Nothing destroys a rubber conveyor belt faster than heat. Here, Rob van Oijen, application engineering manager for Netherlands-based Dunlop Conveyor Belting, explains the effects of high temperatures on rubber and why some heat resistant conveyor belts are able to provide a considerably longer working lifetime compared to others.
A destructive combination
High temperature materials and working environments create a combination of highly destructive forces on rubber conveyor belts. First and foremost, heat causes a rapid acceleration in the ageing process of the rubber, which causes it to harden and crack. High temperatures also have a seriously detrimental effect on the inner carcass of the belt because it damages the adhesion between the covers on the top and bottom of the carcass and between the inner plies contained within it. The result, known as ‘de-lamination’, is that the layers of the belt literally detach from one another.
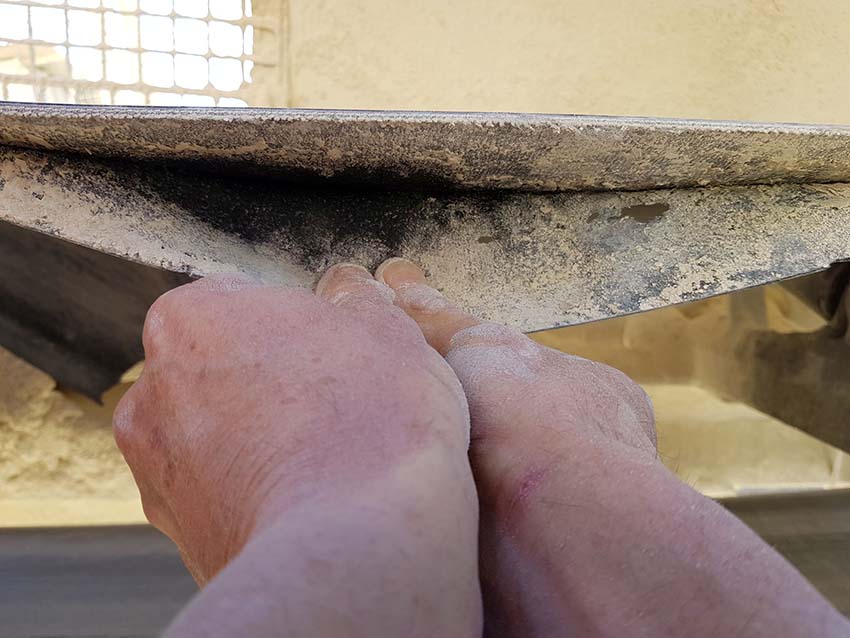
Delamination – the layers of the belt detach themselves
As rubber becomes harder and less elastic its tensile strength and elongation (stretch) can be reduced by as much as 80%. This effectively destroys the operational strength and flexibility of the belt including a serious weakening of the splice joints. At the same time, the surface covers of the belt begin to wear much faster than they would under normal circumstances because the resistance to abrasive wear diminishes by as much as 40% or more. In short, exposure to high temperature materials and working environments can shorten the life expectancy of a rubber conveyor belt like no other. A common misconception is that all heat resistant conveyor belts of a stated specification will provide a roughly similar performance and operational lifetime. In reality, nothing could be further from the truth.
