Thanks to advances in rubber technology, the wear life of today’s industrial conveyor belts should be at least two or times longer than it was as recently as a decade ago. Here, conveyor specialist Bob Nelson explains the causes and effects of conveyor belt wear and tear and the reasons why there are such huge differences in operational lifetime and durability between one manufacturer and another.
Causes of wear and tear – The wear and tear that takes place on the outer covers of rubber belts is commonly referred to using the umbrella term ‘abrasion’. Some 80% of abrasive wear occurs on the top cover while 20% occurs on the bottom cover and is mainly caused by friction contact with drums and idlers. Top cover wear is primarily caused by two actions. First is the abrasive action of the materials being conveyed, especially at the loading point or ‘station’ and at the discharge point and is particularly associated with ‘fine’ materials such as sand or gravel, which literally act like a piece of coarse sandpaper constantly scouring the rubber cover.
Cutting and gouging
However, there is more to the wearing process than simply abrasion because another significant cause is the cutting and gouging of the rubber caused by materials that have sharp edges such as coarse aggregates and rocks. The heavier and sharper the material then the greater the wear. The durability of a belt therefore also depends on the overall strength and resistance to cut and tear propagation of the rubber compound used for the covers. If that resistance is low, then a seemingly insignificant area of damage in the cover can easily increase due to the continuous material loading and the relentless flexing around the drums and pulleys. In time, the damaged area spreads, and links up with another area of damage causing small pieces of rubber to be cut from the surface.
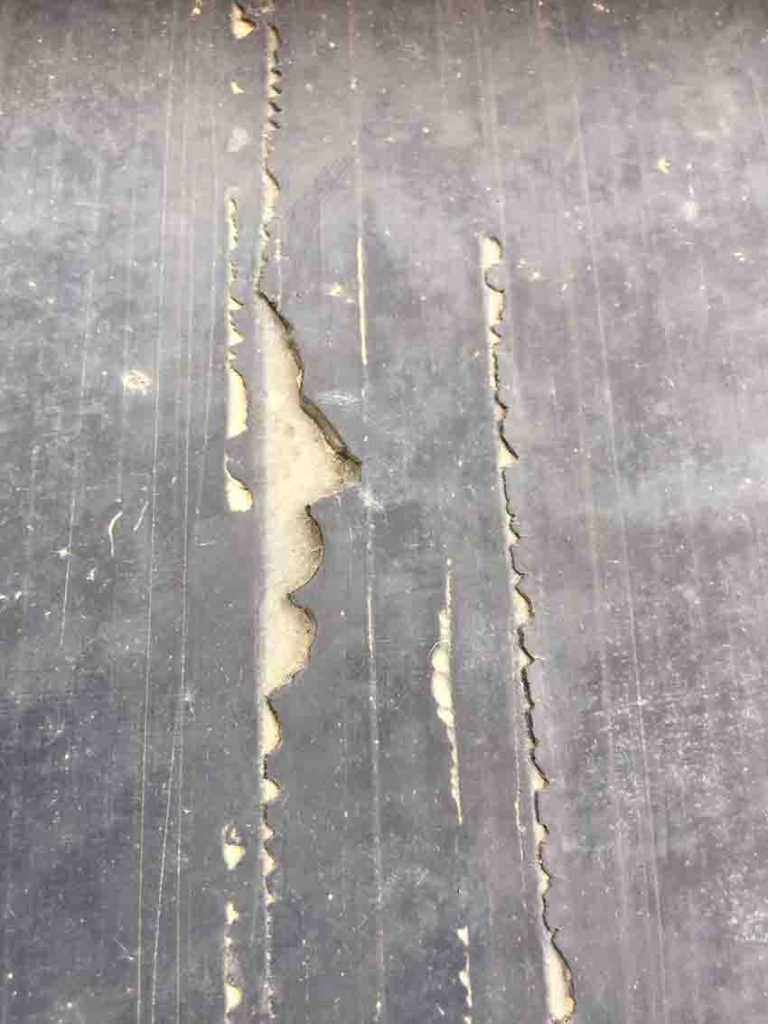
There is no doubt that the biggest single reason for rapid belt cover wear is because the rubber compound used by the manufacturer does not provide the level of wear resistance needed for the job. For example, a manufacturer may claim that their belt meets DIN Y (ISO 14890 L) standards for abrasion resistance (maximum volume loss in cubic millimeters of 150 mm³ under ISO 4649 / DIN 53516 test methods). However, in reality, the wear resistance may only be borderline at best or, quite possibly, be totally inadequate. One recent example I came across was a belt with an abrasion resistance of 264 mm³, which is more than 75% higher* than the maximum level for DIN Y compliance.
