Civan Lasers, founded in 2008 in Jerusalem, is a manufacturer of industrial fiber lasers with dynamic beam profiling. Civan’s technologies, Coherent Beam Combining (CBC) and Optical Phase Array (OPA) have revolutionized industrial applications. With a team of 165 employees and a portfolio of over 75 patents, Civan opens up new frontiers in laser welding, Metal AM & Free Space Optical Communication. Their range includes Single Mode (SM) lasers, delivering power outputs from a few watts to over 100 kW, seamlessly integrated into material processing systems.
The company operates from a facility in Jerusalem, housing advanced labs and manufacturing infrastructure. Civan’s Dynamic Beam Laser offers unique possibilities, enabling manufacturers to produce new products more affordably, efficiently, and with reduced CO2 emissions compared to other solutions. These welding capabilities find applications in various industries, including the production of electric vehicles, ships, and wind towers. By utilizing Civan lasers, manufacturers in these sectors can achieve enhanced welding precision and quality while contributing to a greener and sustainable future.
Interview with Ami Spira, VP Marketing at Civan Lasers.
Easy Engineering: What are newest products in your range?
Ami Spira: The 100kW Dynamic Beam Laser is the latest product on the market. In addition to its extremely high power, this laser is equipped with dynamic beam capabilities that allow it to generate any arbitrary beam profile, move the beam in any arbitrary pattern, switch between beam shapes in microseconds, and steer the focus with a frequency of up to 40MHz. This product is designed to weld thick metals of 25mm to 100mm thick.
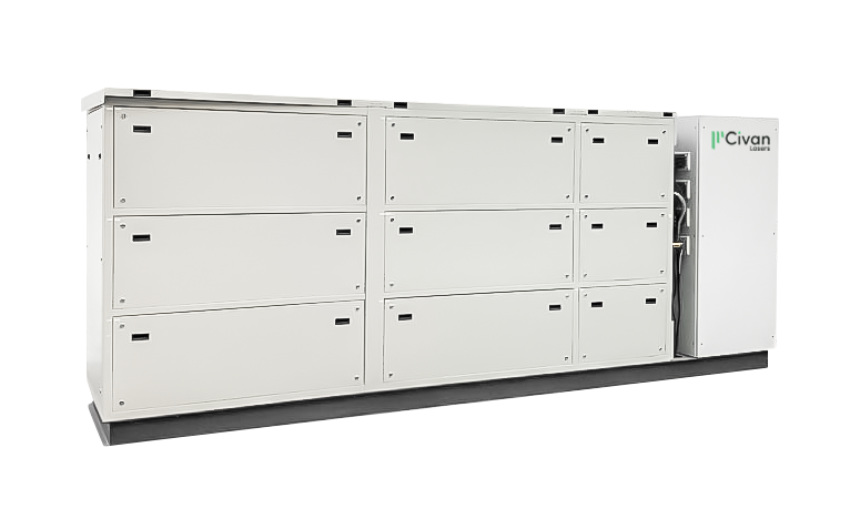
E.E: Which are the most innovative / trending products and what special features do they have?
A.S: The dynamic beam capability which is in all our lasers from 7-100kW power levels are the main revolution that allows to achieve sophisticated welds that are not possible with any other lasers. The beam shaping capabilities are all controlled by a simple software which allows any user to easily design and use different beam shapes.