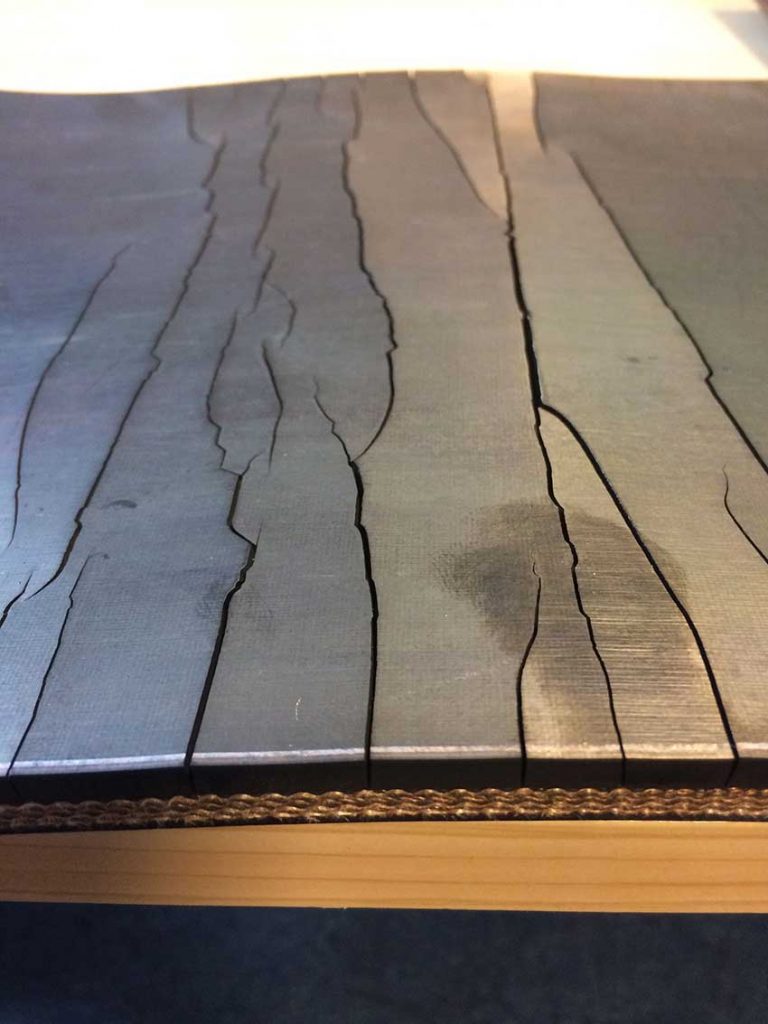
Cracking evidence – not all heat resistant belts perform the same
Heat resistance – definitions and classes
To many, the different definitions and classes or ‘grades’ of heat resistant conveyor belting must appear very confusing. So, before looking at the technicalities, it is perhaps a good idea to start with clarifying the terminology and meanings. The temperature limits that a belt can withstand are viewed in two ways – the maximum continuous temperature of the conveyed material and the maximum temporary peak temperature. Heat resistant grades are historically identified as grade ‘T’. The international ISO 4195 specifies the requirements for heat resistant belt covers, which spans classes 1, 2 and 3. The two identifications are commonly combined into classes T1, T2 and T3 respectively. Due to the typical material application areas of these classes, the market may also use T100, T150 and T200 instead. The two main classifications of heat resistance recognised in the market are T150, which relates to a maximum continuous temperature of 150°C and T200, which is for more extreme heat conditions up to 200°C.
The difference between what are considered to be continuous temperatures and peak temperatures is a critical issue and is the most common cause of failure and arguments over warranty. For example, although a belt classified as T150 should be able to consistently withstand material temperatures up to a maximum of 150°C over long periods, it can only be expected to cope with temperatures in excess of that limit for a very short period of time (literally minutes). The same principle applies to the T200 classification for temperatures higher than 200°C. Any period longer than just a few minutes will almost certainly cause irreparable damage to the belt.
WORD Of ADVICE: Even the very best heat resistant belt can be damaged beyond repair if it is allowed to stop when loaded with hot material, even for a relatively short period. Unless it is for emergency safety reasons, belts carrying hot materials should be allowed to fully discharge their load before being stopped.
Most manufacturers actually specify the range between continuous and temporary peak temperatures. For example, at Dunlop Conveyor Belting we produce Betahete ISO 4195 class T150, which is designed to handle materials at continuous temperatures up to 160°C and peak temperatures as high as 180°C. Our more extreme heat resistant belt, Dunlop Deltahete T200, has been engineered to withstand a maximum continuous temperature of the conveyed material as high as 200°C and extreme peak temperatures up to an incredible 400°C.
To give these temperatures some kind of real-world perspective, it is worth bearing in mind that the boiling point of water is 100°C. This means that T150 classification belts need to withstand temperatures some 50% higher and for T200 belts it is virtually double the boiling point of water!
WORD OF WARNING – Although the Centigrade temperature scale has long been regarded as the norm, some manufacturers are now using the Fahrenheit temperature scale in their marketing and product literature. It might look more impressive but it is simply marketing trickery. In my opinion, if a belt really does have good heat resistance then such practices should not be necessary.
