Vitalo Group is a renowned leader in the industry, boasting 85 years of expertise in thermoforming plastics and technical foam solutions. With a turnover of €80 million, the company operates from five production sites located in Belgium, Slovakia, France, and two in China (Chengdu and Suzhou). Their strong presence is supported by the three distinct brands, Vitalo, Insulo, and Starplast, which highlight Vitalo’s wide-ranging capabilities and their commitment to delivering customized and high-quality solutions to customers worldwide.
Vitalo’s core focus is on delivering exceptional products using advanced plastics processing technologies and technical foam solutions to cater to the diverse needs of acoustic and thermal insulation.
Interview with Lola Frosio, Marketing Manager at Vitalo Group.
Easy Engineering: What are the main of activity of the company?
Lola Frosio: The Vitalo Group has established itself as a prominent leader across various industries, catering to the unique requirements of diverse sectors. Our extensive expertise encompasses critical areas such as aerospace, medical, agriculture, automotive, and more. Under our brand VITALO, we have perfected our proficiency in both thick and thin gauge thermoforming techniques, working with a diverse range of materials, in opaque plastics. Our capabilities also extend to inside and outside cleanroom manufacturing, ensuring the highest quality standards.
Through our brand INSULO, we excel in processing insulation materials and employing thermocompression methods for natural and synthetic fibers. This expertise enhances our capabilities in sectors such as HVAC and off-highway applications, particularly focusing on acoustic performance.
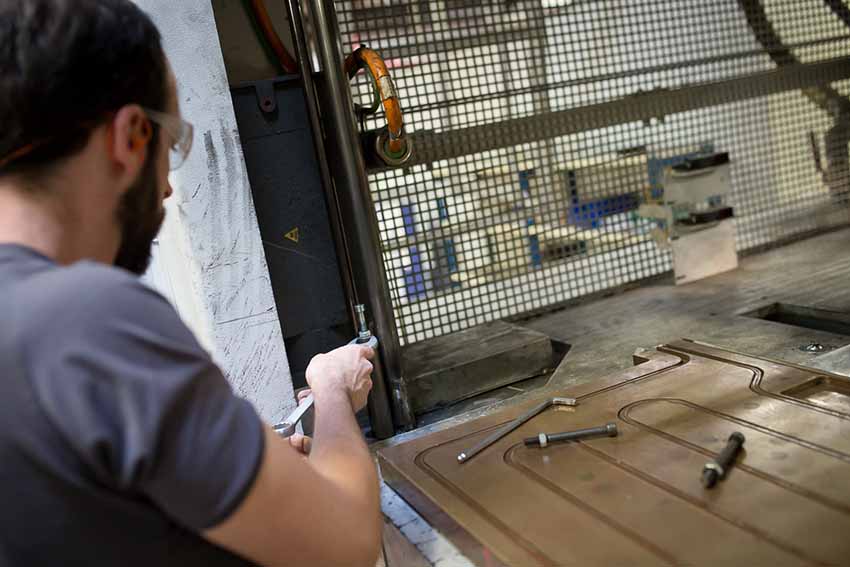
Our brand STARPLAST is dedicated to specializing in the production of customized, high-quality thermoformed pieces using transparent plastics. We excel in crafting a wide range of products, including windshields, canopies, and various other items, with a strong focus on delivering exceptional transparency and precision. Our expertise in thermoforming allows us to create tailor-made solutions that meet the unique requirements of our customers, ensuring top-notch quality and superior performance.
These specialized competencies enable us to provide comprehensive solutions that consistently yield exceptional results, effectively addressing the complex challenges faced by engineers in their respective fields. The Vitalo Group remains dedicated to delivering tailor-made products of the highest quality that meet the rigorous standards of their respective industries.
E.E: What’s the news about new products?
L.F: At Vitalo Group, we are committed to optimizing design and process efficiency to deliver effective solutions to our customers. Our dedication to innovation drives us to develop new products that meet the evolving market demands. Sustainability is a core focus of our product development initiatives. We actively incorporate recycled materials, minimize waste generation, and prioritize environmental responsibility.
We are thrilled to introduce a groundbreaking product tailored for the aeronautical market. Our research and development team has achieved a remarkable milestone by engineering an air duct that is 90% lighter than existing polycarbonate ducts. This breakthrough offers substantial weight savings without compromising performance and reliability. It provides our esteemed customers, including renowned companies like AIRBUS and Dassault Aviation, with a distinct competitive advantage, showcasing our commitment to pushing product development boundaries.
