Today’s conveyor belt market is dominated by low grade ‘economy’ belting imported from Southeast Asia. In fact, it is now common practice for some European belt manufacturers to supplement their own production by importing from Asia and re-selling under their own brand in order to compete at the low-price end of the belting market. The resultant decline in prices has been accompanied by an alarming decline in performance and longevity standards.
Despite this trend, one major European manufacturer, Dunlop Conveyor Belting in the Netherlands, part of the Fenner Dunlop Group, consistently refuse to follow this downward spiral. They insist on making every belt themselves and instead of competing on lowest selling price, their market strategy continues to be based on only supplying belts that provide the longest possible operational lifetime and therefore the lowest lifetime cost. However, although this strategy had always served them well, Dunlop also continue to pursue another integral part of their DNA makeup, which is the search for new, ground-breaking products.
Ambitions and objectives
For developmental work to be effective, it is important to have clear ambitions and objectives. Not having a destination in mind makes it impossible to even know what general direction to take. Fortunately, Dunlop’s research & development teams on both sides of the Atlantic benefitted from having a very clear shopping list – superior durability, greater affordability and reduced environmental impact. The primary objective was to design a belt that had a much higher resistance to impact, ripping and tearing. The reason for this is that an estimated 75% of industrial conveyor belts have to be replaced prematurely as a result of damage.
To many, catastrophic damage is wrongly considered to be inevitable. As a consequence, growing numbers have fallen into the trap of using low price imported ‘sacrificial’ belts. Ironically, the lower the quality of belt then the lower the ability of that belt to resist damage, resulting in an even faster, more expensive cycle of fitting and replacing.
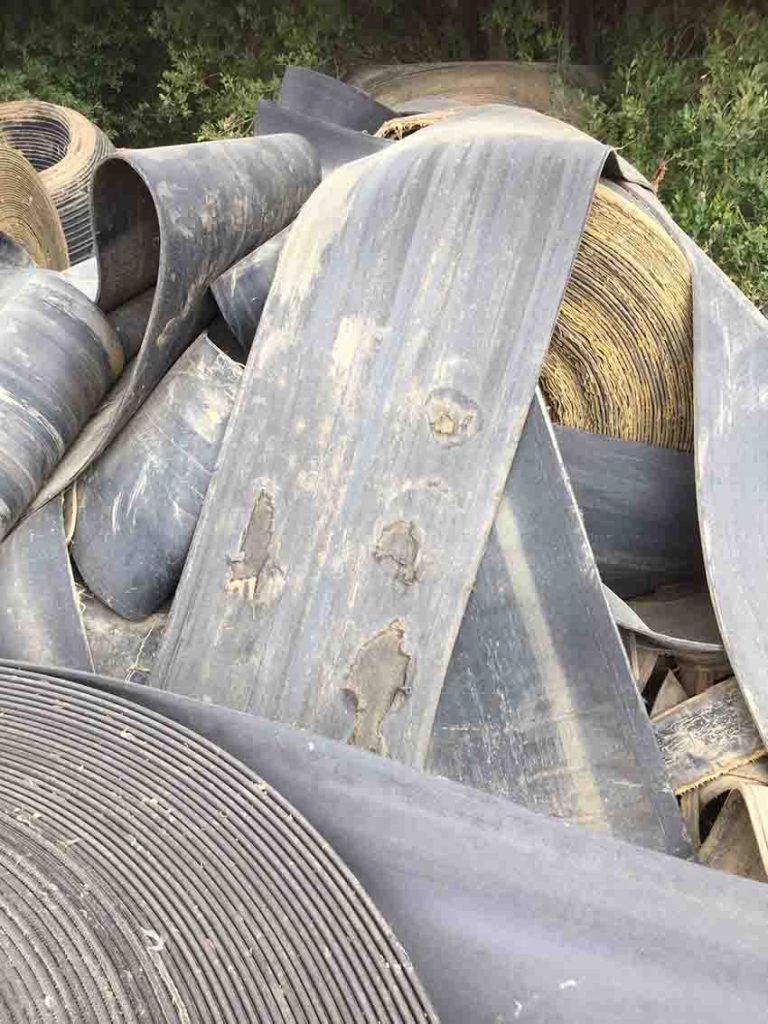
The ultimate goal for the Dunlop engineers was therefore to develop a super-tough belt which at the same time was also much more affordable. Directly related to the issue of affordability was production efficiency, both in terms of speed and energy as well as the volume of raw materials contained in each belt. In order to meet this impossible sounding challenge they decided to forget convention and harness advances in science and technology that were now available to them. The result was the creation of a new and unique super-strength single-ply belt that in Europe they named Ultra X.