ISO 4195 testing
The T150 and T200 classifications should not be confused with the requirements used within the ISO 4195 test methods that measure the heat resistance properties of rubber conveyor belts. The tests involve placing rubber samples in high temperature ovens for a period of 7 days. This testing procedure is known as ‘accelerated ageing’. At the end of the 7 days the reduction in mechanical properties such as tensile strength, elongation etc are then measured. There are three ‘classes’ of ageing within ISO 4195, each with a respective ‘ageing temperature’ – Class 1 (100°C), Class 2 (125°C) and Class 3 (150°C). At Dunlop, in order to maximize temperature resistance qualities for Class 3, we also carry out testing at a staggering 175°.
It’s all about the rubber
The heat resistant properties of the rubber need to perform a dual role. Firstly, it has to maintain its own integrity by not hardening, cracking or losing its tensile strength, elongation or wear resistance. At the same time, it must also be able to prevent as much heat as possible from penetrating the carcass. Protecting the carcass is vital because if the core temperature of the carcass becomes too high then the bond between the covers and fabric layers will separate (delaminate) and the belt will quite literally begin to fall apart.
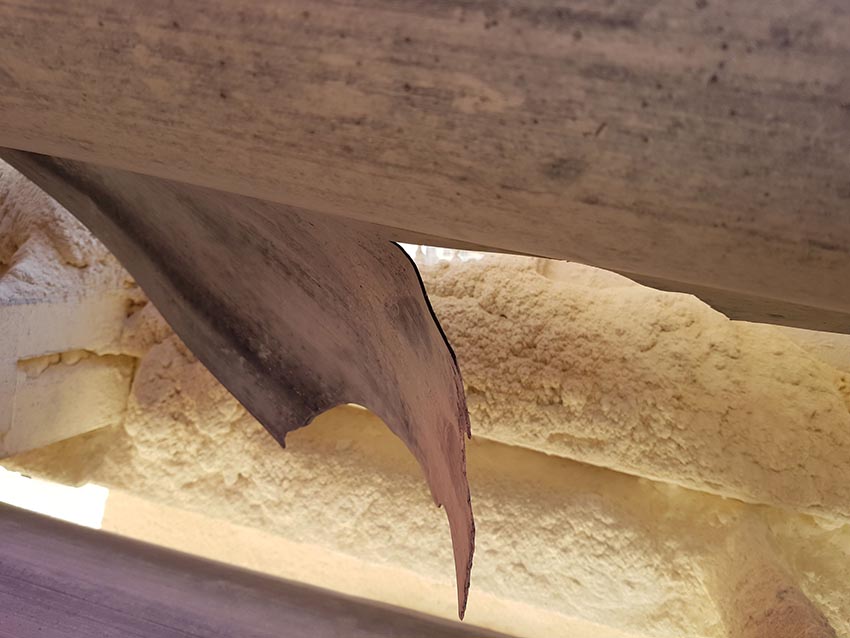
An increase as little as 10°C in core temperature can cause a belt to fall apart.
An increase as little as 10°C in core temperature can reduce the life of the belt by as much as 50%. This is because for every 10°C increase in temperature the rate of rubber oxidation increases by a factor of eight. The only way to limit the effects and slow down the degradation is to use rubber compounds that have been especially formulated to cope with the high temperatures that the belt is required to endure. The quality of the rubber always has the biggest bearing on the performance and cost-effectiveness of any conveyor belt but in the case of heat resistant belts, it has an even higher significance.
A complex cocktail
The vast majority of rubber used to make heat resistant conveyor belts is synthetic. This is because it is far more adaptable than natural rubber and can be more precisely engineered to cope with the many combinations of different physical demands placed on conveyor belts. Each different rubber compound consists of a complex ‘cocktail’ involving a huge range of different chemical components, polymers and other essential substances. In the case of heat resistance, the rubber not only needs to protect itself and the belt carcass, it also needs to have good wear resistance, tensile strength and durability.