(* When comparing abrasion test results, higher figures represent a greater loss of surface rubber under testing, which means that there is a lower resistance to abrasion. Conversely, the lower the figure the better the wear resistance).
Although increasing the cover specification might seem a logical solution, that does not necessarily follow. One manufacturer’s DIN Y (ISO 14890 L) used for normal service conditions can often be more durable and wear resistant than another manufacturer’s DIN X (ISO 14890 H) or even DIN W (ISO 14890 D), which are usually reserved for heavier-duty applications. Laboratory testing regularly exposes instances of belts claimed to be DIN X or DIN W that fail to even achieve the DIN Y standard. This most often applies to belts imported from Southeast Asia rather than those genuinely made in Europe. **
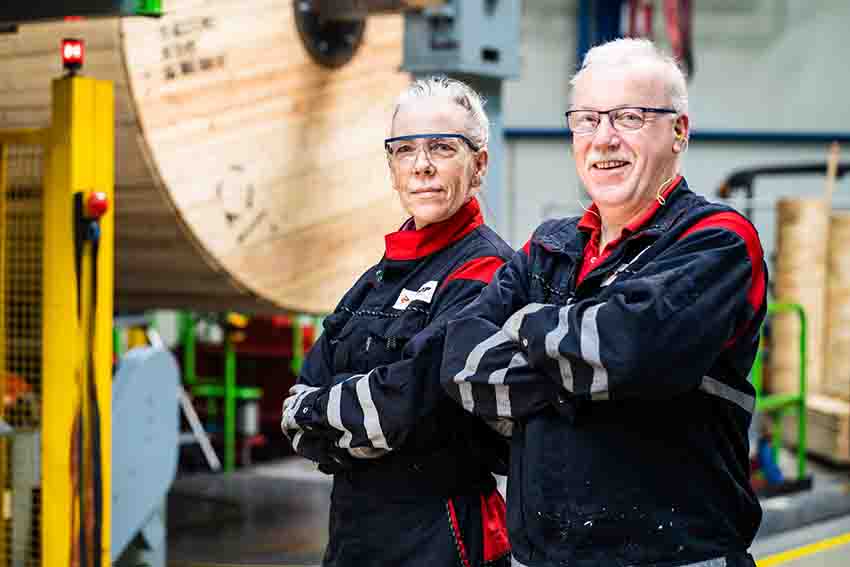
The only real solution is to only buy belts where you are totally confident of their provenance (manufacturer’s origin) and where the manufacturer clearly states the level of anticipated performance rather than simply claiming to have been tested to a certain DIN or ISO standard. (** With the exception of Fenner Dunlop, all European manufacturers now supplement their production with belting that is made in Southeast Asia). My best advice is to avoid so-called ‘economy’ belts and always ask for certified confirmation of the actual place of manufacture.
Rip, tear and impact damage
The ability of a belt to withstand the forces that cause rip, tear and impact damage is often more important than any other physical attribute. A ‘rip’ occurs when a sharp object punctures the belt and becomes trapped, cutting the belt lengthwise as it is pulled against the object. A ‘tear’ is when a section of belt is pulled apart in opposing directions. Impact damage is caused by heavy objects falling from height that pierce the outer cover and damage the inner carcass. In an attempt to prolong operational lifetime, many conveyor belt users resort to fitting belts with increasingly thicker covers and heavier carcasses. However, this is usually a mistake. Firstly, simply using more of the same material will not provide the solution. Secondly but just as importantly, thicker, heavier belts can cause other problems including lack of troughability, steering and handling problems and dynamic stress due to the pulleys and drums now being too small.
