Construction waste such as concrete washout is under scrutiny from environment agencies around the world, largely due to its heavy-metal content, notably chrome. With the rate of construction unlikely to slow down, there will be no let-up in the quantity of concrete washout produced. There needs to be an increased awareness of technology that can help concrete plants and construction firms meet growing demand, without suffering legal, financial or environmental consequences associated with waste disposal. Among such technologies are the latest Qdos chemical metering pumps and Bredel hose pumps from Watson-Marlow Fluid Technology Group (WMFTG), which are highly proven in tough applications such as construction sites, aggregate and concrete production plants.
Alkalinity issues
Water contacting freshly exposed or poured concrete takes on an alkaline pH (circa 13) due to chemical reactions between the water and free lime particles within the cement.
At a typical concrete plant, up to 12,000m3 of water is consumed every year, which means that the washing down of machinery, equipment and transportation vehicles becomes problematic.
The issue is equally prominent at construction sites, where there are many common sources of alkaline waters, including: washing chutes and drums used with fresh concrete; cutting or coring concrete structures; hydro-demolition processes; surface water run-off from recently lime-stabilised sites; stockpiled or spread-crushed demolition materials; placement of fresh concrete beneath groundwater (such as piled foundations).
Harmful effects
While most are familiar with the dangers of acids, highly alkaline substances such as concrete wash water can be just as corrosive, and if left untreated can cause concrete burns, damage to vegetation and the surrounding ecosystem.
The UK Environment Agency publishes Pollution Prevention Guidelines, including PPG6 ‘Working at construction and demolition sites’, a guideline that is intended to assist with those in the construction and demolition industry. This states that precautions must be taken to ensure the complete protection of watercourses and groundwater against pollution. Further, it states that ‘Suitable provision should be made for the washing out of concrete mixing plant or ready-mixed concrete lorries. Such washings must not be allowed to flow into any drain or watercourse.’ Ready-mixed concrete trucks should not be allowed to wash out anywhere other than the areas designated for the purpose.
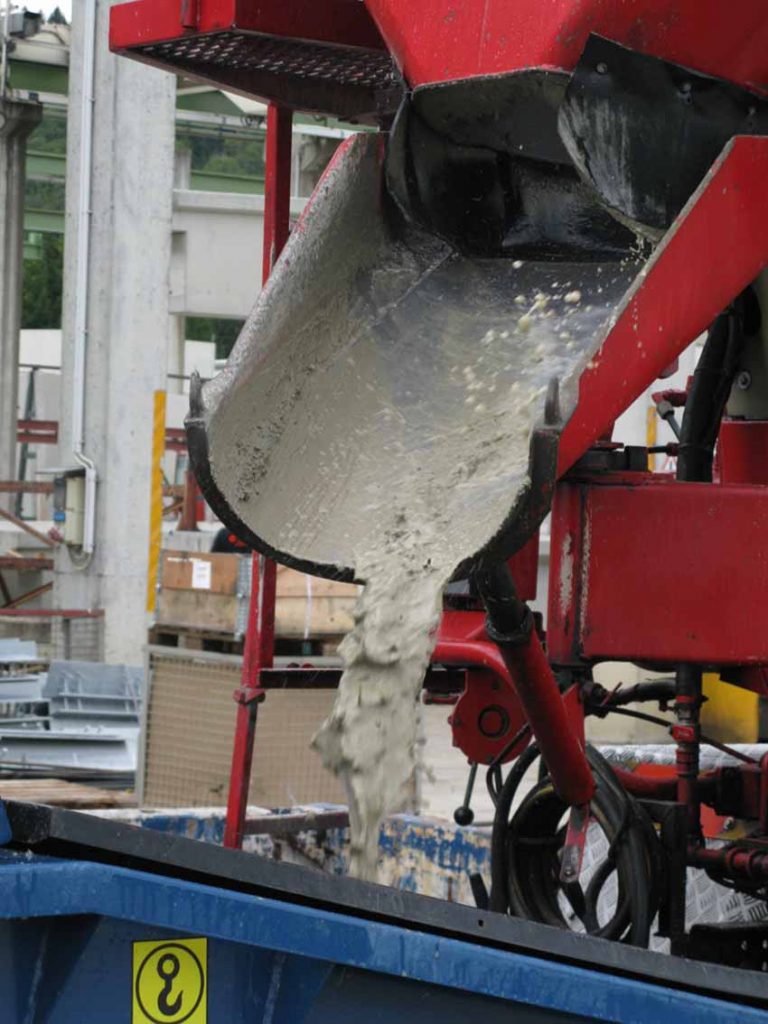
Dilution or neutralisation?
