Dencam Composite A/S selected three ELGi EG Series compressors (EG55V, EG22V, and an EG15V) to support precision milling of composites, plugs, moulds, and models across three production locations in Denmark.
Dencam Composite has years of experience creating and producing composite tooling solutions across the wind, marine, and automobile industries. When selecting a compressed air partner, their key considerations were enhancing existing manufacturing processes and identifying a reliable, energy-efficient compressed air solution to power their high-precision 5-axis milling machines.
Dencam reached out to ELGi’s compressed air channel partner in Denmark, ALT-Trykluft Aps., for an air audit, which highlighted energy improvement possibilities by simulating the efficiency of three ELGi EG Series variable speed oil-lubricated screw air compressor units.
“Optimal operating cost, energy efficiency, and innovation are the focus areas for our business. High-quality air compressors enable us to achieve this”, said Jens D. Andersen, CEO at Dencam Composite. “Especially vital is energy efficient compressed air, as we produce moulds used to create wind turbines’ rather large blades. We are very mindful of the importance of energy as we work on creating renewable energy solutions for the future.”
“At ELGi, we understand the importance of energy efficiency for our customers, and the in-built ELGi VFD (Variable Frequency Drive) matches compressor output with demand by varying the motor speed. This reduces the power consumption in line with the demand reduction. Compared to a compressor without a VFD, an EG Series with variable speed over a ten-year operating period can have a 34 percent reduction in energy costs,” said Tord Sandberg, Regional Manager Nordics at ELGi.
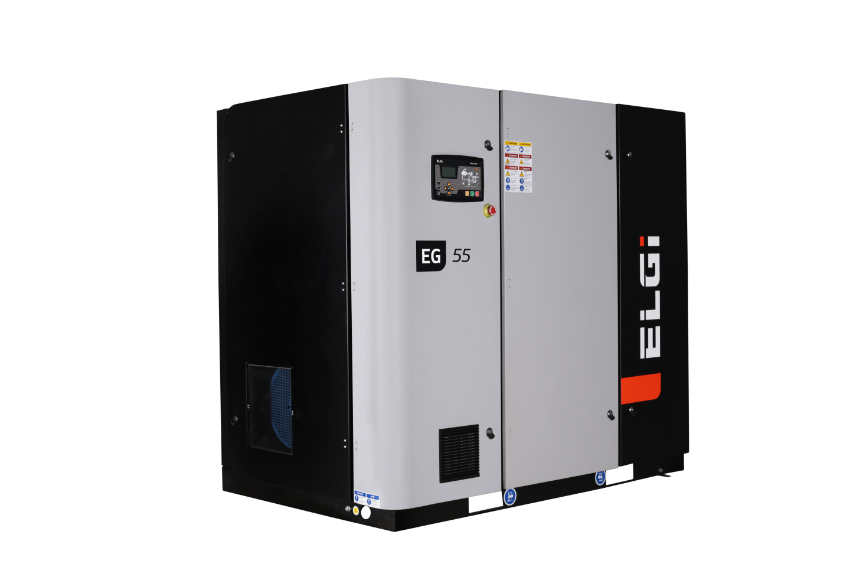
“Furthermore, the EG Series chosen by Dencam Composite comes with the best-in-class warranty package: a 10-year warranty on ELGi’s airend, five years on major compressor components, three years on the VFD, and one year on electrical and rubber parts – further contributing to making this arguably the compressor with one of the lowest life cycle costs in its range on the market today.”
The sturdy design of the EG Series compressor range enables operations at extreme temperatures – from cold to hot and from dry to extremely humid conditions – leading to improved compressed air system reliability. ELGi’s high-efficiency airends are equipped with in-house developed η-V profile rotors, with the 4/5 lobe combination, designed to run at low rotor speeds. This unique design reduces pressure losses, and together with the OSBIC (Oil separation by impact and centrifugal action), 3-stage separation provides best-in-class energy efficiency.