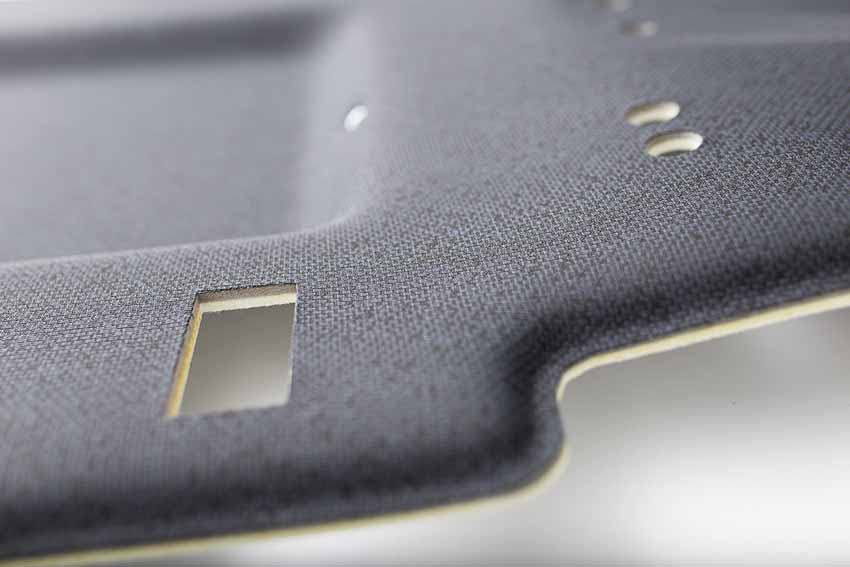
Our close partnerships and customer feedback are integral to our innovation process, allowing us to continuously improve and refine our products. As we envision the future, we remain dedicated to exploring innovative and sustainable solutions that deliver superior performance, efficiency, and environmental responsibility.
E.E: What ranges of products?
L.F: At Vitalo Group, we provide a wide range of high-quality thermoformed plastic products for diverse industries worldwide. Our portfolio includes single or twin-sheet thermoformed plastics, vacuum forming, and high-pressure forming. We offer opaque plastic components designed to meet industry-specific requirements, ensuring optimal performance. Additionally, our transparent glazing solutions are meticulously engineered to deliver exceptional clarity and optical properties. We also specialize in technical foam products that offer superior thermal and acoustic insulation. With a focus on meeting the unique needs of various industries, our tailored solutions exemplify our commitment to customer satisfaction.
E.E: At what stage is the market where you are currently active?
L.F: The market in which Vitalo Group is currently active is experiencing a phase of significant growth. Despite the strict regulatory constraints surrounding the use of plastic products, the market is thriving. This growth can be attributed to increasing demand from various sectors, particularly the medical industry and the food packaging sector, where there is a rising need for packaged or processed food. Vitalo Group’s presence in multiple sectors further strengthens our position, allowing us to capitalize on the opportunities presented by this growing market.
In addition, our marketplace in acoustic and thermal insulation is booming, with the development of heat-pumps and more generally in the HVAC industry.
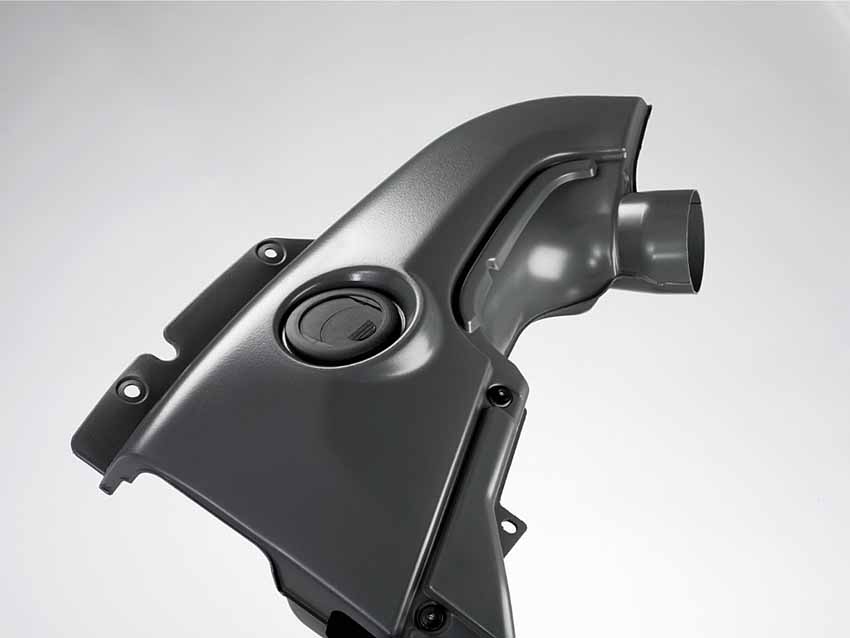
E.E: What can you tell us about market trends?
