Sirmax Group, headquartered in Cittadella (Padua), is the leading independent European manufacturer (and among the top global manufacturers) of polypropylene compounds, engineering plastics, circular and bio compounds used across all sectors: Automotive, household appliances, power tools, household, construction and furniture. Active since the 1960s, it now has 13 production plants: Six in Italy two in Poland, one in Brazil, two in the USA and two in India, and has become a global benchmark for the international market. It is the supplier for the biggest automotive and home appliance OEMs, among others.
In 2020, the Group had a turnover of 315 million euros, employing 700 people worldwide. Total turnover for the first half of 2021 was 220 million Euros, with a forecasted turnover in excess of 400 million by the end of the year.
Interview with Marco Moretto, Director of Strategic Marketing at Sirmax Group.
Easy Engineering: What are the main areas of activity of the company?
Marco Moretto: Sirmax Group specializes in the production of polypropylene compounds, engineering plastics, thermoplastic elastomers, circular compounds, and bio-compounds for a variety of applications. It has now developed extremely high-performance green product families. Alongside its traditional “core” production of prime virgin materials, the Italian group has been able to produce enhanced plastic deriving from the mechanical recycling of post-consumer waste, making it usable as a durable good. This has been possible thanks to decades of experience and to the work of five Research Centers. The Group also offers molding solutions that reduce the use of virgin plastic and produces 100% biodegradable and compostable bio-compounds.
E.E: What’s the news about new products?
M.M: The state-of-the art of Sirmax Group’s new products is mainly focused on top-performing virgin products, circular compounds, and bio-compounds.
In terms of circular plastics, Sirmax’s experience in the field of prime virgin production means it is able to elevate post-consumer plastic and to create products that can be used for durable goods and high-performance automotive components, despite coming from waste. Sirmax’s added value lies in the plastic enhancement process. The company’s recycled compounds are enriched with mechanical and technical capabilities: Granules are combined with glass fiber, talc or other components, making the material just as resistant, performing and reliable as virgin plastic. This little “miracle” happens thanks to the Green ISO® family. This family includes Green ISOFIL®, Sirmax’s polypropylene compound, which can be made of up to 100% post-consumer resin depending on its final application. This excellent compound stands out for its ability to adapt to aesthetic and design applications. The Group’s R&D Labs have also developed a high-performance polypropylene compound whose post-consumer recycled content is also suitable for interiors and structural components. This special material is called GREEN ISOGLASS XT® and each granule encompasses all the best practices acquired from working with prime, high-performance virgin materials and applies them to circular compounds.
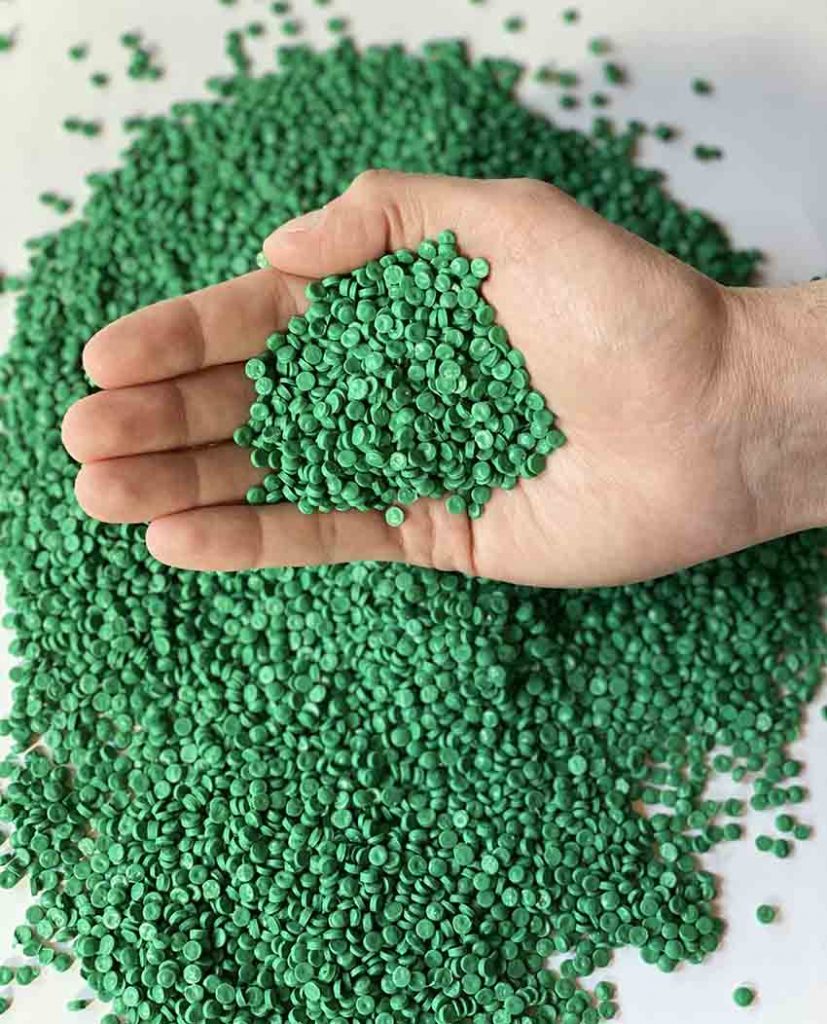
On the bio-compound side, the use of BIOCOMP®, an innovative family of bioplastics obtained from both renewable and fossil raw materials, is growing in several applications. BIOCOMP® is produced in granular form using known technologies for the transformation of plastic materials, which have been specifically adapted to treat biodegradable and compostable polymers. These granules can be used to make products with similar or even improved characteristics compared to traditional plastics. Unlike traditional plastics, however, they are completely biodegradable and compostable.
