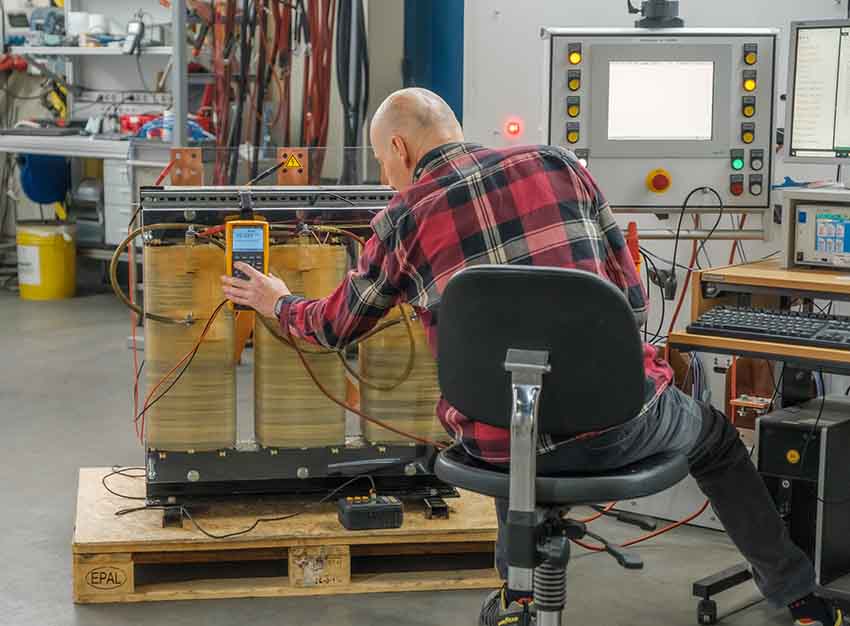
E.E: What are the most innovative products marketed by TRAMAG?
J.R: In general, TRAMAG innovations follow the innovations of our customer’s applications. For example, a modern, high-resolution MRI machine requires specially developed transformers that are able to meet the requirements for electrical supply and safety in all respects.
Special focus on Renewables:
Green electricity from photovoltaic technology is unsuitable in its original signal quality for feeding into the grid and would lead to disturbances and damage in the supply network. For this reason, solar power producers must observe binding standards and regulations for compliance with quality requirements for power feed-in.
In order to comply with the standardized, low-frequency compatibility level (THDi) according to these regulations, a TRAMAG-LCL filter – a combination of double-deck choke and capacitors – reduces the occurring amplitudes of the harmonics with its low-pass effect and the inductance connected upstream on the grid side and thus ensures a permissible and grid-compatible power feed into the supply grid.
The particularly compact design and the special mechanical bracing of the TRAMAG LCL filter also ensure reduced noise emissions during operation. These are several good arguments in favor of TRAMAG’s choke and filter technology, which has been tried and tested in a number of solar energy systems installed worldwide.
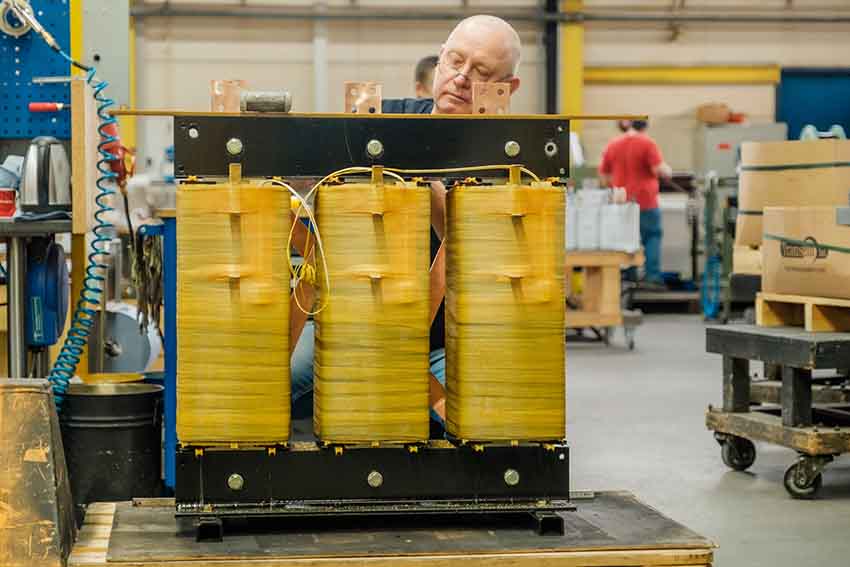
E.E: What estimations do you have for the upcoming months?
J.R: Our expectation for the near future is a further growing transformer and choke business driven by the increasing demand in specifically growing industries like e-Automotive, renewable energy generation and drives systems due the construction of new highly automated and digitalized factories.
Text and photos ©: All rights reserved by TRAMAG Transformatorenfabrik GmbH & Co. KG