Founded in 1946, Bausano is an international leading player in the design and production of customised extrusion lines for the transformation of plastic materials. Quality, flexibility and attentiveness to the individual needs of every customer: these are the company’s distinctive features in developing tailor-made solutions for the extrusion of pipes, granules, profiles and WPC for a wide variety of applications, as well as material used in the medical sector.
On both the home and international market, Bausano is a strategic partner by virtue of its complete control over the value chain, a highly qualified pre-sales consultancy service as well as after-sales support with specialised operators, who are able to work on-site within 24 hours from the request, everywhere in the world.
The company’s headquarters are near Turin, it has 100 employees and a turnover of more than 20 million euro, and a widespread presence thanks to production units in Brazil and India and the commercial branch in the United States.
Easy Engineering: What are the main areas of activity of the company?
BAUSANO: We design and manufacture customised extrusion lines completely MADE IN ITALY for the production of pipes, granules, profiles, medical tubes, pockets and sheets in thermoplastic materials.
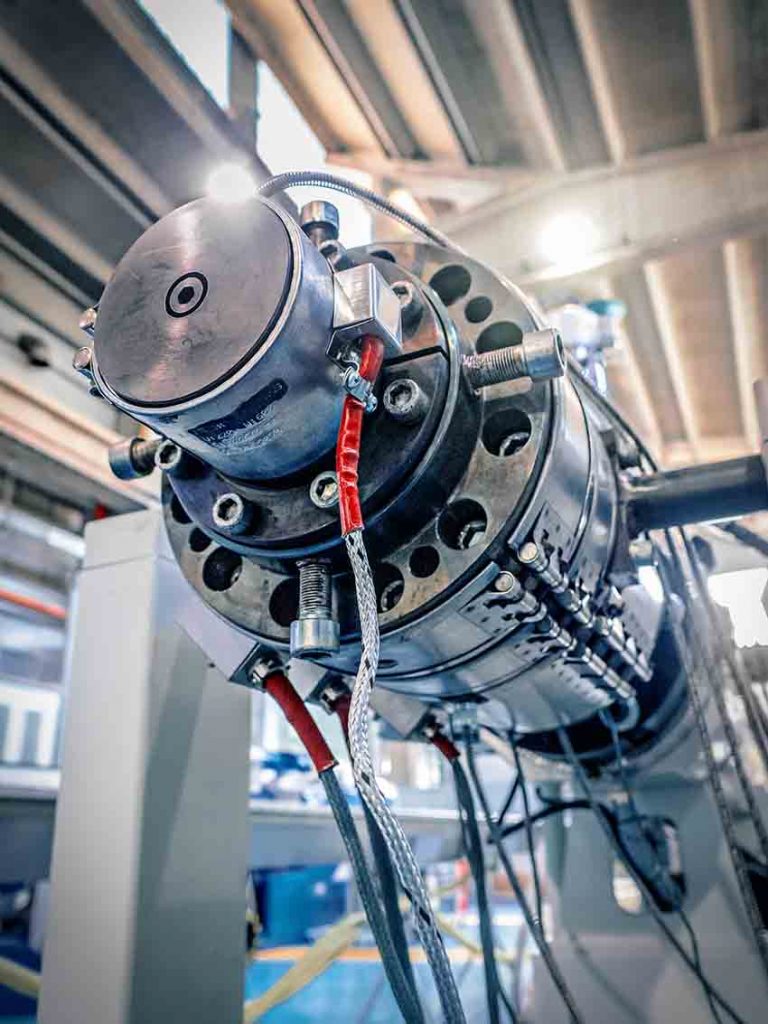
E.E: What’s the news for 2021 about new products?
BAUSANO: Bausano introduces E-GO in 2021: the renewed range of single-screw extruders for the production of PO pipes, resulting from the expertise of the Bausano technical Team, which has always designed solutions that stand for reliability and quality.
The E-GO single-screw technology makes it possible to obtain smooth, corrugated, multilayer or single-layer, rigid or flexible pipes, with a variable diameter from small size to large section, assuring excellent melt homogeneity of plastic materials such as PP, PP-R, PE, HDPE, LDPE, PE-X, PE-RT, PMMA, PC, PA and PU, ideal for a wide range of applications. Several sectors are concerned, namely from construction to infrastructure, laying water and electricity mains and gas pipelines, from agriculture to medical, up to the mining, oil industry and automotive. Compact, efficient and high- performance: E-GO pipe extruders stand out for the screw geometry which, in addition to featuring an ad hoc design developed on customers’ requirements, also introduces innovative solutions. This design choice makes it possible to obtain a high output in terms of Kg/hr of the machine and to process polyolefins without excessive mechanical stress. What is more, the specific design of both the screw and the cylinder, jointly with the low-input asynchronous motors, guarantee excellent energy efficiency. In addition to that, the solution is designed to assure operating continuity and a superior life cycle of the line, owing to the low wear of the components, which contributes to significant overall savings.
E.E: What are the ranges of products?
BAUSANO: Our Single-screw and Twin-screw extruders are suitable for:
- Pelletizing or regranulation line for different materials, mostly PVC;
- Production of PVC pipes and hoses, such as conduit, pressure and sewer pipe up to the agricultures hoses;
- Production of PP, PP-R, PE, HDPE, LDPE, PE-X, PE-RT, PMMA, PC, PA and PU mono and multilayer pipes;
- Production of the PVC, PE, HDPE, LDPE, PPR, ABS and PLA profiles, windows, decking, fencing and flooring, even those made in WPC (wooden plastic composite);
- Production of PVC and other non-toxic materials for sanitary use, like medical tubes, bags and sheets.