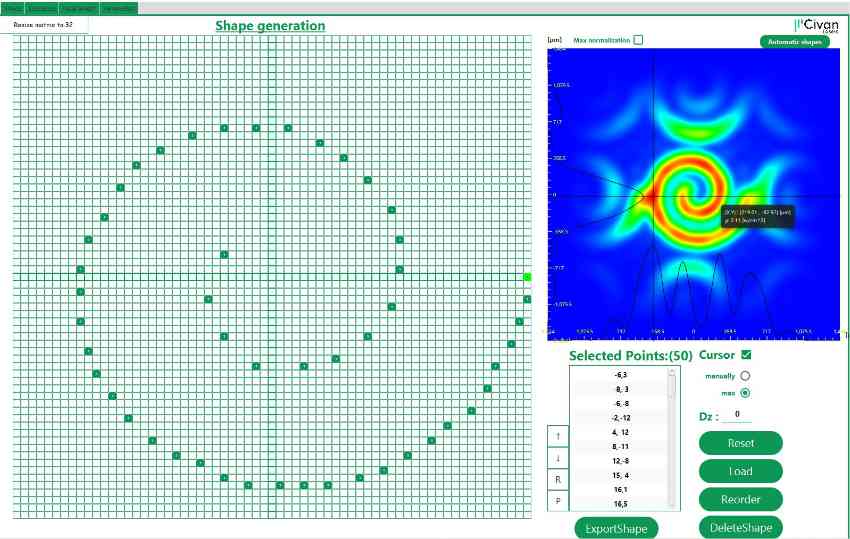
E.E: How important are these features for the users in their work?
A.S: The ability to prevent cracking and spattering, ensure a defect-free weld, and obtain desired weld geometries is invaluable for industries demanding precision and durability. It not only ensures the quality and longevity of the final product but also reduces production time and costs.
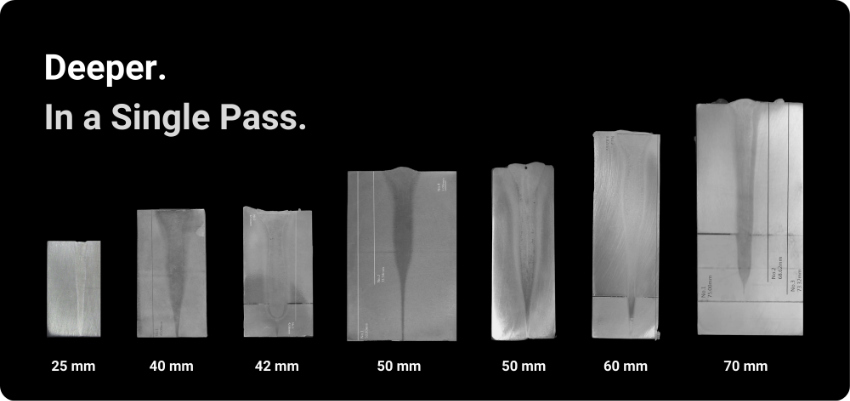
E.E: How do your new products / services differ from others on the market?
A.S: While traditional welding techniques might demand multiple passes, complex setups, or concede to material limitations, our Dynamic Beam Lasers present solutions that streamline the process, ensuring efficiency without compromising on quality.
E.E: Tell us about research and development in your company.
A.S: Currently, our R&D team is focusing on two main areas. The first is to improve laser reliability and performance by continuously improving components and reducing laser size, volume, and weight. Additionally, they are developing new products with higher power levels.
E.E: What impact has product innovation on your customers?
A.S: Our innovations in Dynamic Beam Lasers have revolutionized traditional welding processes, reduced costs and improving product quality. There are several case studies that emphasize this. A first example is the welding of thick metals. It can take 250 minutes for a 7m long panel to be welded with existing methods, when we can reduce the time to only 3 minutes using our method.
In the automotive industry, we have a case study of welding battery cooling plates, where vacuum brazing is commonly used, which is a large machine that takes up a large area in the production hall, requires continuous operation with high power consumption, and is limited in the alloys it can join. By replacing vacuum brazing with laser welding, Dynamic Beam Laser customers can achieve high joint quality in a more efficient way.