Home advantage
The basic construction of rubber conveyor belts has not changed fundamentally for many decades. By far the most common construction consists of multiple layers of synthetic fabric ply material with a thin layer of rubber in between each layer known as the carcass. The carcass is protected by an outer layer of rubber. Although the quality and durability of the outer rubber is very important, on applications where ripping and tearing and impact is a problem the solution invariably lies in the construction of the carcass. Dunlop had already developed extremely hard-wearing rubber compounds, which meant that their engineers and technicians could focus purely on the design of the carcass.
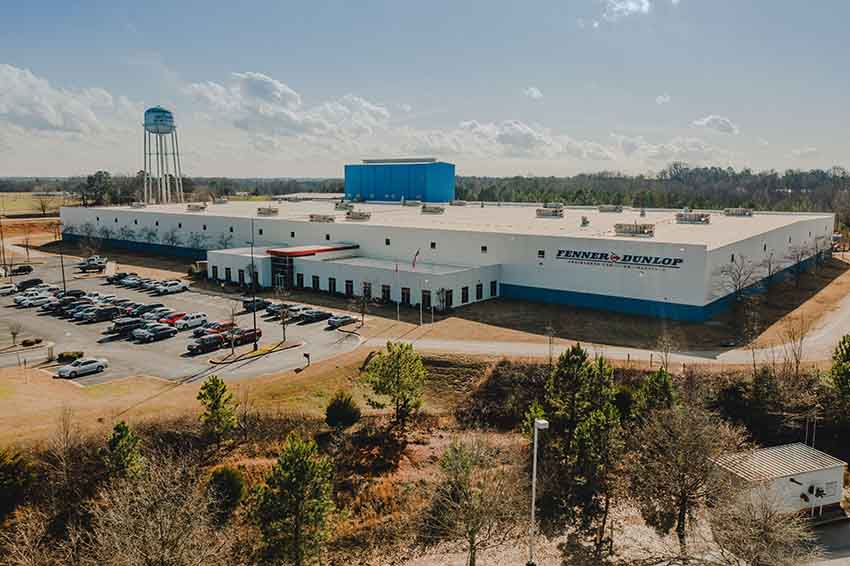
The big advantage that the Dunlop engineers had was having an in-house fabric weaving facility located in the USA where new thinking could be explored. It was thanks to their creation of an amazingly tough patented woven fabric that enabled the engineers to design a unique, super-strength ‘breaker weft construction’ single-ply belt.
How it works
The specially woven fabric uses crimped warp polyester yarns to provide high strength and low stretch. These were combined with very strong ‘binder’ and ‘filler’ yarns to create a super-strength ‘breaker weft construction’ that could be used to produce a single-ply belt carcass with exceptional strength and stability under load characteristics.

Throughout its development, sections of belt carcass were repeatedly tested to destruction, including measuring the tear resistance according to the international EN ISO 505 standard. The tests revealed that the (Ultra X) fabric possessed more than 3 timesgreater longitudinal rip resistance, up to 5 times better tear resistance and a far superior resistance to impact compared to traditional 3-ply or even 4-ply belting. There was also no question about the overall strength. For example, the Ultra X3 single ply belt proved capable of pulling up to 56 tonnes in weight.