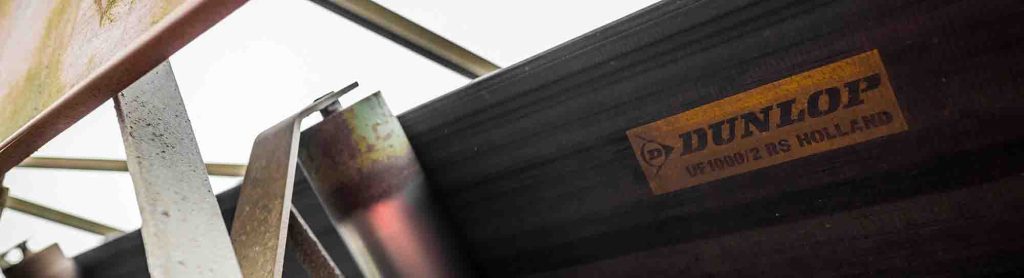
The most practical and economical solution is to fit a conveyor belt that has been specifically engineered for the purpose, such as Fenner Dunlop UsFlex or Ultra X, which are proven to last up to four or five times longer than conventional multi-ply conveyor belts. True, the initial buying price will be much higher but over the lifetime of the belt, the cost will be substantially less, as well as significantly less output disruption caused by unplanned stoppages to carry out repairs. As they say, price is what you pay but cost is what you actually spend.
An invisible cause of wear & tear – ozone and ultraviolet light.
Ozone (O3) occurs naturally in the upper atmosphere. At high altitude, ozone acts as a protective shield but at low altitude it becomes a pollutant created by the photolysis of nitrogen dioxide (NO2) from sources such as automobile exhaust and industrial discharges. This process is known as ozonolysis and causes cracks to form in rubber that is under tension. The dynamic stress a conveyor belt undergoes while in operation is considerable. Ozone attacks the points where the strain is greatest, activating an oxidation process causing the rubber to become brittle, lose strength and increasingly less able to withstand virtually every kind of wear. The second destructive force is ultraviolet light from sunlight and artificial (fluorescent) lighting, which accelerates rubber deterioration (known as ‘UV degradation’) by producing photochemical reactions that promote the oxidation of the rubber resulting in a loss in mechanical strength. In short, ozone and ultraviolet light damage significantly reduces the ability to withstand the forces that cause wear and tear.
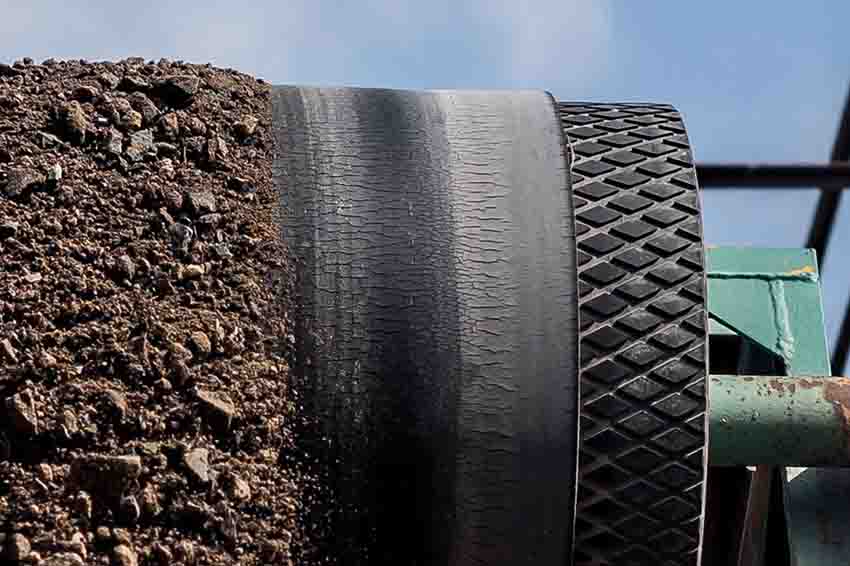
Although protection against ozone and ultraviolet damage is easy to achieve by using antioxidants within the rubber compound, laboratory testing reveals that some 90% of belts sold in Europe, Asia and Africa have virtually no protection. The reason is that antioxidants are regarded as an ‘avoidable cost’ by manufacturers wishing to be ‘competitively’ priced. The solution, therefore, is to always insist on the provision of certification confirming that the belt you are buying has successfully passed the EN ISO 1431/1 procedure B static ozone resistance test (@20% elongation; 50 p.p.h.m. ozonised air and 40°C).
