The future is circular
In today’s world where environmental awareness is more important than ever, manufacturers are adapting and embracing sustainable practices for the benefit of consumers and our planet. Huge shift has been made from linear to circular economy and EcoCortec has been one of the first packaging manufacturers to promote new green packaging technologies.
Packaging products that are designed to be used once and discarded are causing enormous amounts of waste material and pollution. Landfills have reached their capacity and micro-plastics are polluting almost every area of our planet. The change is needed more than ever and EcoCortec’s team of scientists and engineers have been working on designing and manufacturing environmentally friendly packaging solutions for over the last 15 years. Plant’s circular packaging solutions incorporate all the principles of the circular economy, in fact the company has been one of the first in Europe to implement a European-wide initiative to collect and recycle used VpCI® films and bags. Within the “Plastic Recycling Project,” EcoCortec’s customers send their waste material back to the Croatian plant, where it is then completely recycled and used for manufacturing a new product.
EcoCortec® reprocesses VpCI® film scrap and incorporates the “repro” back into the virgin film at up to 20 percent, a level at which Cortec® can ensure quality of the new product. EcoCortec® has expanded its film reprocessing program to allow customers to send their used VpCI® film back to the plant, creating a win-win-win situation for customers, the manufacturer and the environment. Instead of paying thousands of Euros for disposal, customers can send their used VpCI® bags and films to Croatian plant. Both customer and manufacturer demonstrate environmental responsibility and reduce their carbon footprint in the process.
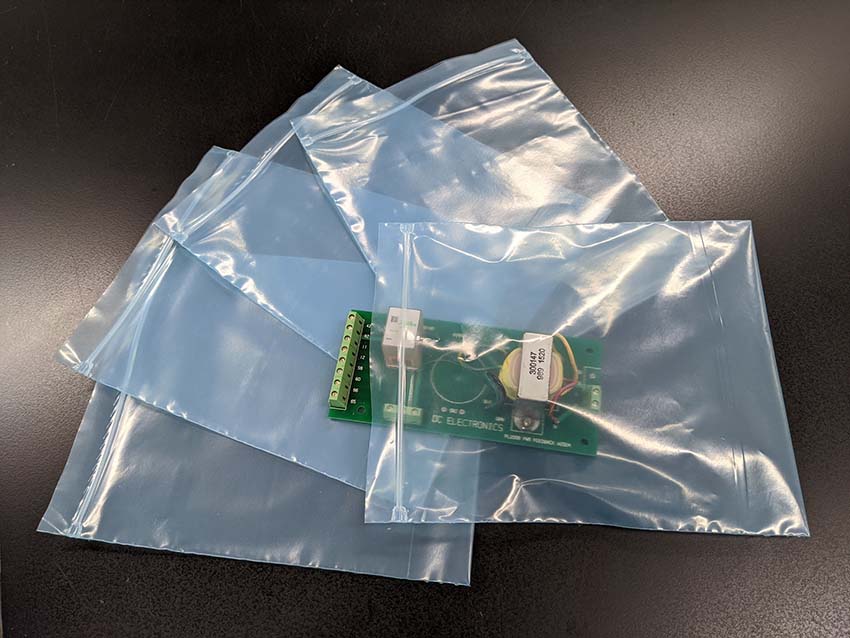
Environmentally friendly corrosion protection packaging
One of various recyclable films that is aimed for packaging od sensitive components is EcoSonic® VpCI®-125. These static dissipative film and bags are unique in their ability to prevent corrosion and ESD damage. The film combines the most effective multi-metal corrosion protection with strong static dissipative properties. They protect components from electrostatic discharge and conform to the surface resistivity and static decay requirements of MILPRF-81705 D (Static Dissipative Packaging Materials). EcoSonic® VpCI®-125 will not affect optical properties nor plastics used in electronic industry. The film does not contain any harmful Prop 65 ingredients and has been tested effective for up to 3 years of corrosion protection and 2 years of ESD protection.
The film is also available in EcoSonic® VpCI®-125 HP permanent version. These permanent ESD films and bags are high-performance, anti-static while they protect from corrosion static sensitive multi-metal items. Anti-static properties immediately reduce or eliminate static buildup as long as the films or bags are in use, independent of the presence of humidity.

Stretch hoods are among the fastest growing packaging techniques for shipment of palletized goods. EcoCortec recently rolled out new Cor-Pak® Stretch Hoods powered by Nano VpCI®, offering specifically designed plastomer material solutions for stretch hood packaging. Cor-Pak® Stretch Hoods powered are the ultimate high-performance stretch hood films for corrosion protection of ferrous and non-ferrous metals. The film is suitable for industrial use to stabilize loads and ensure pallet integrity for efficient packaging and delivery. It is co-extruded using state of-the-art resins, offering superior strength and stretch characteristics as well as multi-metal corrosion inhibiting properties that only VpCI® technology can deliver. Cor-Pak® Stretch Hood Film powered by Nano VpCI® delivers puncture resistance and load holding, which allows a user to down-gauge, contain aggressive loads and produce a better package at reduced cost. The combination of enhanced polyethylene resins with VpCI® Technology makes Cor-Pak® Stretch Hoods powered by Nano VpCI® the most advanced corrosion inhibiting stretch film available today on the market. The film can easily be recycled and is compatible with commercially available manual and automatic stretch wrapping equipment. Cor-Pak® Stretch Hoods meet German TL-8135-002 and NACE TM0208-2018 standards for corrosion protection. Cor-Pak® Stretch Hoods keep dust, dirt, and moisture off warehouse stock, satabilize pallet loads and enhance packaging integrity. They can be used in the fast-growing market for stretch hood film packaging techniques and allow industries to quickly and securely wrap and contain heavy loads while protecting metals. Cor-Pak® Stretch Hoods can be used for countless possible packaging applications such as appliances, automotive components, computers, construction materials, electrical/electronic cabinets, petrochemical drums foundries, industrial equipment, any metal items placed on pallets.

When looking for “greener” ways to approach packaging one need to look at the entire range of the product’s life cycle—from raw material sourcing to disposal. With this in mind, Cortec® Corporation, mother company of European plant, EcoCortec®, has been working tirelessly to introduce viable packaging options that can make the “circular economy” a reality. For more than two decades, Cortec® has been a leader in compostable films R&D and has recently intensified efforts to develop a variety of practical alternatives to traditional plastic films and bags. Recently, the company lauched EcoShrink™ Compostable Film, a commercially compostable alternative to common plastic shrink wraps for use in industrial packaging applications. Designed with the “Circular Economy” in mind EcoShrink™ takes both the beginning and the end of the shrink wrap product life cycle into account. It is sourced from certified commercially compostable resins and contains 45% biopolymers. After use, EcoShrink™ can be disposed of in a commercial composting environment to reduce the amount of plastic packaging that normally ends up in a landfill.

In addition to these “green” benefits, EcoShrink™ has many practical characteristics. It is designed for standard heat-shrinking applications. Users of EcoShrink™ can shrink wrap their small or large components as normal to conform to the shape of the object. EcoShrink™ is a great way to keep dust, dirt, and moisture off warehouse stock while keeping components bundled into a streamlined package. Shrink wrapping can be done with a wide variety of standard shrink tools. Simply measure the size of the unit, determine how much film is needed to wrap around it with enough for overlap, then shrink wrap as usual. There are many possible steps in the journey toward reducing plastic waste. By incorporating renewable materials, we are able to significantly keep reduce plastic waste and keep plastics out of the landfill by designing them for an industrial composting waste stream.