E.E: What can you tell us about market trends?
BAUSANO: The global demand for plastic pipes has grown exponentially and, over the next few years, is set to increase for a large variety of applications: from water and gas supply networks, rainwater drainage and the transport of various fluids to energy supply systems and sprinkler systems. In this context, Bausano – an international leading player in the design and production of customised extrusion lines for the processing of plastics – announces that it has completely revamped its ranges for the extrusion of soft and rigid, transparent, supercharged or press-filled PVC, PP and PE pipes in order to meet the ever-increasing demands of manufacturers for excellent melt homogeneity, flexible processes, maximised output and reduced energy consumption.
Worldwide, demand for polyolefin pipes (PO) is growing steadily thanks to their excellent physical and mechanical properties, able to outclass the performances of other materials. In this connection, they are emerging as the preferred choice for the construction of sewerage and drainage infrastructure, as well as networks for the Oil & Gas industry, eating away at the metal and cement market shares.

E.E: What are the most innovative products marketed?
BAUSANO: Made-in-Italy quality and ongoing technology innovation: this is the perfect mix behind the exclusive patent for MD Plus and MD Nextmover twin screw extruders from Bausano.
Our lines stand out for their unique transmission systems, a careful study of interpenetrating and counter-rotating screw geometry, the latest motors generation and consumption analysis tools, thus guaranteeing top production efficiency, sturdiness, reliability and sustainability.
Primarily, it is precisely the Multidrive technology that makes Bausano twin-screws unrivalled throughout the world. Evidence of years of research and experimentation, this transmission system undeniably reduces stress on motor shafts, gears and screws thanks to the tightening torque strain being distributed on two pairs of motors, resulting in higher power on screws, equal to the power delivered, with a positive impact in terms of both precision and energy savings. Compared to traditional systems, the distribution of motion also reduces the chance of faults due to excessive stress on mechanical components and ensures a longer average service life of the machine. Motors are managed by a single static frequency converter, an instrument capable of ensuring constant rotation and perfect synchronism, without using any additional devices.
Among the pluses of the lines, there is also the innovative Smart Energy System for cylinder contactless heating through an alternating electromagnetic field, resulting in a significant reduction in wear and energy savings of up to 35%. Finally, the new Digital Extruder Control 4.0, with its capacitive multitouch panoramic screen, performs continuous screening of the system by processing reports and graphs in real time, in order to easily and precisely analyse extrusion parameters and consumption at each stage of the production cycle.
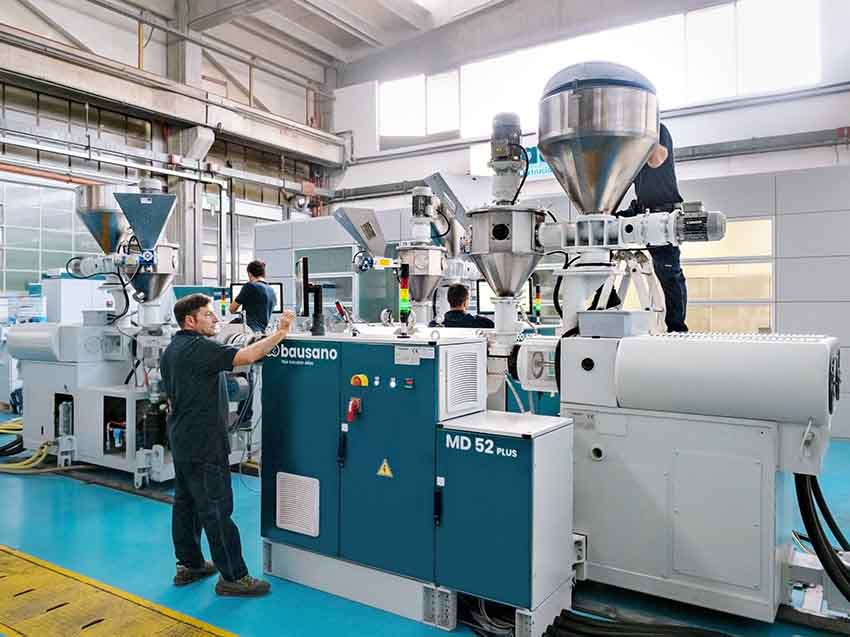
E.E: What estimations do you have for 2021?
BAUSANO: According to the recent study published by Market Research Future®, the global market for extruded plastics will reach a value of 281 billion dollars by 2025“, declares Clemente Bausano, who continues “If we consider the United States, the plastics processing sector is positioned as the eighth largest in the manufacturing world” and concludes “Strengthening the presence of Bausano in North America means, therefore, laying the foundations for a solid development in a dynamic sector, full of opportunities and needs, which we are ready to seize and fulfil”.
Bausano is implementing to effectively respond to the needs of North American customers: in fact, a structured training program for specialised technicians is underway at the Houston and Oswego dealerships, aimed at guaranteeing qualified and prompt assistance, centred around flexibility “and concludes: “Plus, in autumn, at the showrooms of our Resellers, a twin extrusion line will be installed, that operator in the plastics industry can watch in action and have a hands-on experience.