Although BIOCOMP® was initially used to produce standard packaging film (e.g. for shopping bags), its new and innovative formulations mean it has many applications in the flexible and rigid packaging sector, from large-scale distribution to the agri-food sector, catering, and disposable packaging for various uses.
E.E: What are the ranges of products?
M.M: At Sirmax we formulate more than 400 new products every year.
This is why we can offer a complete thermoplastic compound portfolio (both rigid and flexible) for different industries such as the automotive, home appliance, electrical & electronics and power tools industries, among others. Our experts work in collaboration with our R&D Departments to help our clients select the right material for their application. In the automotive industry, for example, we continue to successfully assist our customers through a co-design process aimed at reducing vehicle weight, lowering emissions and replacing metal parts – all while improving safety and durability with products suitable for interiors, exteriors and under the hood.
At Sirmax, we develop compounds for small and large players in the global home appliance market in collaboration with leading international manufacturers and their supply chains. The key to our growth is constant innovation, which supports our customers and continues to help drive their products to first-in-class status thanks to our outstanding quality and multi-country, multi-product delivery. Our portfolio consists of a wide range of existing UL approvals, technical compounds, thermoplastic elastomers and innovative circular products with a focus on R&D in order to improve cost, feel and end quality.
We also produce polyolefin compounds with mechanical and aesthetic characteristics suitable for the power tools industry. Moreover, we develop high-performance engineering polymers suitable for the production of tools subject to high stress, impacts, extreme temperatures and chemical exposure in domestic and professional/industrial settings.

E.E: At what stage is the market where you are currently active?
M.M: As far as the markets in which Sirmax Group operates are concerned, I must say almost all segments have recovered. During the pandemic we had to face raw material scarcity and a true logistics crisis. We saw the petrochemical industry grind to a halt due to lower demand for fuel. Prices increased sharply and an anomaly in the exports of raw materials from Europe led to complete stock depletion. But we did not get scared. The fact we had built a transparent, stable and – above all – regionalized supply chain played in our favor. It meant we did not have to depend exclusively on supplies coming from a single area of the world.
E.E: What can you tell us about market trends?
M.M: Currently, the most noticeable trend in the plastics sector in which we operate is to seek product performance while also considering the product’s environmental impact. Offering a product and a service consistent with these needs is one of the pillars on which the Sirmax Group is strongly focusing. The Group follows two main principles: Sustainability and client proximity. These guidelines have not only inspired our business through the difficult months of the pandemic, they have also become our claims. Proximity compounding is the vision that sets us apart. We see proximity as being not only our proximity to our clients’ needs, but also the desire to create a value chain based on a regionalized, loyal and solid supply chain. Our sustainable ideas are at the basis of our desire to create an ethical business that respects the environment and people. Over the last three years we have invested 80 million euros in our sustainable ideas and products.
E.E: What are the most innovative products marketed?
M.M: In addition to the range of innovative products already listed, Sirmax Group can count on the cutting-edge process innovation of Smart Mold. Smart Mold, Sirmax Group’s flagship brand, is an engineering company of the University of Padua – one of Italy’s biggest universities, with over 60,000 students a year. Sirmax acquired 50% of the shares following a capital increase in 2020. Smart Mold has two business activities. Its first, most innovative activity is to facilitate the processing of recycled plastics. The company has patented a surface treatment for the molds used in injection molding machines which makes filling molds easier by decreasing injection pressure. Recycled materials usually have a higher and more variable viscosity than virgin materials, which limits their applications. The Smart Mold patent, however, opens up new possibilities for post-consumer plastics, with a lower environmental impact.

Smart Mold’s second business activity focuses on reducing plastic consumption within a product by using raw materials with a higher added value. Smart Mold supports companies from the engineering design stage of the product, studying its applications (for example, the internal structure of a car dashboard) and the mechanical characteristics it requires (e.g. withstanding loads and shocks). It then uses advanced software to simulate the product’s mechanical behavior and recommends design solutions to reduce its weight and the amount of plastic used. Thanks to its expertise, Sirmax is able to provide optimized materials for each application, accurately profiled for the required engineering process. By combining Sirmax’s most performing materials and Smart Mold’s surface treatments, the thickness of many structural components can be significantly reduced, leading to a reduction in weight and in the consumption of virgin plastic.
E.E: What are your predictions for 2022?
M.M: I see a good trend, a balance that will continue in 2022. As far as Sirmax is concerned, we will continue to work on new initiatives and new products that stand out for their innovation and allow us to offer different solutions to those offered by our competitors. Innovation and development will therefore play an increasingly important role within the group, alongside strategic marketing to anticipate new market trends.