How the Industrial Internet of Things transforms manufacturing
The Internet of Things (IoT) is developing a strong hold over our everyday lives, whether it’s a “smart” home, an intelligent assistant built into a smartphone or online shopping. The number of connected devices is increasing year on year, along with the IoT application domains. Prospective use cases allow managers to make optimal business decisions swiftly, reduce production costs, increase labor productivity, leading to improved businesses’ competitiveness on the market. According to the consulting company Accenture, the contribution of the Industrial Internet of Things (IIoT) to the global economy may reach $ 14.2 trillion by 2030.
IIoT: a brief timeline
The term “Internet of Things” was coined in 1999 by entrepreneur Kevin Ashton, a researcher in RFID technologies, but the concept of IoT itself dates back to the creation of electrical telegraphs (at the end of the 19th century). The first smart device was a Coca-Cola machine at Carnegie Mellon University. In 1982, students received up-to-date information about the product range via the ARPANET.
According to Cisco IBSG’s research, the Internet of Things emerged at a time when the number of connected devices exceeded the number of people on Earth (between 2008 and 2009). Since then, IoT has been permeating all areas of business, including industry, and became known under the name Industrial Internet of Things (IIoT).
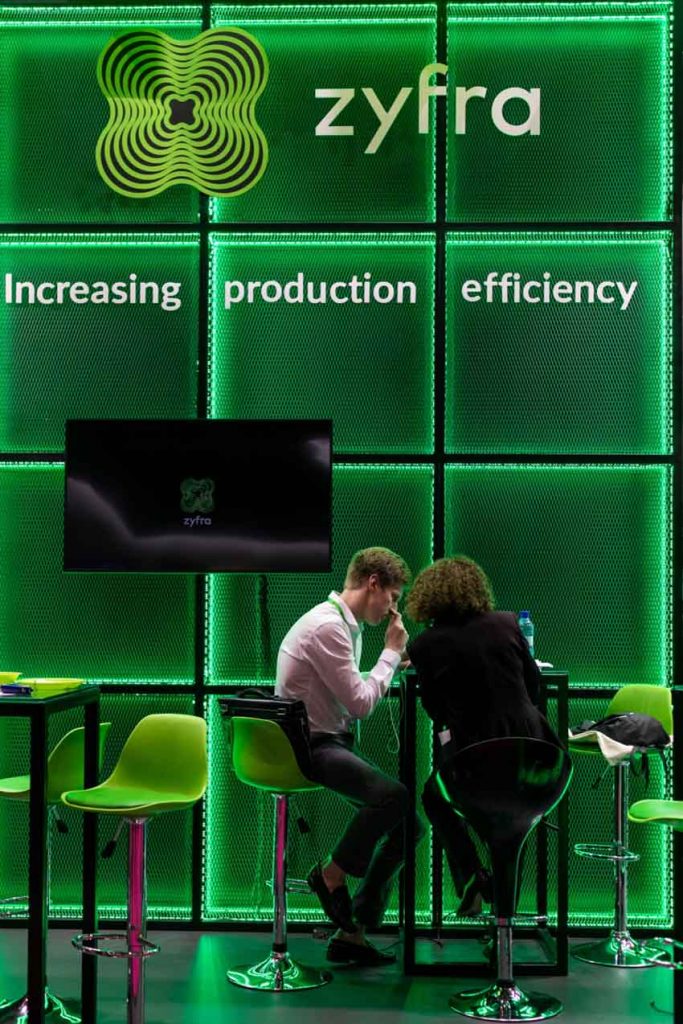
Revolutionary technology in the industry
The US and Europe recognize the advantages of innovative technologies, which is why they are striving to automate production processes as far as possible. According to a forecast made by Bain & Company, the volume of the global Industrial Internet of Things market will reach $ 200 billion by 2021.
Implementing a system to monitor personnel and industrial equipment increases productivity by on average of 20%. The operating principle of the equipment monitoring system is that each machine automatically transfers data about its performance to a unified system. Data on the equipment’s condition and workload, as well as on its operating mode, makes it possible to promptly eliminate downtime and provide an objective evaluation of the machine operators’ work.