A question of strength
The fact that Ultra X is a single-ply construction designed to replace conventional two, three and four-ply belts did raise a few eyebrows at first. The first question seemed to be how a single-ply belt could provide sufficient tensile strength and yet still have such high levels of rip, tear and impact resistance? According to Dr. Michiel Eijpe, Dunlop’s Innovation & Sustainability Director, the answer lies with the special fabric plus the advantages of finger splices.

“We stepped away from the conventional multi-layer belting for a number of reasons. First and foremost, the unique fabric created by our colleagues in the USA is able to withstand the kind of punishment that would destroy a normal belt. Ultra X also has amazing tensile strength. For example, the longitudinal tensile strength of the X1 is 330N/mm and the X3 has a longitudinal strength of 550N/mm. A single-ply construction requires a finger-splice joint to be made and the enormous advantage of finger splice joints is that they retain up to 90% of the belt’s tensile strength. By comparison, a 2-ply step splice only retains a maximum of 50% of a belt’s tensile strength and a 3-ply step joint only retains a maximum of 67%”.

The higher level of splice efficiency combined with the tensile strength effectively creates equivalent tensile strengths and belt safety factors that are more than comparable to 3 or 4 layer conventional belting. Dr. Eijpe freely admits that finger splices do concern those who have little experience of making them but the technical and economic arguments in favour of finger splicing are unquestionable. “Finger splice joints are stronger and more durable so the need to repair and re-splice joints is almost non-existent in comparison to step splices”.
Numerous advantages
The advantages of the single-ply construction are extremely wide ranging. Using a single, albeit much stronger, layer of fabric means that the belt is flexible enough to be used on smaller drive pulley diameters if required, “The X1 drive pulley diameter for over 60% rated tension can be as small as 315mm and the X3 drive pulley diameter, again for over 60% rated tension, can be as small as 400mm” explains Dunlop’s application engineering manager, Rob van Oijen. “Ultra X can run on the kind of mobile machinery that has always been notorious for having small pulley diameters where the dynamic stress placed on the inner carcass and splice joint by the continual flexing over the small diameter pulleys seriously limits what can be fitted. Ultra X overcomes that problem”.

Since the introduction of Ultra X to the market some three years ago, some unexpected advantages have also emerged. One UK quarry, for example, found that the multi-ply belts used previously made the head drum squeal constantly and the rollers emit a constant, loud rumble. Located on the border of a wildlife sanctuary, it was therefore a very welcome surprise when the first Ultra X conveyor belts were fitted because the squealing stopped completely and the whole noise level of the conveyor dropped by at least 50%. The quarry also discovered that with Ultra X they only needed a single 37kw drum instead of the double drum drives they had to use with conventional multi-ply belts.
Rob van Oijen was more than happy to explain the reasons for these improvements. “The biggest factor is actually the rubber because it is much higher quality compared to low grade ‘economy’ belting and contains much higher proportions of top-grade polymers and essential additives such as carbon black than you would normally find in economy products. Rather than being rigid, the rubber is highly elastic, which helps to reduce its rolling resistance. This means that it requires less drive power and makes less noise as it passes over the rollers”.
Affordability and environmental impact
Following closely behind superior durability on the original list of objectives given to the R & D team at Dunlop were affordability and greater sustainability. From the outset, Dunlop were very open about the need to be able to offer prices that were more affordable. “There are several reasons that allow us to price Ultra X competitively” explains sales and marketing director, Andries Smilda. “Firstly, the single-ply carcass is made from fabric that we manufacture in-house. That is a big, big advantage in terms of quality and cost. Having a single-ply construction also helps to maximise efficiency of production because there are fewer calender runs. And having no rubber skim between the plies not only results in a thinner, stronger carcass, it also keeps the cost down. We are also able to make longer production runs at a maximum width of 2000mm”.

Mr. Smilda was keen to explain why these factors also have a big bearing on environmental impact and sustainability. “For a start, more efficient production processes consume less energy. We also use less rubber, including a corresponding reduction in the amount of chemicals and additives used to create that rubber. There is also a dramatic reduction in the amount of nylon and polyester used in the creation of a single layer of fabric compared to the multiple layers found in a conventional multi-ply belt. This is particularly important because synthetic fabrics are not bio-degradable. Last but not least, the vastly superior toughness of Ultra X belts means that they have to be replaced far less frequently, which consequently means that far fewer conveyor belts have to be manufactured and shipped enormous distances in the first place”.