Apart from thermal ageing caused by exposure to heat, the most common cause of rubber deterioration and degradation is oxidative ageing. It is a little known fact that oxidative ageing is primarily caused by exposure to ultra violet light (sunlight and fluorescent light) and other reactive gases, especially ground level ozone. All three factors cause rubber to become brittle and crack. The dynamic stress caused by the belt travelling around pulleys and drums under tension greatly accelerates the formation of the cracks. This means is that to be truly effective, heat resistant rubber must also be fully resistant to the effects of ozone and ultra violet light, which can only be achieved by the addition of UV stabilizers, anti-ozonates, and anti-oxidants. Sadly, laboratory testing consistently confirms that the use of these essential ingredients is an exception rather than the rule because of their cost. This brings me rather conveniently to one of the best indicators of a belt’s quality and suitability – the price!
Alarm bells
The rubber used for conveyor belts usually constitutes at least 70% of the material mass and is therefore the single biggest element of cost when manufacturing a conveyor belt. Consequently, for manufacturers who want to compete for business based on price rather than operational longevity, rubber is their biggest opportunity to minimise costs.
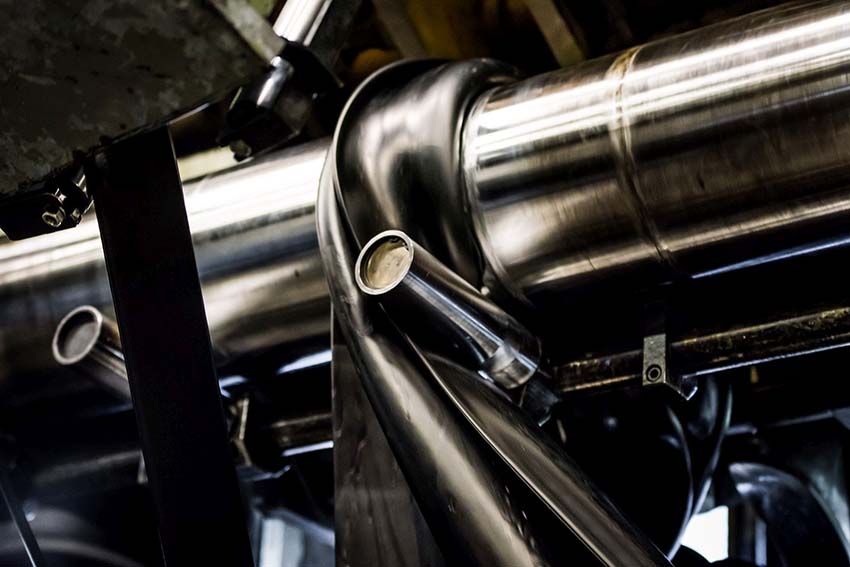
Don’t be fooled. Lower prices = lower quality rubber = shorter belt lifetimes
Manufacturers use a number of different methods to minimise productions costs and one of the most common concerns carbon black, which makes up some 20% of synthetic rubber. Good quality carbon black is an expensive commodity because it is produced by a process of burning oil in a strictly controlled, low oxygen environment. To create a much cheaper, lower grade form of carbon black, the practice of burning used rubber car tyres is becoming increasingly commonplace, especially for belts imported from outside of Europe. However, apart from the enormously negative impact on the environment, burning used car tyres means that the many undesirable chemical elements contained within this ‘regenerated’ material will have a detrimental effect on the physical properties of the rubber compared to good quality carbon black. Sadly, this is just one example of how some manufacturers are able to keep their prices so low.
This is precisely why the alarm bells should start to ring if there is a significant difference between the quoted prices for belts of apparently the same specification. The reason why the price of one belt can be 30% or 40% (or more) lower compared to another seemingly identical one is that there is a direct correlation between the price and the quality of the rubber. This is why some heat resistant belts are able to run and run without difficulty while others literally crack up and fall apart in a matter of weeks or months. It is a very old saying but it remains true to this day – you only get what you pay for!
Making your choice
When choosing a heat resistant belt, the most critical considerations are the actual temperature range of the material being carried and the type and nature of the material, both of which are inter-related. Materials with fine particles usually cause a greater concentration of heat on the belt surface due to the lack of air circulation between the particles. By comparison, even though the temperature of the material can be extremely high, larger sized particles of coarse materials allow a better circulation of air.
The actual loading of the belt is another important factor because if too much of the belt surface is covered by material there may be insufficient uncovered surface to allow the heat in the belt carcass to dissipate (escape). This almost inevitably leads to a build-up of heat within the covers and within the core of the carcass.
