For more than 30 years, SKS Welding Systems has been known as a reliable system partner for robotic arc welding. The company’s innovative power, combined with a forward vision and customer-oriented development work, has allowed them to establish an excellent reputation throughout the industry. As leading innovators, they develop welding machines, processes and torch systems that sustainably expand the possibilities of automated robot welding.
The company’s concept: The combination of a modularly designed welding machine made of high-performance components with a functional torch series for single wire and dual wire welding. Their systems are complemented by flexible software solutions for the documentation of welding data – from a stand-alone operation to network-integrated solutions.
All of their welding machines and torch systems are compatible with all common welding robots. What makes the products unique is their high reliability and long service life – because if there is one thing SKS Welding Systems doesn’t want, it’s a thriving repair and spare parts business.
Easy Engineering: What are the main areas of activity of the company?
SKS WELDING SYSTEMS: SKS welding machines are used by well-known manufacturers in the automotive and supplier industries: OEMs, Tier 1 and Tier 2 suppliers, producers of exhaust systems, seats, chassis, battery trays and car bodies.
E.E: What’s the news for 2021 about new products?
SKS WELDING SYSTEMS: pReam – Pneumatic cleaning station for the cleaning of gas nozzles.
We started with eReam, a fully electrical driven cleaning station, using reamer blades. The market also called for pneumatic solutions, so we have expanded our product portfolio to include a pneumatically driven cleaning station for the cleaning of gas nozzles.
pReam contains a wire cutter and an injection unit. It can be finely adjusted to optimize the cleaning process, and can also be programmed easily and flexibly, as the control system is already included.

Wire Guidance FlexiGlide
The quality of wire feeding is an important factor in robotic arc welding. Our new wire guidance is made from high-alloyed Chrome/Nickel spring-steel with a high flexibility and outstands with its reduced surface friction. The constructive base, a spiral with a plastic type sheath results in a robust product with a high lifetime.
It is optimized for use in robotic applications, has an extended work life, a very good sliding property, is flame retardant and abrasion resistant, and has a lower wire pull resistance.
E.E: What are the ranges of products?
SKS WELDING SYSTEMS: Development, production and distribution of:
- Welding machines and components for automated or robot welding;
- Welding torch systems;
- Process development for MSG (single wire, double wire) and MIG soldering;
- Development of software/IT for welding applications.
E.E: At what stage is the market where you are currently active?
SKS WELDING SYSTEMS: One of the key drivers for the robotic welding is the global automotive industry. Robotic Welding Market was valued at USD 3.81 Billion in 2018 and is projected to reach USD 7.40 Billion by 2026, growing at a CAGR of 8.67 % from 2019 to 2026.
E.E: What can you tell us about market trends?
SKS WELDING SYSTEMS: Industry 4.0 forces a rapid technological change in all robotic driven industries. Advanced communication technologies, ubiquitous internet in all devices and the possibility to process big data analysis in cloud services will be a advent of new possibilities for the welding industry. With smart sensors, customized weld data, welders and fabricators get better insights to optimize welding processes, enhance production with improvements in efficiency and productivity, additionally, are able to implement predictive maintenance.
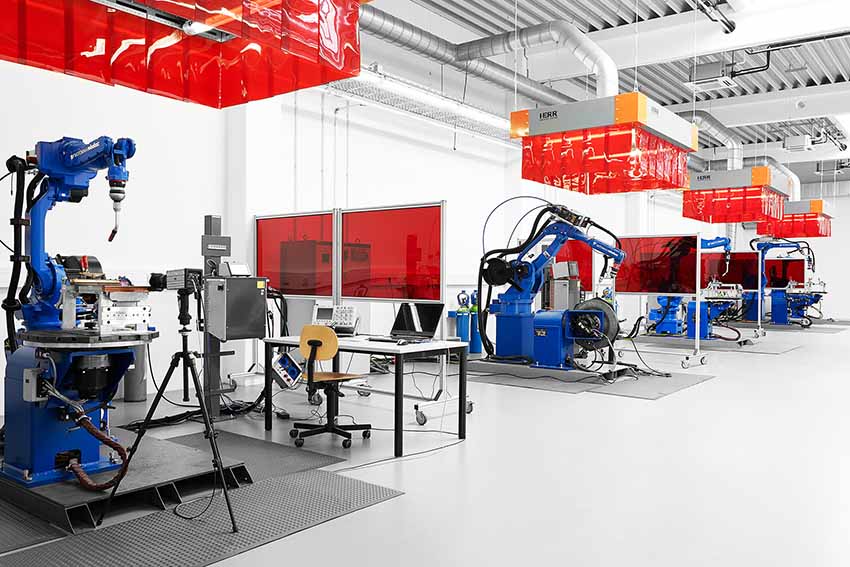
E.E: What are the most innovative products marketed?
SKS WELDING SYSTEMS: Power Joint torch system: The Power Joint torch system perfects the interaction of the welding machine and robots with an internal torch cable. It increases uptime and reduces cycle time. The rotating joint of the Power Joint rotates without limit (even beyond 360°) and supports the transmission of power, gas, air and wire.
Decoupling the torch cable from the torsional movements eliminates any torsional strain on the cable – significantly increasing the lifetime of the torch cable. The elimination of reorientation movements saves time; the torch reaches any point by the shortest possible way.
With the development of the Power Joint, SKS set a new industry standard: Meanwhile, over 16,000 Power Joints are successfully operating under industrial conditions worldwide.
The Frontpull torch systems enhance quality and performance of robots with outer and inner cable dress. This applies to the process control speed and dynamics as well as the seam quality, time savings during programming and during welding operation – and also to a longer service life of consumables, and this is true even in difficult operating conditions as with the use of soft wires from a coil. Frontpull allows a new weld processes: microMIG and microMIG-cc. The basic principle of these processes is a mechanical droplet detachment with or without pulses in-between. Both are the ideal for controlling heat input and penetration depth. These weld processes are much cleaner, resulting in less maintenance and are practically spatter-free so less rework lowers production costs.

E.E: What estimations do you have for 2021?
SKS WELDING SYSTEMS: SKS extends its worldwide network of subsidiaries. Worldwide, the number of industrial robots is growing rapidly. Based on data of the IFR (International Federation of Robotics), the operational stock of robots (Welding and Soldering of all materials) was around 450,026 units in 2015. By 2019, 637,936 welding robots were working worldwide. Automotive companies and their suppliers are still the main purchasers of industrial robots. Their main area of application is welding. The resulting demand for planning, consulting and other services for automated, highly productive, highly reliable and highly available arc-welding technologies is where SKS Welding Systems GmbH comes in. To meet this demand, SKS is currently extending its global organization.
2021 with a new subsidiary in Russia.

SKS WELDING SYSTEMS GMBH
Marie-Curie-Strasse 14, 67661 Kaiserslautern, Germany
Phone: +49 6301 7986-0
Fax: +49 6301 7986-119
Email: info@de.sks-welding.com
Website: www.sks-welding.com