Waygate Technologies (WT) is the world leader in non-destructive testing (NDT) and industrial inspection solutions, providing innovative technologies and services to various industries such as aerospace, automotive, electronics, energy, battery, and additive manufacturing. While WT is a truly global business with around 1.500 experts and talents and an expertise that goes back over 125 years in the market, its HQ is in Huerth, Germany.
Waygate Technologies is part of the Inspection portfolio within the energy technology company Baker Hughes.
Interview with Henning Juknat, Global Communications Leader at Waygate Technologies, a Baker Hughes business.
Easy Engineering: What are the main areas of activity of the company?
Henning Juknat: Our main areas of activity include hardware and software solutions as well as services in industrial radiography (X-ray) and computed tomography (CT), remote visual inspection (RVI), ultrasound (UT), and robotic inspection as well as software solutions for inspection data analysis and management. With our solutions, we help our customers make flawless products, keep people, assets and the environment safe, and increase production efficiency.
E.E: What’s the news about new products/services?
H.J: We are continuously launching innovations in all disciplines of NDT technologies that meet ever changing demands in various industries – from more stringent safety regulations to the deployment of new materials or new technologies inspired by the global energy transition efforts. Some of our most recent product introductions have been in the field of portable ultrasonic inspection equipment and remote visual inspection for the energy and aviation sectors, or a new industrial 3D CT solution for application in the automotive industry, amongst others.
E.E: What are the ranges of products/services?
H.J: We offer advanced 2D X-ray systems and 3D CT scanners for the detection of internal defects, deviations in thickness, assembly details, and other components and geometries that are otherwise invisible. Furthermore, we develop solutions for automated ultrasonic testing of cracks, welds, flaws and corrosion found in pipes used in the oil and gas industry or aircraft wing structures for example. We also offer portable ultrasound equipment such as ultrasonic flaw detectors, thickness gauges, probes and transducers.
In the field of visual inspection our portfolio includes video borescopes with the highest image quality and measurement capabilities to inspect the inside of tanks and pipes or aircraft turbine blades. We have also been offering robotic solutions for the inspection of hazardous and confined spaces for several years now. Our product range is completed by services and software solutions for inspection data analysis and management, which help our clients streamline inspection processes, reduce the potential for human error and better predict and plan maintenance and repair times.
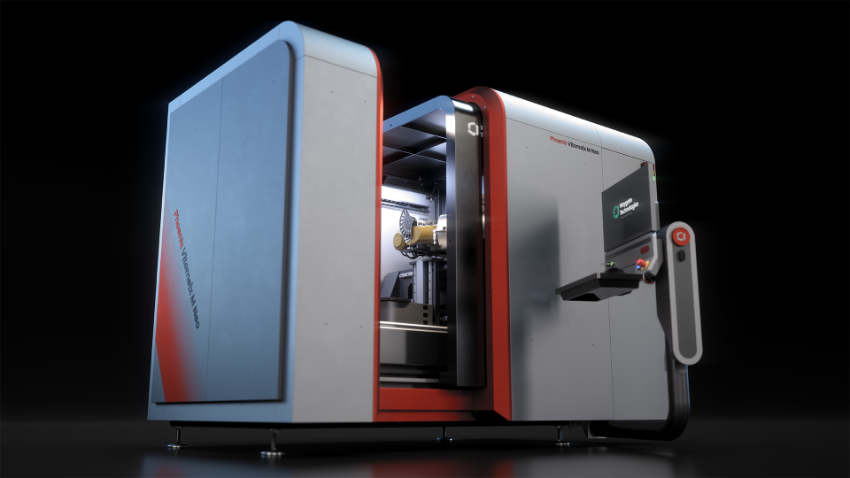
E.E: What is the state of the market where you are currently active?
H.J: The NDT and quality inspection market is highly competitive. The demand from customers for more efficient and reliable NDT solutions is increasing, because consolidation and rising cost pressures across a multitude of industry sectors are making efficient production and operations more and more important for them. Be it battery manufacturers, aircraft manufacturers and MROs (Maintenance, Repair & Operations), electronics providers or automotive companies and suppliers.