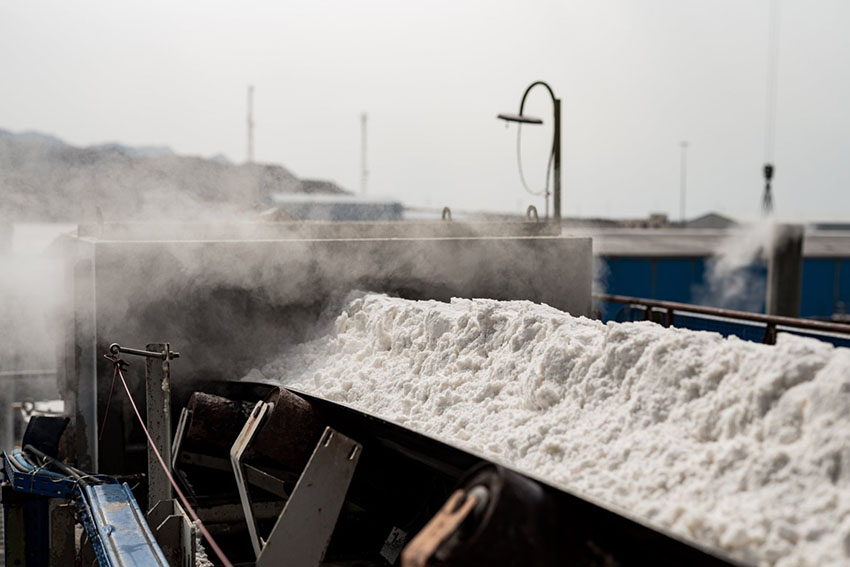
Avoid overloading – uncovered belt surface area allows heat to escape
This problem is even more applicable to conveyors that have a relatively short (less than 50m) center-distance length because there is less time for the belt to cool down on the return (underside) run. The running speed of the belt should also be taken into consideration.
Any belt fitted to a short conveyor will wear faster simply because it passes the loading and unloading stations (where materials are accelerated across the belt surface) more frequently than longer belts so having a heat resistant belt with good abrasion resistance is even more important than usual. Very hot, abrasive materials that are being conveyed at high speed on a short conveyor is the toughest combination of all and many heat resistant belts often last only a few weeks or months before having to be replaced. If this is happening to some of your belts do not simply accept the situation as being an inevitable consequence of a tough working environment. The fact is that there are heat resistant belts on the market that are capable of lasting two or three times (or more) longer than you are likely to have ever experienced before.
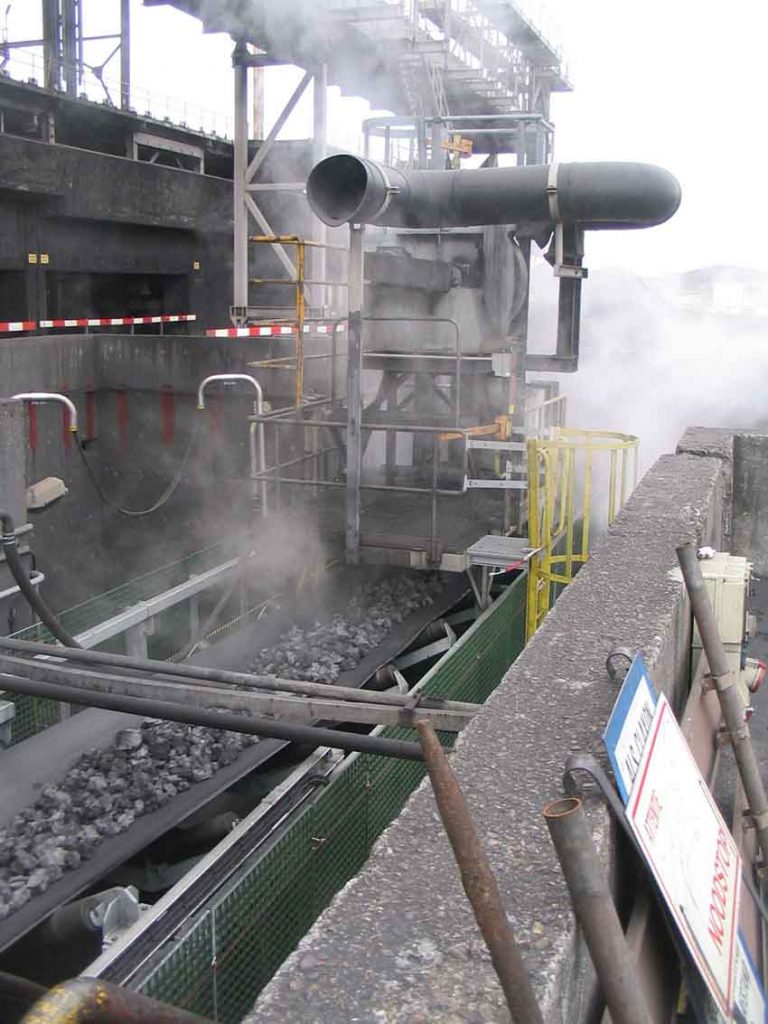
There are heat resistant belts capable of lasting two or three times (or more) longer than you may have ever experienced before.