Tried and tested
Dunlop are the first to admit that when they first launched Ultra X they took a deliberately cautious approach. “We knew from the years of research and intensive laboratory testing that we were onto something special” explains Smilda. “But Dunlop being Dunlop, we still wanted to prove it in the field so we worked with several tried and trusted end-users”. “Three years on and having sold hundreds of thousands of meters has confirmed beyond doubt that Ultra X is all that we thought it would be and more. We have not had one single complaint or technical issue”.
A single-ply future
For some, the very idea that a single-ply construction belt can provide the necessary tensile strength as well as considerably more resistance to accidental damage compared to a belt with multiple plies is difficult to comprehend. However, the evidence is now overwhelming with Ultra X becoming the belt of choice in a rapidly growing number of operations across a wide cross-section of industry. Thanks to their belief in new technology and their commitment to develop increasingly stronger, more resilient products, Dunlop’s management certainly regard single-ply belts as being the way forward.
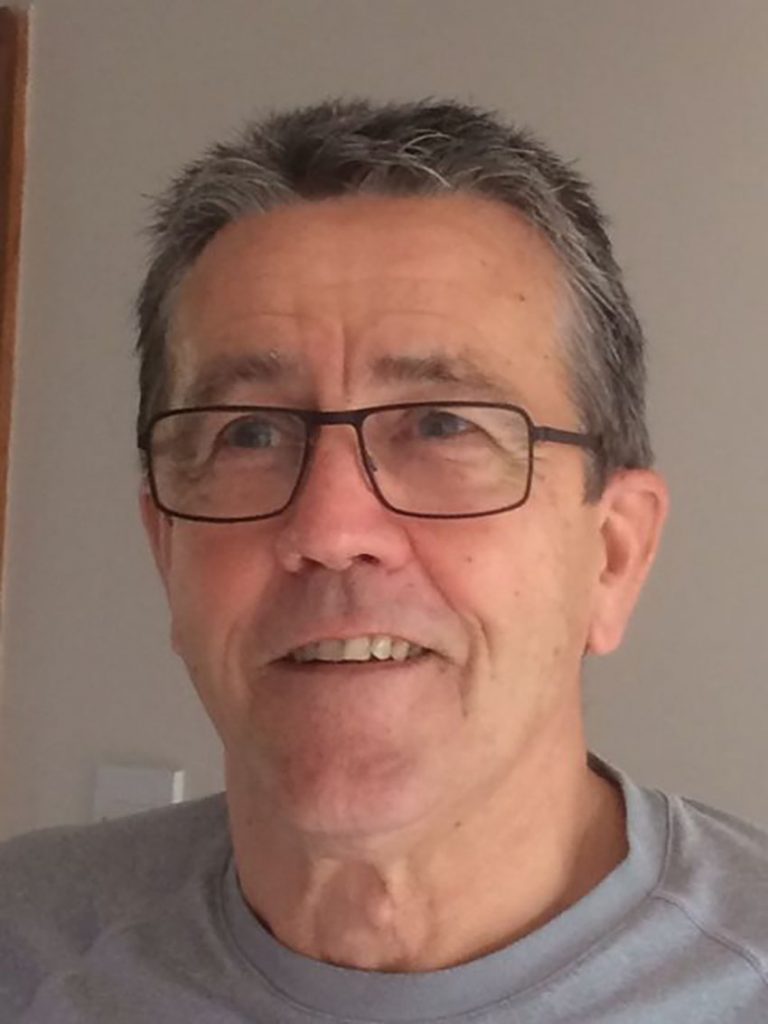
Leslie David
After spending 23 years in logistics management, Leslie David has specialised in conveyor belting for over 17 years. During that time, he has become one of the most published authors on conveyor belt technology in the world.