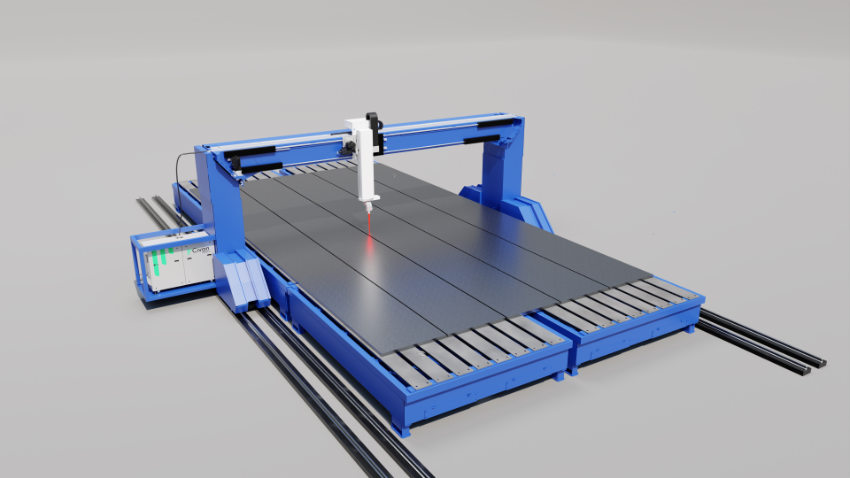
E.E: What new products / solutions are you going to launch in the future?
A.S: At this stage, we are focusing on developing welding processes for as many applications as possible. We are currently limited in the number of welding processes we can develop, since each process requires time to fully qualify. The more welding processes we develop, the more industries can use our lasers. Currently, we are encouraging our customers to work with research centers that have our laser to help them develop their processes.
E.E: What industries do you think will grow in 2024?
A.S: There are two main industries that we see potential in. The first is E-mobility, which is a growing market that still needs welding solutions for many applications. Despite the fact that many applications are working, they still have a limited process window, which is a challenge for production. Dynamic Beam Lasers offer a larger process window and can improve speed and quality, which is why we see potential in this market.
Secondly, offshore wind towers are an important industry. The Multi-Pass Welding process takes a long time, but Dynamic Beam Lasers can help them reduce the welding time and increase productivity.
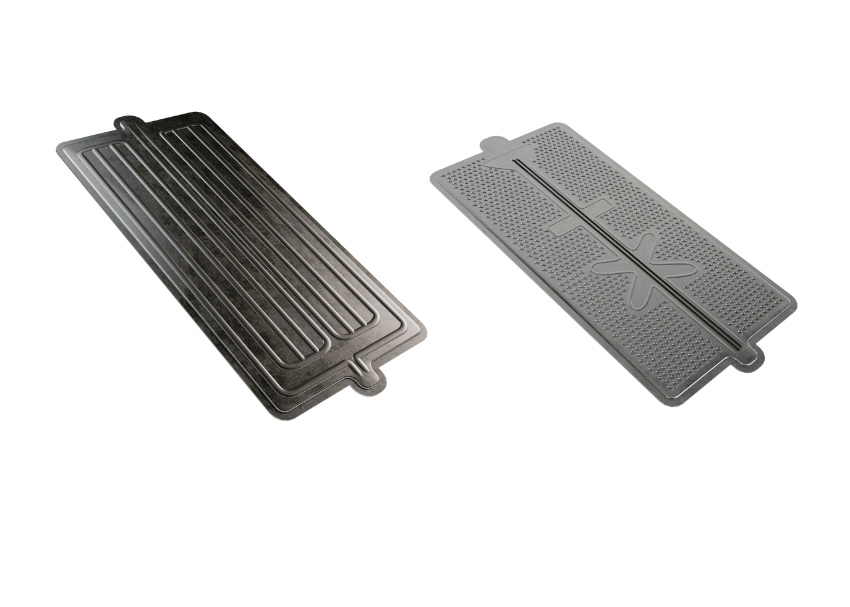
E.E: What products/solutions do you provide for these industries?
A.S: For the E-mobility industry we offer welding processes for aluminum alloys which are used in various components as well as welding dissimilar materials which are common in the battery production and we’ve seen new results on welding hair pins, which is an important topic nowadays. We also provide a solution for welding Die Cast material which is a big revolution since it opens possibilities to use this material for many more products.
In the heavy industry, we offer shipyards a process for welding ship panels in a single pass. For thicker materials such as for manufacturers of wind tower, we offer welding of thicker materials of 10’s of mm in a single pass, which reduces the welding time significantly.