The level of digitalization of industrial enterprises directly linked to how mature the technology is and the extent of its adoption. At the moment, many are merely keeping a close eye on the existing cases, but successful implementation of innovative solutions by some of the large companies will be followed by mass use. Today, digital transformation is being launched at cutting-edge factories and large holding companies. But it’s safe to say that once the innovative technologies are successfully tested by the “industry leaders” and – most importantly – receive positive outcomes, high-tech equipment will be rolled out across the entire group of companies and the use of AI will become a ubiquitous standard.
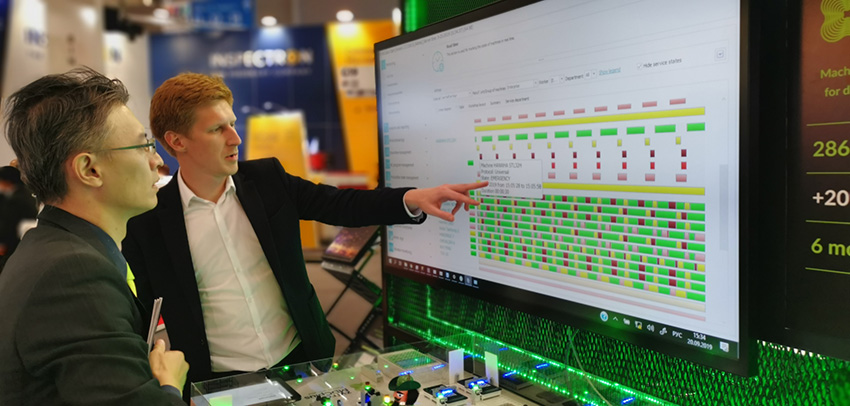
Why are businesses hesitant about modernizing production?
Digital technologies at industrial cities are being implemented in a fragmented way. Many executives are reluctant to invest in modernization as they understand that it will lead to additional expenditure, especially ensuring the cybersecurity of industrial systems (IS). In 2019, 80% of businesses in Russia stated that this was their priority, yet only 31% of them had implemented an incident response process. It’s not just hacker attacks that pose a threat but the unintentional actions of employees, too. This is due to the low awareness of new digital systems. 48% of firms surveyed view this as a problem and are willing to invest in personnel training.
A prerequisite for implementing AI is the availability of data. Some organizations form a business hypothesis and then start collecting data to support it. Others accumulate all the data in the hope that they will be able to single out the relevant information when necessary. For an IT company planning to carry out a digital “upgrade”, this option is preferable, although both methods are valid. The most important thing is for data to be high quality and directly relate to the task at hand.
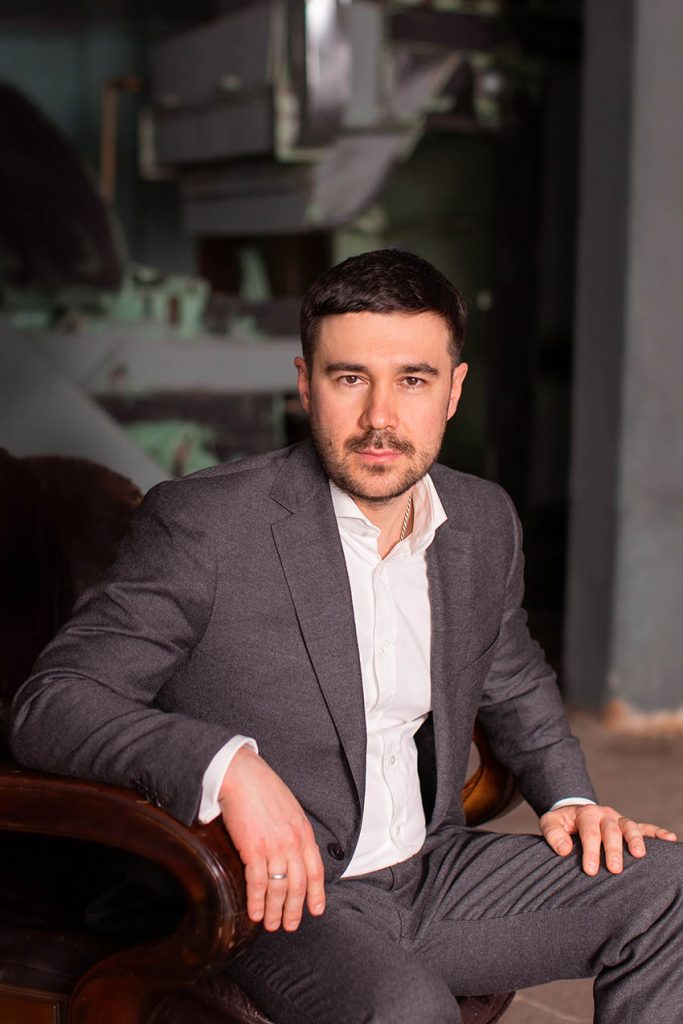
A competent approach to the digital transformation
The approach of managers to business “digitization” is of great importance. They must clearly define what the priority goal will be, such as optimizing the company’s budget or solving a specific problem. It must be understood that digitalization is not a cheap process. Ideally, it should pay off in a year. This is where a thorough analysis of the production efficiency comes to the fore. Other significant reasons are equipment monitoring and staff operations, controlling production processes, and increasing the quantity and quality of products.