Checking the data
It is always important to be as specific as possible when making requests for quotations from manufacturers and suppliers. Providing potential suppliers with accurate temperature data and material type is paramount. Even if the would-be supplier ignores the information, at least you will be able to show this as evidence in the event of a warranty claim. Another very important thing is to always request technical datasheets. However, be aware that with only one exception that I am aware of, virtually all manufacturers only provide technical datasheets that show (claim) the minimum required standards rather than the standards that the belt they supply can be expected to achieve. In many cases, technical datasheets can be very misleading because the impressive looking reference numbers shown on them usually only refer to the test methods used rather than the actual performance achieved during that testing. Sad to say that there can often be a very big difference between what is promised and what will actually be delivered.
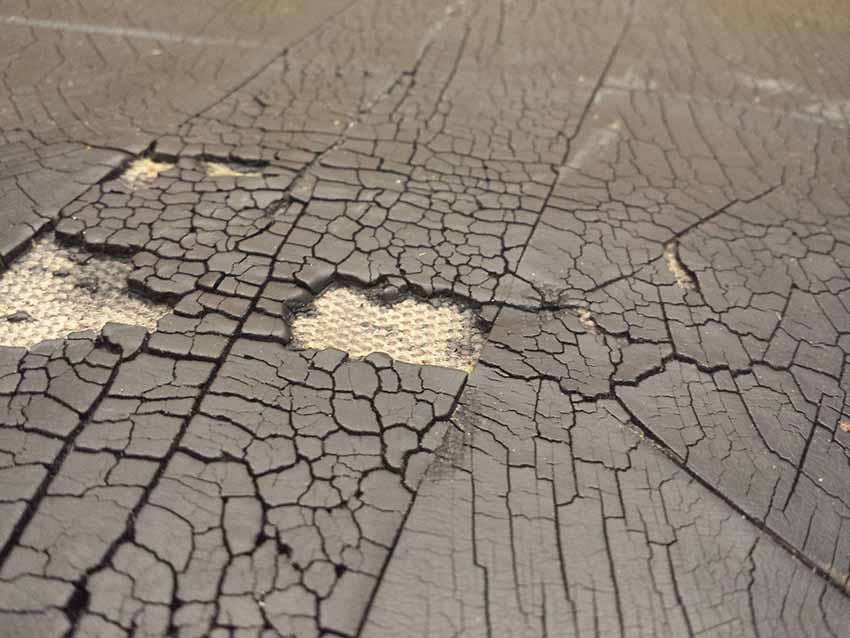
There can be a very BIG difference between what is promised and what is actually delivered
Never give up
My final message is this: Never accept that your belts can only ever be expected to last a short period of time. There is no such thing as a ‘sacrificial’ belt. If you go for genuine quality and work on the basis of lowest lifetime cost rather than lowest price then you will save yourself a lot of trouble and stress and a whole lot of money at the same time.
About the author.
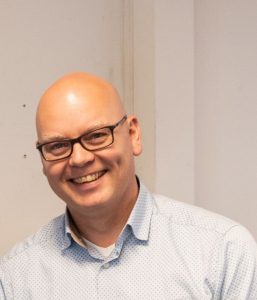
Rob van Oijen is Manager Application Engineering for Dunlop Conveyor Belting in The Netherlands. Rob has specialised in conveyors for some 14 years, supporting businesses throughout Europe, Africa, the Middle East and South America.