L.F: Market trends show rising demand for sustainable packaging solutions and innovative technical foam products. Thermoformed plastics are highly sought after in the food industry, providing effective protection against moisture, bacteria, and odors. This segment is projected to witness continuous growth. In the automotive sector, there is a strong demand for thermoformed plastic parts, contributing to lighter and more durable components like bumpers, panels, and cladding. At Vitalo Group, we closely monitor these trends, integrating them into our product development strategies.
In the insulation field, the need for quieter products and thermal insulation to reduce CO2 emissions is increasing. Our activities align with these requirements. Our 100% plastic thermoplastic products are easily recyclable compared to composite materials like RIM, RTM, or FRP. Thermoformed plastics also offer significant weight advantages, crucial for CO2 savings, over alternative options like metals or composites.
E.E: What are the most innovative products marketed?
L.F: In addition to our innovative air duct cited earlier, we introduce Light & Strong, a cutting-edge product leveraging our expertise in thermos-compression technology. Our revolutionary process compactly combines non-woven polyester fibers, allowing exceptional performance. With the flexibility to hybridize different fiber types, including polyester, polyamide, glass fiber, carbon fiber, flax, basalt fiber, and more, we push industry boundaries.
By precise control of compaction level and temperature, we fine-tune material properties to match specific requirements. Adjusting void presence balances stiffness with enhanced impact and acoustic performance.
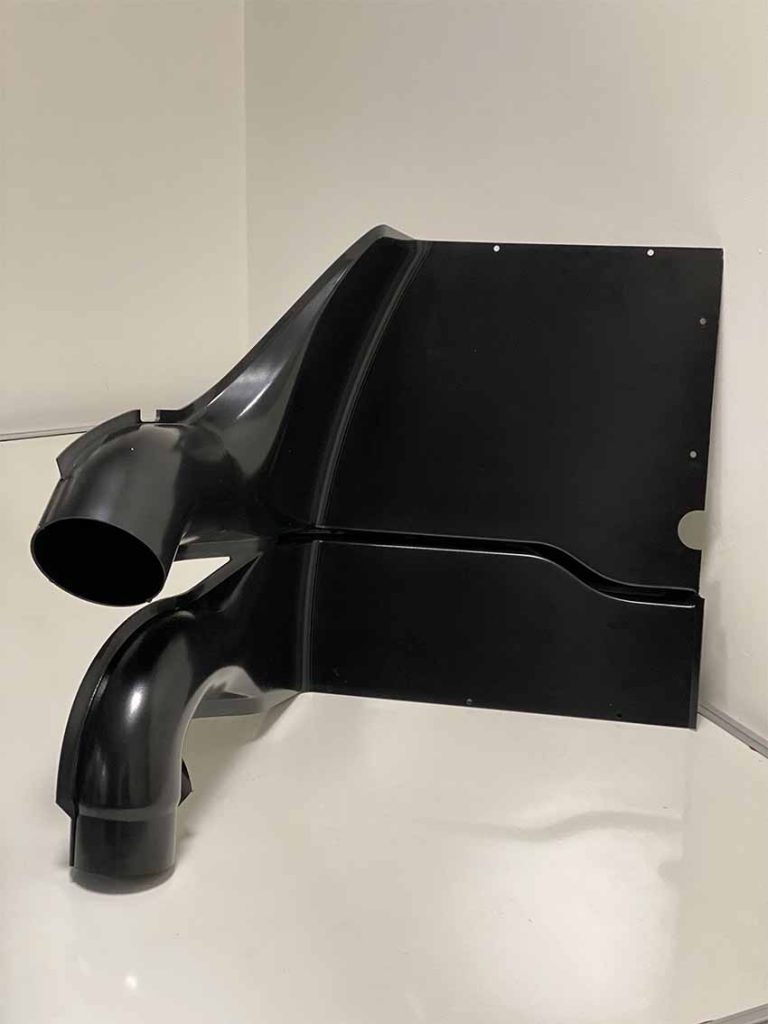
Vitalo Light & Strong (L&S) boasts outstanding mechanical properties, high resistance to impact, weight, and pressure. It offers flexibility and durability in demanding environments, minimizing brittleness.
Our approach emphasizes utilizing recycled non-woven fibers, showcasing sustainability and responsible resource usage.
We understand each customer’s unique requirements, adapting and customizing materials to match desired properties.
E.E: What estimations do you have for 2023?
L.F: For 2023, we have optimistic estimations in terms of growth and expansion. We aim to further strengthen our commitment to sustainability, expand our product portfolio, forge strategic partnerships, and continue delivering superior quality thermoforming plastics and technical foam solutions to our valued customers around the world.