The vast majority of rubber used to manufacture industrial conveyor belts is synthetic. That is because synthetic rubber can be engineered for specific demands and is far more adaptable compared to natural rubber. This is vitally important when you consider the wide variety of working conditions and materials that they have to cope with. It is the quality of the rubber covers, in particular the ability to resist wear and tear, which has the biggest influence on the durability and operational lifetime of a conveyor belt.

Pouring money down the drain – an enormous proportion of conveyor belts fail to provide a cost-efficient working lifetime
Sad to say however, an enormous proportion of conveyor belts fail to provide a cost-efficient working lifetime simply because the rubber used to make them is of insufficient quality. The reason for this is that rubber usually forms at least 70% of the volume mass of a conveyor belt and more than 50% of the cost. With most conveyor belts being sold on the basis of lowest selling price rather than performance and durability, the rubber is therefore the prime target for minimising costs. The outward appearance may seem perfectly okay but how can you tell if the rubber is poor quality? Fortunately, you do not necessarily need to be a conveyor belt expert to identify some of the tell-tale signs. You just need to use your senses.
Something smells wrong
One of the first clues is smell. All European manufacturers are legally obliged to comply with REACH (Registration, Evaluation and Authorisation of Chemical substances) regulation EC 1907/2006, which came into force in June 2007. The regulations relate to the use of potentially hazardous chemicals that pose hazards to human health and the environment. This includes those that may have category 2 carcinogenic classifications as well as Persistent Organic Pollutants. Sadly, many European manufacturers have chosen to ignore this legal requirement because of the impact on production costs while manufacturers in Asia, the source of a huge proportion of the conveyor belts sold in Europe, are not subject to the regulations at all. This means that they are free to use unregulated raw materials that cost much less on the global market compared to their regulated counterparts, even though those materials may be prohibited or have strict usage limitations within Europe.
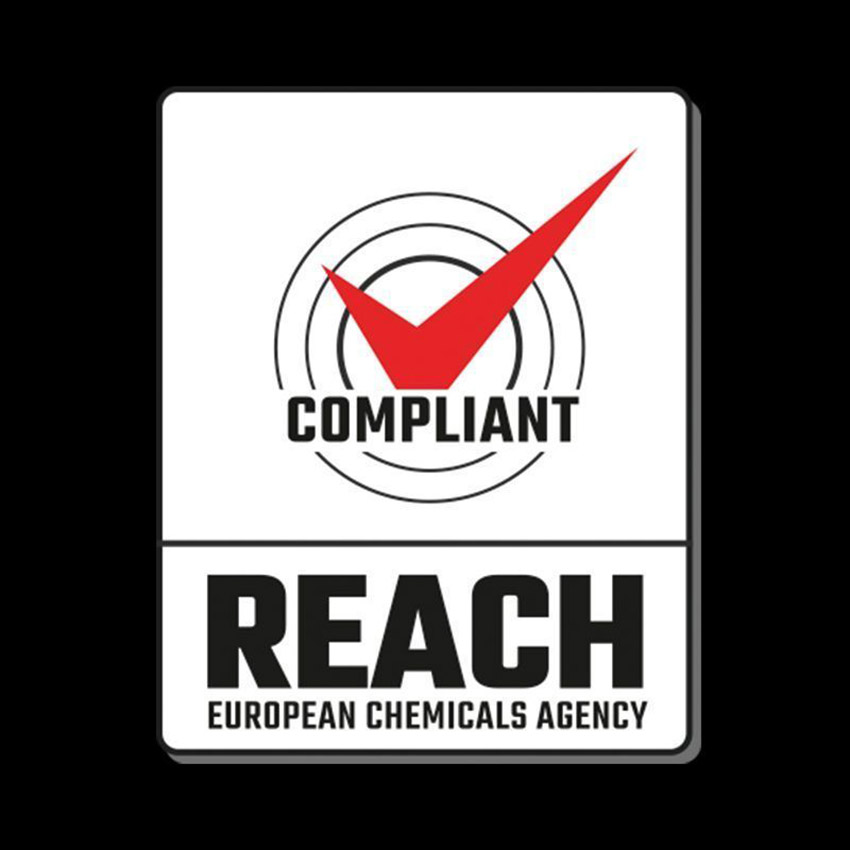
Asian manufacturers are not subject to EU regulations concerning the use of dangerous chemicals and pollutants
One of the biggest concerns involves short-chain chlorinated paraffin’s (SCCP’s), which are most commonly used to reduce production costs by accelerating the vulcanisation process. REACH regulations stipulate that SCCP’s should either not be used at all or at least only used on a very restricted basis because of their category 2 carcinogenic classifications. The tell-tale sign of their presence is usually recognisable due to an unpleasant pungent odour given off by the rubber whereas good quality rubber usually has very little smell at all.
Hearing the difference
Perhaps an even more surprising way of identifying poor quality rubber is sound. Belts with good quality rubber covers tend to run appreciably quieter than their lower-grade counterparts. A key component contained in every black rubber conveyor belt is carbon black. It makes up around 20% of a typical rubber compound and good quality carbon black is an expensive commodity. Carbon black plays a vital role in prolonging belt life by helping to conduct heat away from the surface area of the belt, thereby reducing thermal damage. It also acts as a reinforcing compound. Belts offered with significantly lower prices are virtually certain to contain carbon black that is of a much lower quality that has been produced much more cheaply such as by burning scrap car tyres for example. Other methods used to minimise rubber costs include the use of recycled rubber of highly questionable origin and cheap ‘bulking’ fillers such as chalk, which are used to replace part of the more expensive rubber polymers. The end result is that the rubber is more rigid and less flexible, causing the belt to emit a constant loud rumble. There is also a tendency to slip, causing loud squealing sounds.

Poor quality rubber is less flexible, causing the belt to emit a constant loud rumble
In contrast, higher quality rubber contains much higher proportions of top grade polymers and premium quality carbon black. As a consequence, rather than being rigid, the rubber is much more elastic, which helps to reduce its rolling resistance because it ‘conforms’ more easily. This means that it requires less drive power and makes less noise because the sound is dissipated as the belt surface passes over the rollers. Good quality rubber also has more grip so it is less prone to slipping under tension at the head. A perfect example of this was discovered recently by one operator who, after replacing their low grade imported belting with belts produced by Dunlop Conveyor Belting in The Netherlands, found that the noise level of their conveyors dropped by at least 50%.
Common sense
When trying to differentiate between what is likely to be good quality, more cost-efficient belts and low grade, short lifespan belts, perhaps the best sense of all is good old-fashioned common sense. As I said earlier, rubber usually forms at least 70% of the volume mass of a conveyor belt and more than 50% of the cost. When there is a big difference in the price of one conveyor belt and another, invariably the best tell-tale sign of all is that the price reflects the quality and longevity.
Autor: Bob Nelson
Authors note: Please be aware that the level of noise emitted by a conveyor can also depend on other factors such as the quality of the infrastructure, maintenance, type and condition of other integral components such as rollers and/or general operating conditions. Consequently, a reduction in noise level cannot be guaranteed simply as a result of changing your belt to a premium quality band such as Dunlop. For more advice on this subject please consult an experienced application engineer.