Electrical equipment, such as switches, connectors, and motor brushes, can create electric arcs or sparks internally. Additionally, prolonged usage of electronic devices like iPhones generates heat, potentially turning them into ignition sources in hazardous environments.
To prevent this, hazardous area manufacturers employ various methods, with intrinsic safety being a crucial one. Intrinsic safety, or Ex ‘i’, is a technical concept that involves limiting the electrical and thermal energy to a level that cannot ignite an explosive atmosphere.
This is achieved through design considerations like controlling component temperature using resistors and fuses, minimizing internal sparking by limiting energy, and ensuring proper spacing and isolation of components.
Intrinsically Safe Equipment in the Industry
In industrial settings, the presence of flammable gases or vapors creates an explosive environment. Standard PCBs (Printed Circuit Boards) and other parts of electrical devices can ignite these gases or vapors, leading to explosions.
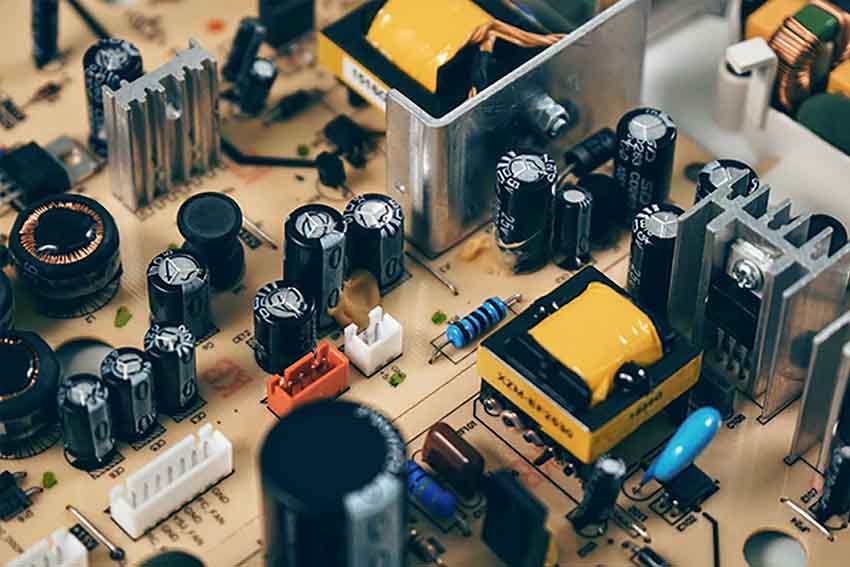
Comparing intrinsic safety to flameproof methods highlights different approaches to preventing explosions. Flameproof equipment, often termed ‘explosion proof’, is designed to contain explosions within its structure, while intrinsic safety prevents the creation of sparks or sufficient heat to cause ignition.
Protection Method: ‘Flameproof’
The pros and cons of flameproof equipment include a simple design suitable for high-power equipment, but it is heavy and expensive with complex maintenance requirements. The enclosure cannot be opened while the device is powered on.
In contrast, intrinsically safe equipment is cost-effective, doesn’t require special cabling, and maintenance can be done without shutting down power. However, it is suitable only for low-power devices, and redesigning PCBs can be costly.
Intrinsically Safe Devices
Various intrinsically safe devices are available, such as smartphones and cameras. However, using these devices alone isn’t enough to mitigate all risks in industrial locations. Proper operation and maintenance according to the user manual are crucial.
The intrinsic safety barrier is another key element in hazardous area design, limiting the energy transferred from safe to hazardous areas. There are two types: isolated barriers, which provide galvanic isolation and manage signals, and Zener barriers, which prevent high energy transmission.
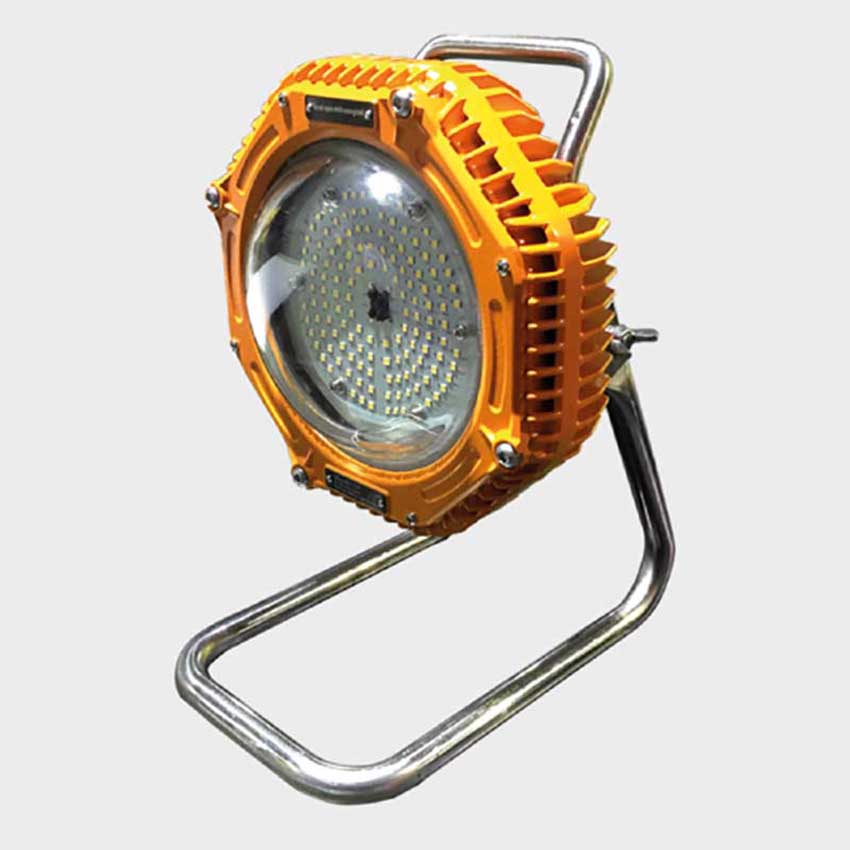
ATEX and Intrinsic Safety
Understanding the relationship between intrinsic safety and the ATEX directive is essential. The ATEX directive mandates safety standards for managing explosive atmospheres, with intrinsic safety being a key method for designing ATEX equipment.
The terms ‘intrinsically safe’, ‘explosion proof’, ‘flameproof’, and ‘Ex certified’ are often used interchangeably in the industry, causing confusion. While they refer to products suitable for explosive atmospheres, their specific meanings and applications may vary.
What Zone is Intrinsically Safe?
The term ‘intrinsically safe’ also categorizes equipment based on hazardous area zones, typically used in more dangerous zones like Zone 1 (gas) and 21 (dust). Understanding this categorization is important to ensure that the equipment certification matches the specific requirements of your location.
The Bottom Line
In conclusion, the concept of intrinsic safety is crucial for preventing ignition in hazardous environments. It’s important to understand that ‘intrinsically safe’ often refers to products suitable for more hazardous zones and should not be confused with terms like ‘explosion-proof’ or ‘flame-proof’. Always ensure equipment certification matches the specific requirements of your location.
For the full explainer on intrinsic safety, visit the Cobic-Ex Blog.