With global warming intensifying – testing the resilience of our economy, our natural resources, and our physical wellbeing – the manufacturing industry has a direct role to play in curbing carbon emissions and waste.
But to do so is no easy feat. It will require each relevant party throughout the supply chain to embrace meaningful sustainable practices. These include saving on resources, reducing collective energy usage, and decreasing emissions, and more – all while still meeting the needs of customers worldwide.
OEMs and EMSs – original equipment manufacturers and electronics manufacturing services – are no exception.
Fortunately, there is at least one tangible solution that is well within reach: leveraging visual AI and big data to ensure the quality of electronic components.
Waste Not
Despite manufacturers’ meaningful due diligence, defective electronic components still make their way into electronic devices. When these devices inevitably malfunction or underperform, their next destination is the dumpster, contributing to an annual generation of 40 million tons of electronic waste. That’s the equivalent of throwing away 800 laptops every second.
This problem is compounded by the rising demand for smart components and chip production. Chip manufacturing requires exorbitant amounts of energy and water, which produces hazardous waste as a byproduct.
Considering the scarcity of the materials used to fabricate our essential electronic components, it is imperative that waste is as limited as possible.
Limited Supplies Call for Precise Inspection
One way to reduce the failure rate of electronic products and improve their long-lasting reliability is to integrate exacting component inspection procedures into the manufacturing process. Advanced visual AI analytics and big data are making these capabilities more accessible and effective than ever before.
Manufacturers have thus far lacked the tools capable of providing 100% real-time inspections of electronic components prior to and during the assembly process. As a result, oxidized or corroded leads, for example, have the potential to slip past inspection, eventually corrupting electronic products, which are more often thrown away than properly recycled.
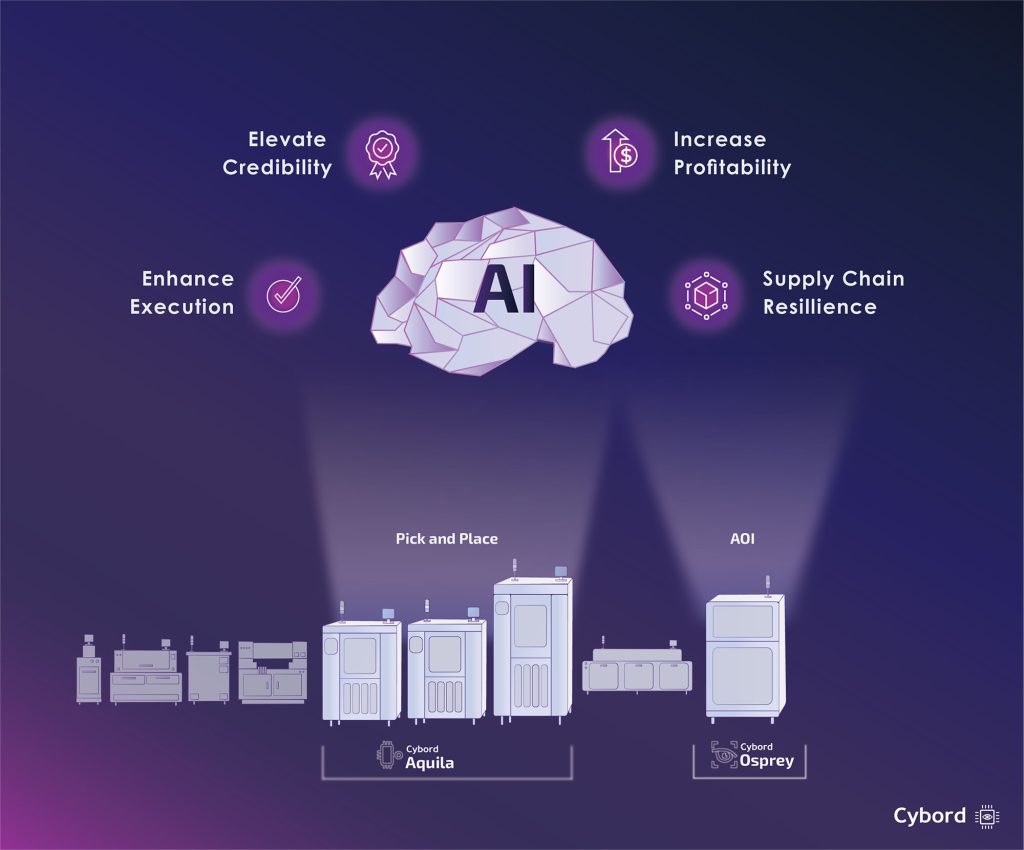
But those inspection tools are available.
Cybord’s visual AI-powered forensic analysis solution can identify errors, defects, and counterfeit components preemptively and at scale. This prevents them from being installed into the circuit boards of electronic products, without disrupting or delaying the manufacturing process. In fact, our internal research revealed that our solution’s quality detection capabilities were found to be more than 99.5% accurate when tested against 3 billion components.
By vastly improving OEMs and EMSs chances of catching these potential errors, Cybord is enabling them to decrease the rate of e-waste and its detrimental impact on the environment.
The ability to analyze the quality of each and every individual electrical component from procurement to assembly has massive potential for the manufacturing industry with regards to sustainability and beyond OEMs and EMSs can avoid crippling recalls and time-consuming reworks – both of which generate excessive waste and harmful emissions.
A Higher Standard
Industry leaders need to adopt alternative strategies and operational methods that embrace sustainability and bolster their bottom lines.
Despite the obvious need for better quality assurance, this remains a challenging goal for OEMs and EMSs. Checking the quality status of billions of individual components just isn’t feasible without a big data-backed visual AI analytics solution.
Cybord’s proprietary technology, however, can help turn the tide. With it, electronic manufacturers can ensure product functionality long-term, reduce e-waste and carbon emissions, and raise the standard for industrial sustainability, and quality as well.
Autor: Eyal Weiss, CTO and Co-Founder of Cybord.