For example, in the battery industry, the intricate designs and complex materials used, such as in lithium-ion and solid-state batteries, present significant challenges. These include ensuring the integrity of delicate internal structures and managing the thermal and mechanical stresses that batteries are subjected to throughout their life cycle. Non-destructive testing (NDT) is crucial for detecting potential issues like electrode misalignment and internal shorts, which are critical for safety and performance. Additionally, as battery production scales to meet growing demand, particularly for electric vehicles, maintaining consistent quality through NDT becomes essential.
The automotive industry, transitioning rapidly towards electrification, faces its own set of challenges. The diverse range of materials now used in vehicles, from advanced alloys to composites, requires versatile NDT methods to ensure component integrity and safety. The complexity of automotive assemblies also necessitates sophisticated NDT techniques that can inspect components like engine parts and suspension systems without disassembly. Furthermore, the shift to electric vehicles intensifies the need for effective inspection of batteries, electric motors, and other related systems.
For the aviation industry, the stakes are particularly high given the zero-tolerance policy for failure. Aircraft are subject to extreme operational stresses and must meet stringent safety standards. The use of composite materials, while beneficial for reducing weight and improving fuel efficiency, introduces challenges such as detecting delamination or water ingress, which can compromise the structural integrity of the aircraft. NDT plays a vital role in the periodic and detailed inspections required to manage the longevity and maintenance of aircraft, ensuring that they can safely remain in service over long periods.
E.E: What can you tell us about market trends?
H.J: Emerging technology trends in NDT include the adoption of digital technologies, such as artificial intelligence, machine learning and robotics that offer greater accuracy, efficiency, and safety in nondestructive testing procedures.
The integration of robotics and automation in the NDT industry is poised for significant growth through 2024. With the implementation of cutting-edge sensors and imaging technologies, robotic inspection systems will become increasingly common, especially in areas that are difficult for human inspectors to access. The use of these advanced solutions will make inspections in hazardous environments safer and more accurate. In addition, these innovative systems will improve efficiency and streamline inspection times, resulting in less downtime and more accurate and timely results.
Looking ahead to 2024, we anticipate a substantial increase in the use of AI and ML algorithms within NDT processes. By automating data analysis, these technologies will facilitate faster and more precise automated defect recognition, ultimately improving inspection efficiency and reducing human error. Additionally, this integration will provide valuable insights for predictive maintenance, enabling companies to proactively address potential issues before they become major problems.
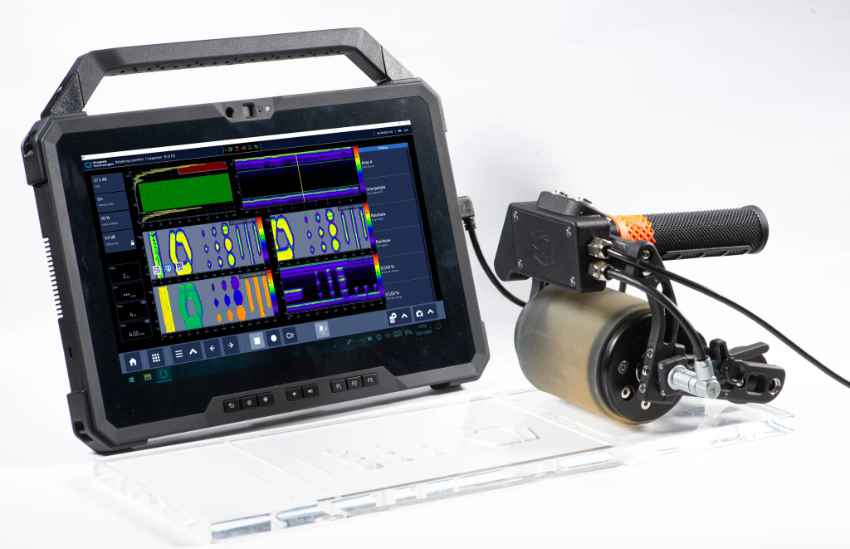
We can also expect further advancements in digital radiography technology. One of its key areas of focus is higher resolution imaging, which will allow for even greater accuracy and precision in detecting defects.
