PMM – Projects Moulds and Manufacture is a company specialized in the study, technical development and manufacture of molds with high technical requirements for the injection of plastic, rubber and die-casting. Currently, they cover the whole value chain, from product design and engineering to serial production of parts.
Founded in 1987 as a project development office, its vast technical competence and working values contributed to the company growth, having the trust of some customers for over 30 years.
This experience also made it possible to increase the range of services provided, with PMM currently being a One-Stop Shop, which allows the reduction of costs and risk by reducing the number of intervenient in each project.
In addition to adopting the latest technologies to increase its competitiveness, PMM was also a pioneer in reducing its carbon footprint through the installation of photovoltaic panels back in 2013. Thus, together with customers and partners, the company will continue to walk towards a more digital, green and sustainable future.
Easy Engineering: What are the main areas of activity of the company?
PMM: PMM core business has always been the design and manufacture of high precision moulds. Our main market is the automotive, particularly in Germany and USA. However, with more than 2130 moulds produced throughout our 34 years of activity, PMM has extensive experience in other markets as well, such as Medical, Electronics, Gardening, Packaging and Houseware.

E.E: What’s the news about new products?
PMM: In 2020 we have doubled our production area to 4000m2. This expansion allowed us to increase our injection machines in number, size, and capabilities – from 50T up to 500T, 2K+ aggregate. We also assemble parts, which is a service some clients were asking us to provide for some time. With this, we simplify the supply chain and reduce risks and costs.
E.E: What are the ranges of products?
PMM: We provide all the services necessary for any injection mould project. Starting with Product Development, where we collaborate closely with our clients to iterate the product design for manufacturing, then CAE analysis, which allow us to find the optimal position for injection points to prevent injection defects. Then, Tool Design, where we create simple but efficient mechanics, allowing us to minimize injection cycle times and maintenance, contributing to a profitable tool that lasts longer. After sign-off, we move to Tool Manufacturing with our 8 5-axis CNCs, EDM, Wire EDM, Robot Cell for electrodes, grinding and spotting machines. Because we value transparency with our clients, we use a GOM inspection machine to measure plastic and steel parts. Finally, we make tryouts in our injection machines to find the right injection parameters and if necessary, make serial productions and assemble the parts.
E.E: At what stage is the market where you are currently active?
PMM: The market has changed in the last couple of years, due to the Covid-19 pandemic. Supply chains were affected everywhere and there was a shortage of components that impacted the automotive market, and indirectly, PMM, forcing us to diversify our client portfolio. Prices in raw materials have also increased, further increasing pressure in prices.
E.E: What can you tell us about market trends?
PMM: Due to the high prices in fuel and environmental concerns, in the last years the sales of EVs have grown rapidly, and we can surely expect a rise on their market share throughout the next decades. In the below chart, you can observe the share of sales of Plug-in Electric Vehicles in some countries and California in these last 5 years.
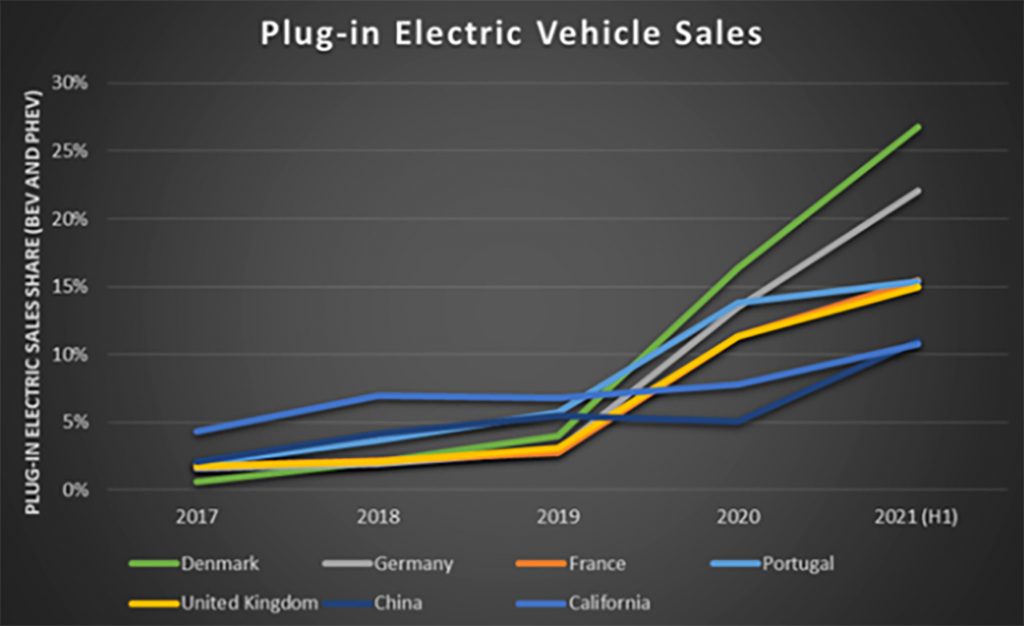
At the World Climate Conference in Glasgow, 30 countries, 11 carmakers and other partners issued a joint declaration to end the production of cars with internal combustion engines in order to produce exclusively emission-free passenger and light commercial vehicles until 2040. Also, we can notice the trend of banning plastic products with single use purpose, like plastic forks, knifes, spoons, cups, plastic packaging and others.