So, how does the industry go about resolving the high pH of wash water? Some think it only requires dilution, but this is a popular misconception. In fact, to dilute one IBC of concrete wash water at pH 12, the equivalent water of that contained by four Olympic swimming pools would be needed just to bring it back to neutral (pH 7).
The typical discharge consents for controlled waters such as surface watercourses and groundwater require a pH of between 6 and 9 (subject to Environmental Permit Limits where relevant). As an alternative, high pH water can be tankered off-site, although this is well documented as an expensive option.
To adjust high pH wash water in line with consent levels, a process of neutralisation using controlled amounts of reagent is required. Typical reagents include mineral acid (either sulphuric or hydrochloric acid), citric acid, carbon dioxide (CO2) and self-buffering solutions.
The stand-out reagent performer is CO2, largely because the very weak acid created offers high levels of control. In addition, slower reaction rates are suited to automatic pH adjustment systems, and it is virtually impossible to acidify the water through overdosing.
Proven solutions
In a typical treatment system, initial pH adjustment is performed to maximise the precipitation of solids and the treated water passes through a lamella clarifier. This process is followed by the recovery of suspended cementitious solids using flocculants dosed by WMFTG’s high accuracy Qdos chemical metering pumps, to aggregate the fine particulates into rapidly settling clumps.
Following treatment, settled solids from the water collect in a hopper where the resulting sludge can then be pumped by Bredel hose pumps into a skip or sludge storage tank, or for off-site disposal.
The level and type of solids in the sludge varies greatly but does not impact the capacity of the hose pumps, which can transfer up to 80% solids in suspension. Furthermore, flow is entirely independent of suction and discharge conditions.
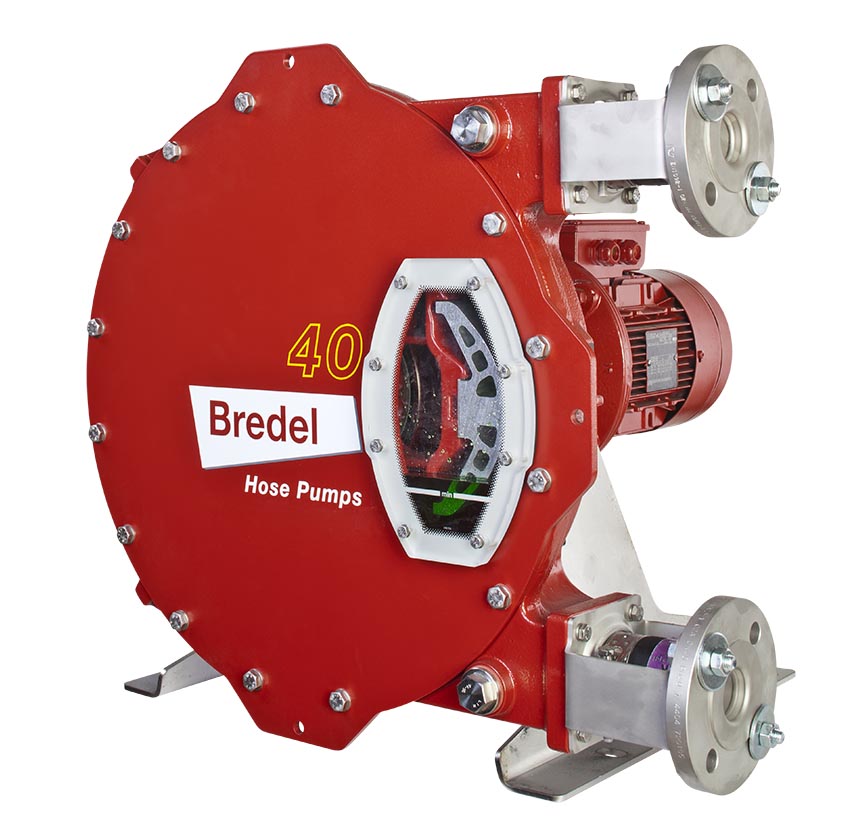
Peristaltic pumps from WMFTG are increasingly favoured for concrete washout applications, due to their extremely low maintenance requirements, and safe, non-contacting pumping method. Without mechanical seals or valves to leak or corrode, Qdos and Bredel pumps completely contain the pumped fluid, preventing operator contact with chemicals, or spillage of untreated sludge.
Importantly, peristaltic pumps do not require skilled personnel for maintenance. A simple Qdos ReNu pumphead or Bredel hose change, takes only minutes and can be performed on site. Their low cost maintenance adds to the list of reasons that growing numbers of plant contractors are turning to WMFTG pumps for chemical dosing and sludge transfer duties in the final stages of pH adjustment and treatment of concrete wash water.
Clean, pH-adjusted and sediment-free water can then be re-used on site, for tanker and conveyor washout, providing further cost savings.