With a newly developed CO2calculation tool, the plastics company and medical supplier Carmo is preparing itself and its customers for a future with strict documentation requirements.
Starting in 2024, the new EU ESG-directive, CSRD, will require major listed European companies to increase documentation of their production’s environmental impact. The new directive also impacts distributors, where companies such as the plastic producer Carmo must now report more data on their environmental footprint than before.
However, Carmo is well prepared for the new requirements, as the company from Denmark has worked intensively for several years on mapping its environmental impact. The initiative has led to the development of Carmo’s own calculator under the designation,” the Carmo carbon footprint calculator”.
“Our data collection has come so far that we can calculate and report exactly what the individual parts of production contribute to the overall carbon footprint of a product. Including the climate impact from electricity consumption, transport emissions, and manufacturing of the raw materials, and the estimated production wastage on the finished product,”, says Anders Johnsen, Development & Technology Director at Carmo.
“We can thereby provide a well-documented report of the carbon footprint, which also meets CSRD requirements. At the sustainability consultancy Viegand Maagøe, which has assisted Carmo’s ESG work since 2018, there is no questioning about the value of Carmo’s efforts for themselves and their customers.”, adds Johnsen.
“Honesty and transparency will become important competitive parameters with CSRD. Because Carmo has been involved in ESG work for so long, they are among the leaders in the field. And their customers will benefit from that in the long run”, says Lasse Vinblad Thaisen, Senior Project Manager at Viegand Maagøe.
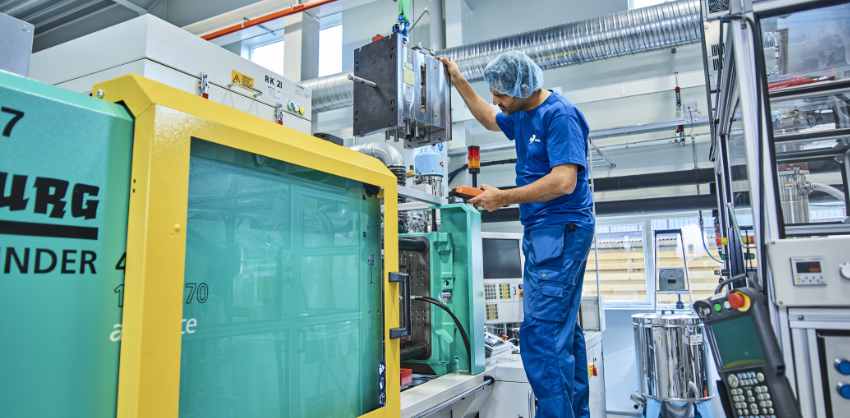
28 percent carbon reduction on signature product
In addition to reporting the final environmental footprint of a product, the calculator also plays a decisive role in developing products with the customers.
“With the new tool, we can make qualified design and improvement proposals based on data, because we can simulate design changes with the help of our carbon footprint calculator”, says Anders Johnsen. He adds:
“This gives us optimal conditions for developing the exact solutions our customer needs. We also use it to document the effects of redesign and changes in the production of existing products.”
As an example, Anders Johnsen highlights Carmo’s signature product, SuperValve, a unique turn valve for urine bags. Based on user feedback, Anders and his team improved the original design and production method of the valve to better suit the customers’ needs. The redesign also achieved a 28 percent carbon reduction compared to a traditionally produced valve. This corresponds to 13.3 kilos less carbon emissions for every 1,000 valves produced. This has been documented through carbon calculations from Viegand Maagøe.
“The valve now opens to 180 degrees instead of the original 90 degrees. This makes the product more user-friendly and takes up less space in both the open and closed state. The carbon reduction has been achieved through streamlining production, where the valve is produced in one piece on a single machine and with less material than in a traditionally manufactured turn valve”, says Anders Johnsen.
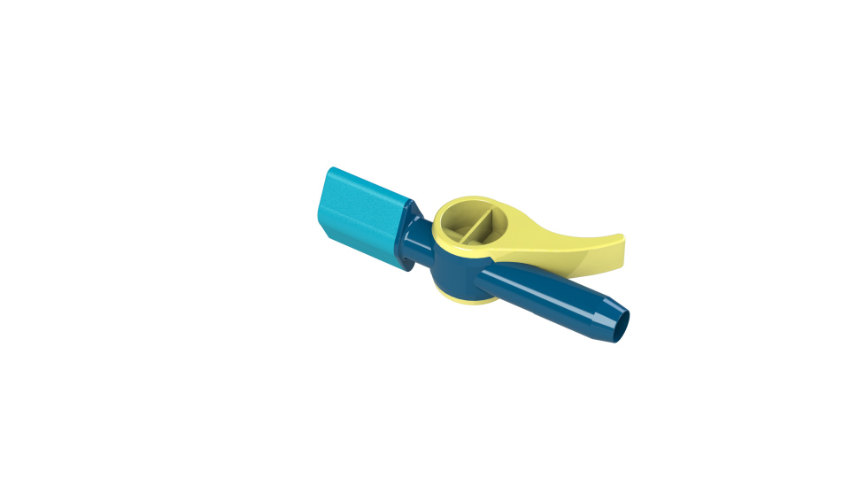
Carmo brings SuperValve to the Compamed fair
When Carmo on the 13th-16th November is exhibiting at the leading trade fair for suppliers of components to the medical industry, Compamed in Düsseldorf, the calculation tool and SuperValve will be the stars of the show. Participants can experience the redesign of the popular valve and can talk to Carmo’s experts about the new ESG initiatives and EU directives.
Carmo exhibits at the Pavilion of Denmark, which is Danish Export’s joint stand. You will find the Pavilion of Denmark in hall 8B, stand no. E20.
Attendees at the fair:
- Ole Schak Nielsen, VP, Sales & Marketing
- Anders Johnsen, Head of R&D and Technology
- Malene Warhøi-Rasmussen, Key Account Manager for Medical Components
- Dennis Petersen, Senior Project Manager