E.E: What are the most innovative products marketed?
PMM: Electrochemical Polishing (ECP) is our most innovative and exclusive service. PMM is the only company in Europe that has the equipment and competencies to use this process in the mould industry.
With ECP, customers can expect the following advantages:
- Improved smoothness of surfaces, which reduces injection pressure, increases injection speed and uses smaller injection machines, which translates in cost savings.
- It reduces surface roughness up to 7 times and eliminates microcracks left by the EDM, increasing wear resistance and consequently, the lifetime of the part.
- Decreases likelihood of bacterial contamination for medical & food products.
- ECP allows the polishing of complex geometries, unreachable by manual means, such as deep ribs.
- Unlike conventional electropolishing, this process does not involve any dangerous chemicals.
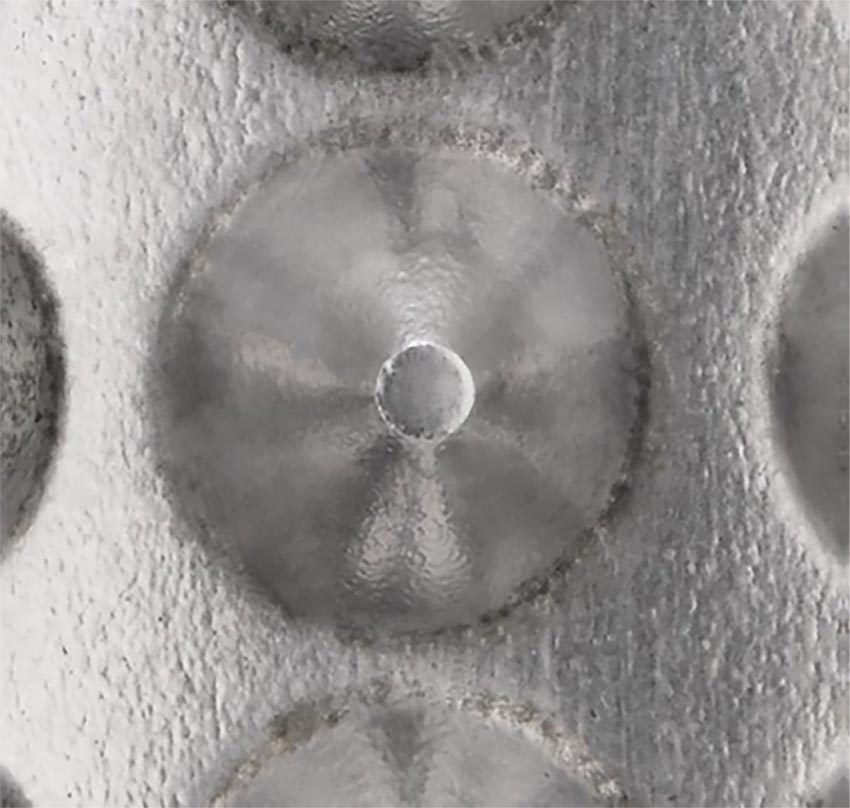
E.E: What estimations do you have for 2022?
PMM: Our outlook is optimistic. More and more companies are becoming aware of the risks associated with centralized manufacturing in Asia: high fuel prices, logistics and customs constraints and the long distance that complicates the attendance for the Project Managers. We are noticing a trend, where European companies are coming back to European suppliers. Although the Automotive Industry is having some difficulties due to the higher prices of raw material and shortage of semiconductors, PMM will continue to innovate and expand to new markets, such as medical and electronics.
Website – www.pmm-moldes.com
Phone – +351 244 545 790