Founded in 1929, Viappiani Printing is one of the world’s leading IML printers. They serve a solid Italian and international customer base from their works in Milano, Italy, and they are since 2009 members of the CTI Group, a privately owned group of companies printing packaging all over the world. Production of exclusively IML labels and more than 35 years of experience are a good guarantee for the customers. The IML Label production ranges from labels for food containers to chemicals and to special applications.
Interview with Stefano Di Gregorio, Technical & Business Development Manger at Viappiani Printing.
Easy Engineering: After-sales reliability. What services do you offer?
Stefano Di Gregorio: Our after sales support is for sure one of our strengths.
It is our mission to accompany our customer in all the phases of the business relationship.
Let’s start from the very beginning and let’s talk also about pre-sales as this is part of the same flow. At Viappiani we love to be involved already in the early planning steps of a project. In fact, it happens that we sit around the same table with injection moulder, mouldmaker and brand owner’s Marketing and Product Management people to sculpture the next day’s product. Involving us in the planning phase allows to add a printer’s perspective with all the connected aspects. Just to make a clear example, some years ago we won a project of a pail on which unfortunately we have not been involved in the planning phase. At project start we noticed that by reducing the label height by 4 mm we could increase the hourly productivity of the IML label printing by 50%. With the slightly smaller size, the label was in fact fitting three positions per sheet instead of two. As you might understand the saving was enormous. Unfortunately a lot of things like label magazines, automation dummy core, design files, and so on were already done. All this had to be reworked, and this is a pity because looking into it from the very beginning could have saved quite a bit of time and money.
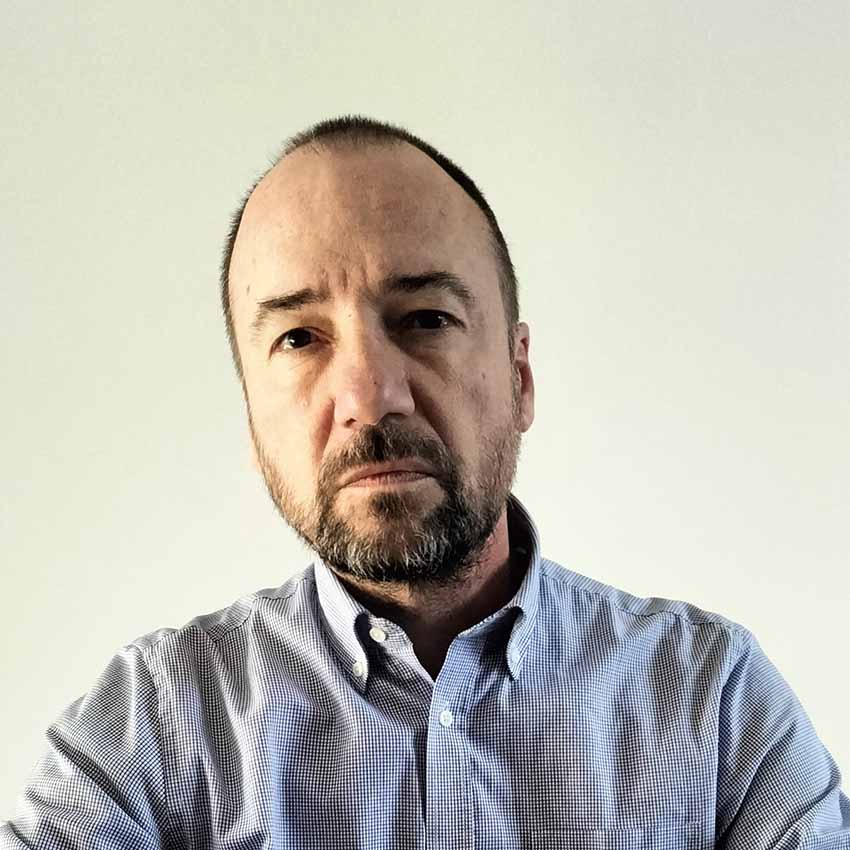
Stefano Di Gregorio, Technical & Business Development Manger at Viappiani Printing.
With more than 33 years of experience in IML applications we honestly feel we can offer our point of view also regarding other aspects which are not necessarily connected with the label printing only.
After a successful planning it’s time to get our hands dirty. It happens quite often that the mouldmaker needs to inject labelled samples. From our end we can produce sampling labels without the need of producing a cutting tool. These test labels can be cut on a digital plotter with highest dimensional precision and since no tool is involved, we can easily produce different versions of the label shape and different film options.
Since the IML automation is often not installed at the mouldmaker’s premises, the first trials need to be done manually. This means we go to the mouldmaker with the label samples and a portable statics generator which we use to keep the hand placed labels in position during moulding.
The following step is an industrial trial with which the general performance of the application is confirmed and some minor technical aspects like label positioning or overlaps can be fine-tuned thanks to some dedicated tools.
At this stage the productive phase is triggered. From now on Viappiani supplies production labels and everything should run smoothly, but we know we are not in an ideal world, we know that some things can happen. In these very dry and windy days for example, it might happen that IML labels get charged statically at the customer’s warehouse and cause label pick-up problems. In some cases, we can help by conditioning the labels and restore the average charging values.
Some other assistance we can offer is optimizing the general performance of an IML application. We can not promise miracles, but during more than 30 years we have seen really a lot of IML projects, and it happens we bring our contribution by grabbing at our experience.
Assisting the customer means listening to his needs, being well informed about the current status and about the targets. Every now and then packaging projects are reworked by changing substrates, changing label shapes, etc. This is just like defining a new project. In some cases the mouldmaker is involved, the Buying Department, the Marketing people and so on. Again, Viappiani sits around a table with all the partners and offers his support.

Even adding new designs might have an impact on an existing IML project.
Something we have done several times for our customers is for example a colour harmonization. A lot of different designs with a lot of different Pantone colours leads to higher production costs and in some cases we made a study to reduce the number of Pantone colours to for example CMYK + 2 Pantones across the whole range of SKUs. This was ending up in lower production costs and higher flexibility.
Offering our support to customers also means reacting to his needs with our Research & Development. It happened several times that an R&D project started from a customer’s need which could not be fulfilled with existing technology. The case of the full-peelable IML is a good example. A brand owner had a mould for an ice cream tub which was quite sturdy and thought about a complementary use. Since the container was robust, the idea was that after consuming the product, the customer could be able to reuse the ice cream tub as a fridge container. For this purpose, the marketing people wanted all the labels to be removable in order for the container to have a clean look, just like something you buy in a shop. We have been proposing removable IML labels since a lot of years, but in this case also the injection point area needed to be removable. We have been looking for a way to have an IML label which is completely removable and finally found a good solution for it. Once the technical problem was solved, we produced both the container and the lid labels as fully removable IMLs and the project was started. A single use plastic container was turned into a multiuse packaging. Another small step for assisting our customer, another small step for our environment.
VIAPPIANI PRINTING S.R.L.
Via Cassanese, 206
20054 Segrate – Milano, Italy
Tel. +39-02-70101112
Email: viappiani@viappiani.it
Web: www.viappiani.it