Phased Array, matrix array and total focusing method (TFM) technologies will become even more important in ultrasonic testing. The increased use of PA and TFM will lead to better material characterization and increased reliability in various industries such as manufacturing, aerospace, automotive and others.
Another area of development is enhanced portability, making it easier to use flaw detectors and inspection devices in a variety of inspection scenarios. The industry is ready to embrace more compact and user-friendly instruments, which will provide greater flexibility, versatility and convenience.
E.E: What are the most innovative products/services marketed?
H.J: Our broad portfolio of products and services in industrial radiography (X-ray) and computed tomography (CT), remote visual inspection (RVI), ultrasound (UT), and robotic inspection as well as software solutions make us a global leader in non-destructive testing (NDT). In order to fully serve our customers and their diverse requirements, we manufacture a wide variety of award-winning products. Some of our recent product launches include:
Krautkrämer RotoArray comPAct is the first instrument to feature our new comPAct technology, combining the performance of a complete phased array (PA) ultrasound inspection system in a single probe thanks to miniaturized instrument electronics.
Everest Mentor Visual iQ+: Utilizing advanced analytics for novel inspection approaches, the new state-of-the-art flagship video borescope technology harnesses the power of Artificial Intelligence (AI) and machine learning to enhance data quality and reduce inspection time for critical inspections across multiple sectors, including aviation and power generation.
The new CT flagship scanner Phoenix V|tome|x M Neo is a highly versatile premium CT cabinet system. The system boasts many features that further increase flexibility, speed, and detection quality and is suitable for a wide range of 3D metrology, research, and evaluation applications in the laboratory environment, as well as automated precision inspection in production.
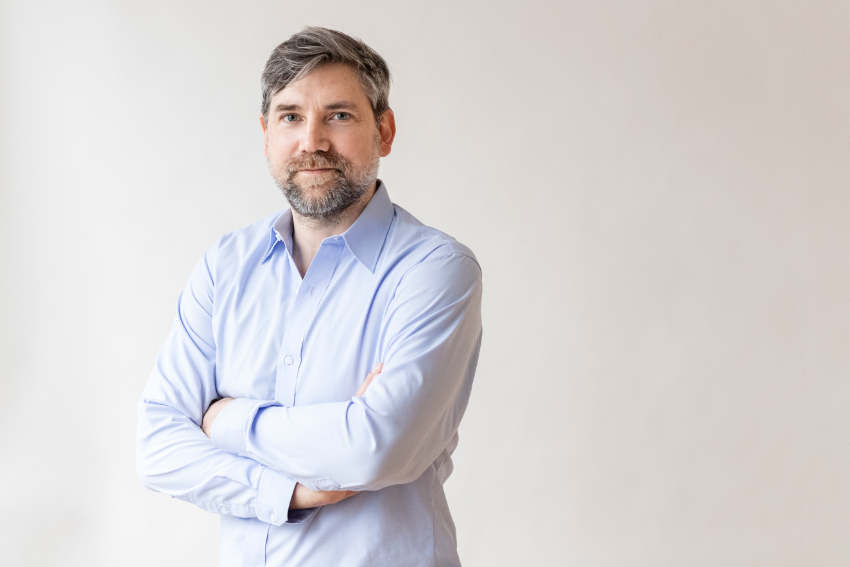
E.E: What estimations do you have for 2024?
H.J: The energy transition is a critical issue that will shape the future of our planet. As we face the challenges of emissions and climate change, it has become increasingly important to find solutions to the technological, regulatory and economic obstacles presented by the “energy trilemma”. This shift towards sustainability is having an impact also on the NDT and inspection market.
In particular, the e-mobility/battery sector is experiencing a surge in demand for safe, reliable and efficient inspection solutions that can be applied as early as possible in the production process.
Innovative inspection techniques combining hardware and software gain demand as they offer improved defect characterization and inspection capabilities, contributing to better material characterization and increased reliability in critical industries such as aerospace, automotive, battery, electronics and manufacturing. As we move toward a more sustainable future, these innovative technologies will play a critical role in ensuring the safety and efficiency of our energy systems.