When implementing digital transformation, one must follow the “simple-to-complex” principle: if it’s possible to increase productivity by 30% with one management decision, this should be done first. It’s important that front-line employees also see tangible benefits in this process and have a stake in the transformation. That’s why one of the key areas of work for the implementation of Industry 4.0 technologies should be to raise awareness among staff about what is on the market today.
Determining the area which should be improved as a matter of priority is a laborious and lengthy process. To do so, a method of assessing the effectiveness of the production process must be used. The first stage is to collect the necessary data. Complicated cases require additional equipment to be connected to the monitoring system. Analytical work comes next: determining the load influencers, equipment availability and the power consumption efficiency, etc. The result of the comprehensive analysis should provide an answer to the following question: where is the biggest bottleneck?
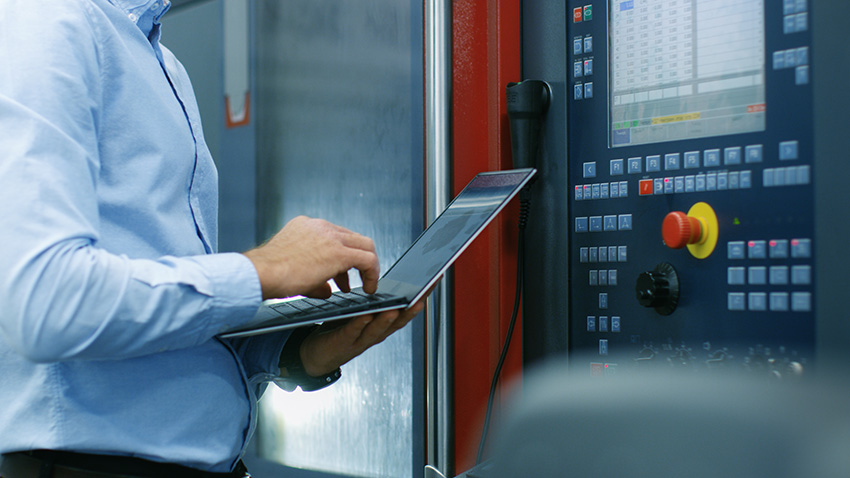
Features of IIoT solution implementation
The technological “upgrade” of businesses is a multi-stage process whose order can be changed. In our opinion, to achieve positive results, it’s better to start “digitizing” the production in the following order:
- Organize remote equipment monitoring and digital workplaces to identify production bottlenecks;
- Implement integration with ERP, MES, and PDM systems in operation;
- Organize the production process and ensure it’s monitored;
- In order to minimize the number of defects, start monitoring production process parameters;
- The next step is to ensure that electricity and energy efficiency is monitored;
- Proceed to monitor the use of metal-cutting tools and equipment;
- Organize predictive maintenance and equipment repair via advance data analysis.
It’s important that a company’s management clearly defines the end goal of implementing the technology. For example, to increase the quantity and quality of products, to ensure condition monitoring of the compliance with the production process, or to optimize the company’s budget. It’s not trends that should come to the fore but the needs of the business. The correct approach to modernization is key to quick results and an effective solution to the tasks at hand.