Wear and tear – a price to pay.
Rubber forms some 50% of the cost of a conveyor belt so it is consequently the biggest opportunity for manufacturers to cut costs in order to achieve greater price competitiveness. In such a cut-throat market, it is therefore no surprise that the primary reason why belts lack durability, is that they have been made using low grade ‘economy’ raw materials.
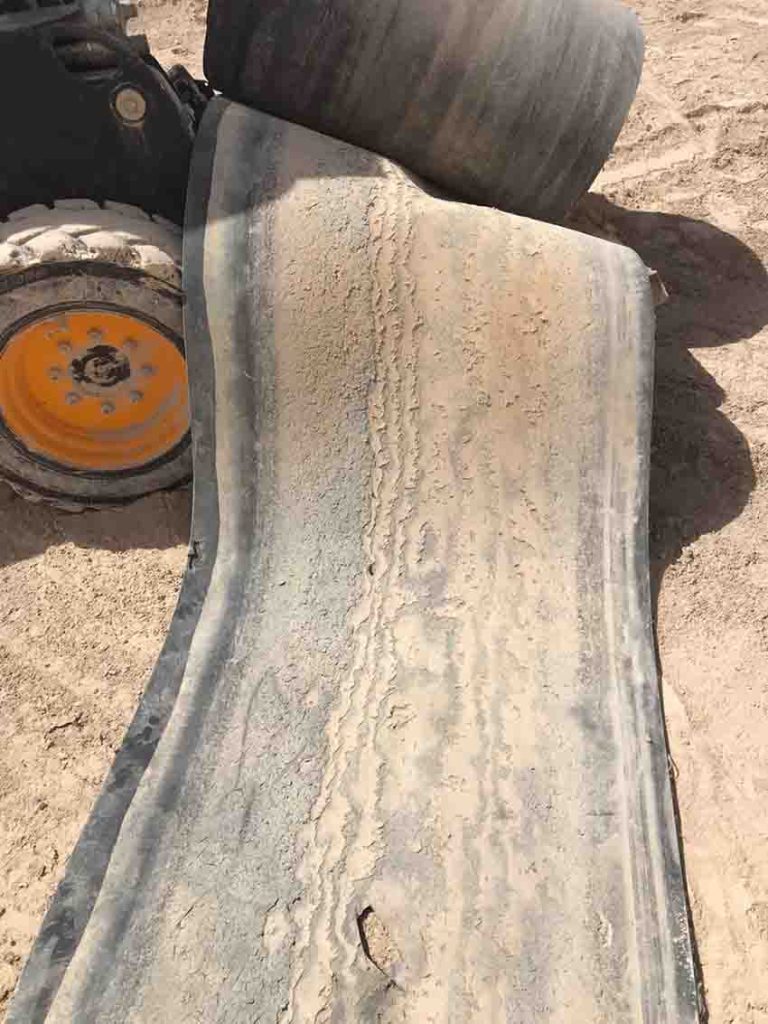
The simple solution is to avoid short-term economics and not buy belts simply because they are priced attractively. If anything, low prices should serve as a warning sign because there is a direct connection between price and durability and therefore, the whole life cost of the product. The mathematics are simple. Quality belts last significantly longer and therefore cost considerably less.
Autor: Bob Nelson
https://www.fennerdunlopemea.com